Magnetti Building cuts the time needed for precast projects design and construction by 20% and reduces the number of errors in fabrication and construction by 80%.
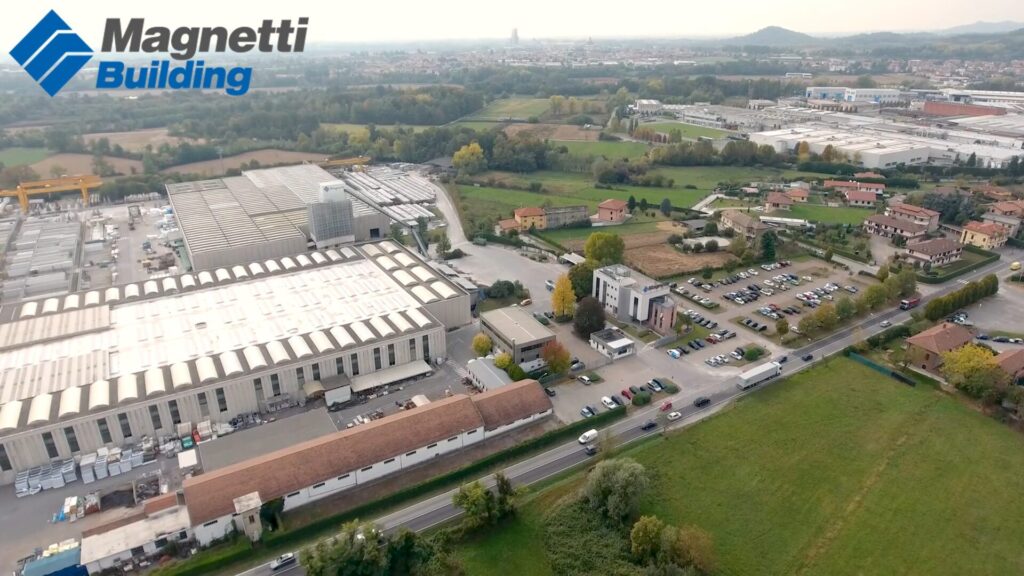
It’s not often when companies update their processes. But, when they do, significant changes are planned with the goal of improving one or several success metrics. Processes are all about how resources work together to get the needed outcomes, and in the precast concrete industry, there are many processes. The most straightforward is the manufacturing process, which refers to how the concrete is poured on top of the reinforcement and any other embedded elements. But to get here, another important process has to happen first: the design for fabrication of the precast elements.
What also does not happen often is the openness of a firm undergoing such changes to agree disclosing how this is unfolding. But Magnetti Building, one of the largest Italian precast fabricators, believes that the industry they act in must improve and, given their two-century-old DNA in the construction industry, they have a responsibility to lead by example. They offer integrated planning and operational skills to provide complete, turnkey solutions with a low environmental impact for projects, from logistics centers to industrial and commercial buildings, hotels and accommodation facilities, and more.
Having already delivered more than 24,000,000 sqm. (258,000,000 sq. ft.), how could they upgrade while still making new buildings for their customers? Let’s take a look at how the CAD to BIM migration improves several of Magnetti’s processes.
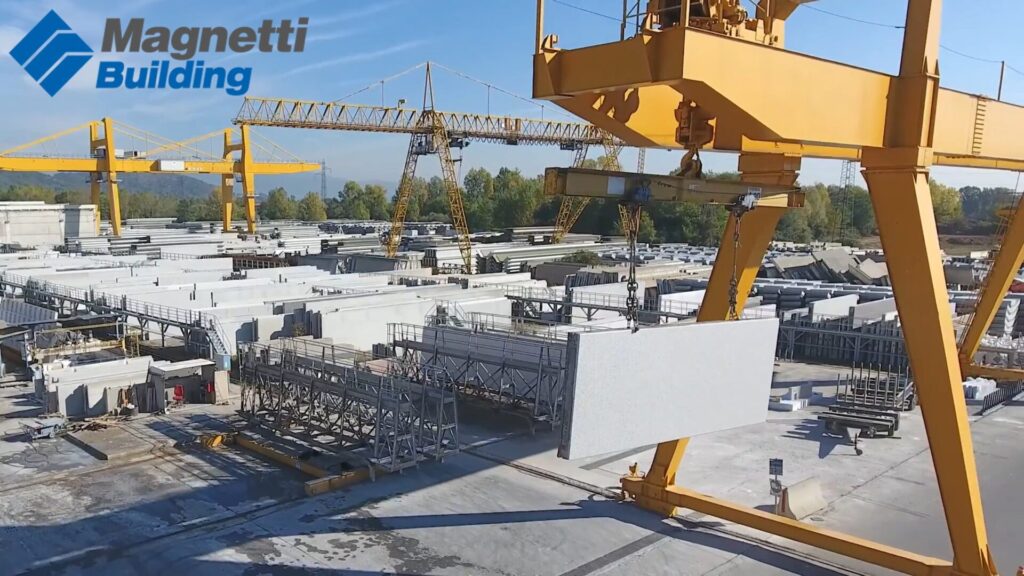
Roberto Volpi, Engineer and Project Manager at Magnetti Building, says there were several reasons for the company to switch from CAD-based solutions to Revit for designing and modeling precast buildings: faster and more accurate design, better collaboration, as well as optimized logistics and fabrication.
Magnetti delivers many types of precast elements, such as columns, individual foundations, façade panels, TT-slabs, and roof panels. To efficiently model them according to the exact fabrication requirements specific to Magnetti’s production line, they turned to Massimo Speziani’s Precast Designer for Revit, a tool to design, analyze, and produce precast elements.
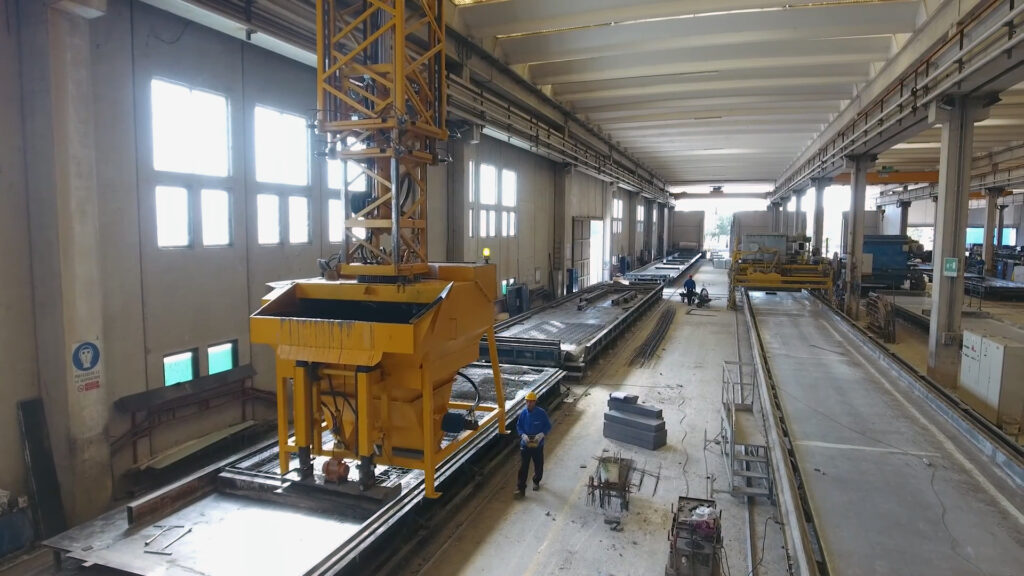
Since the design of projects couldn’t stop during the transition to Revit, Magnetti opted for a multi-step migration. In phase 1, they started using the Precast Designer for Revit to model accurately for fabrication. For roofs and façades, they use the rule-based automatic segmentation to define planar precast elements. Mounting parts and many other types of embeds are automatically placed as well. The placement of such items can be optimized using bidimensional nesting and other customizable area rules. What’s even more useful is that by having this automated routine, engineers can quickly iterate through several options, using different types of embeds from several providers and selecting the most cost-effective solution.
The design and detailing of complex curved precast elements have also been improved due to this transition. Such panels are used for creating aesthetic, yet easy to build, roofs for various types of buildings.
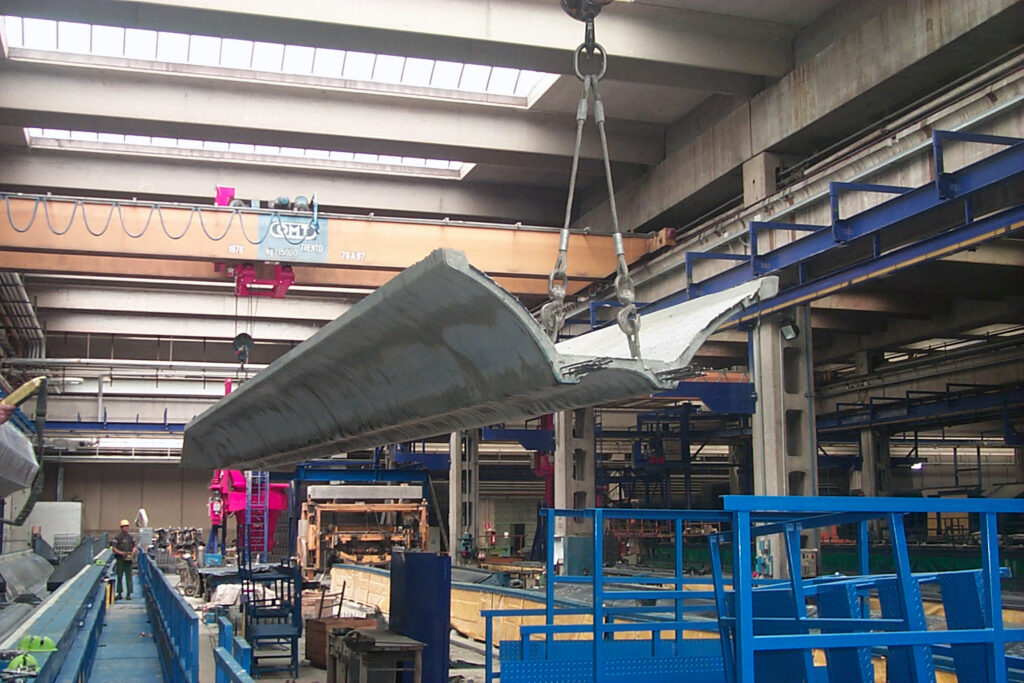
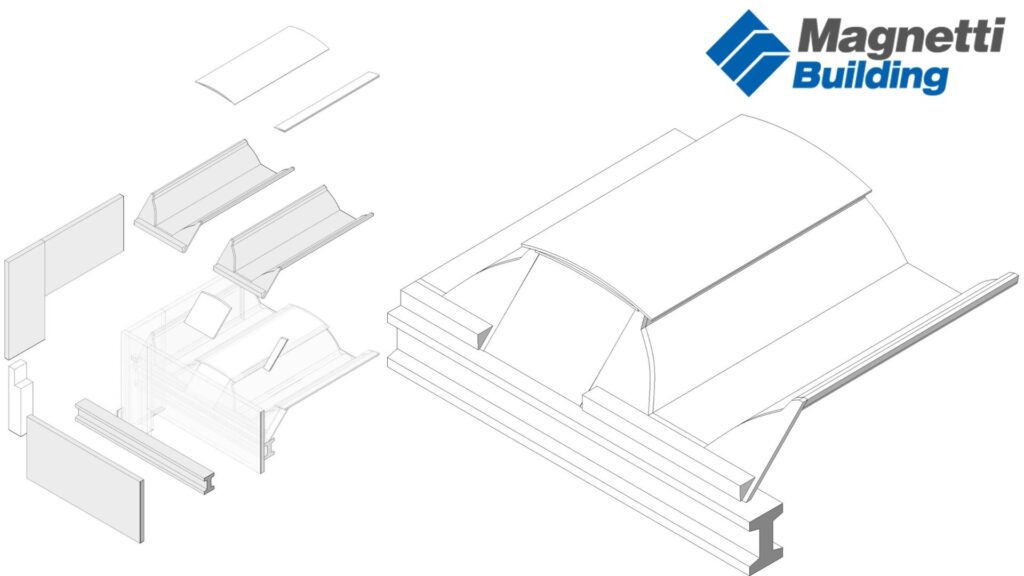
Another useful feature for Magnetti is the ability to assign different materials to the finished surfaces of the panels. This helps them strengthen a key competitive differentiator of delivering unique designs based on their pre-finished elements, which have better build quality and durability compared to the in-situ created ones and help reduce the overall construction time.
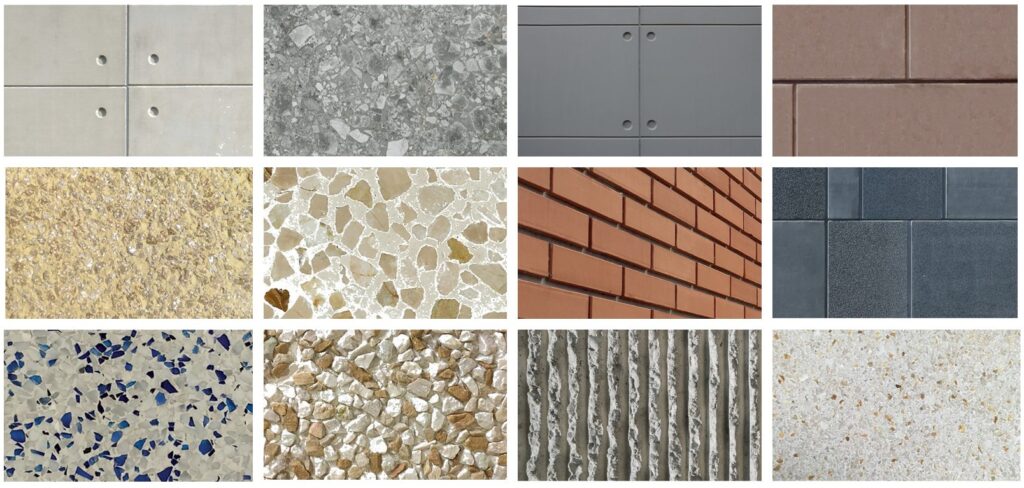
To ensure that on-site assembly of precast elements goes according to plan, various tolerances are embedded in the modelling process. Every panel edge can have a different tolerance. Using Revit’s capabilities of respecting the different perspective of each persona, the architectural model coexists without displaying these offsets. Notice in the two pictures below what the 3D view used by architects looks like, compared with the one used by the precast detailers.
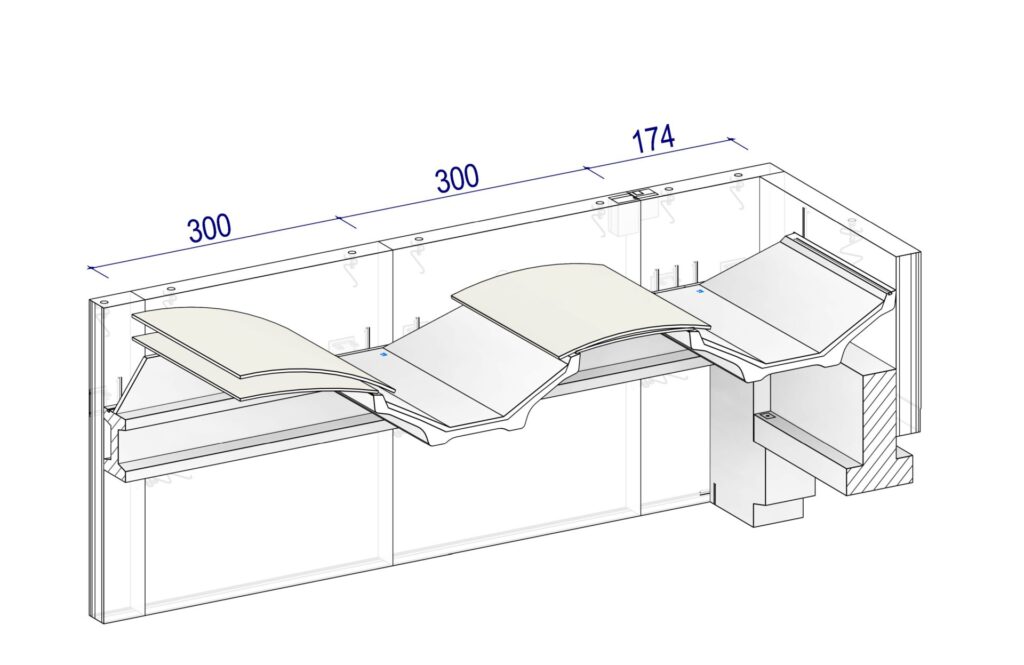
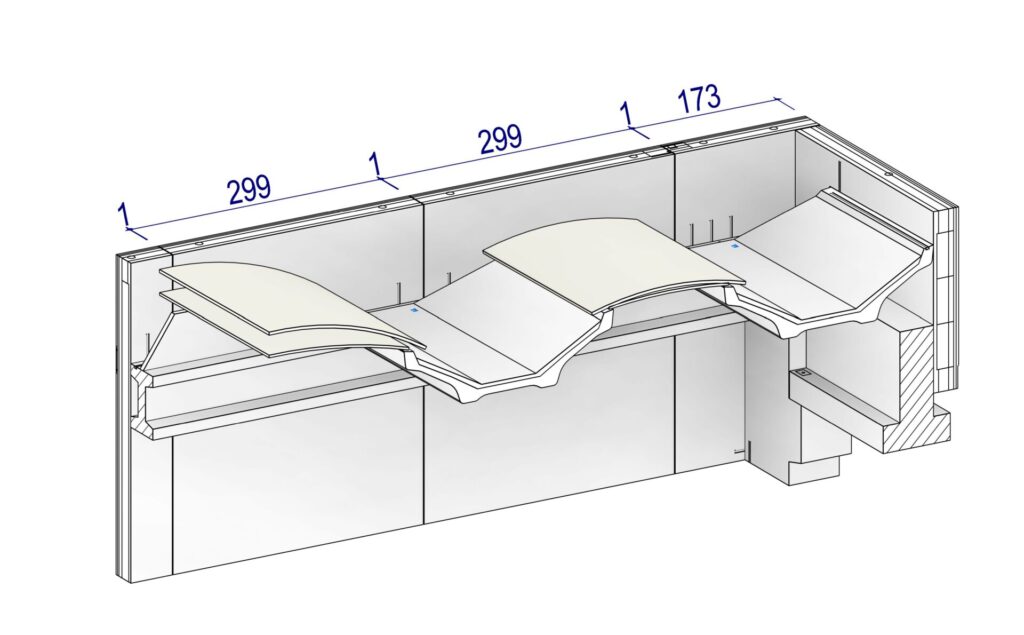
The Precast Designer for Revit manages this using parts and detail levels for the Revit families. Moreover, it can automatically model various customizable chamfers, edge profiles, and special embeds.
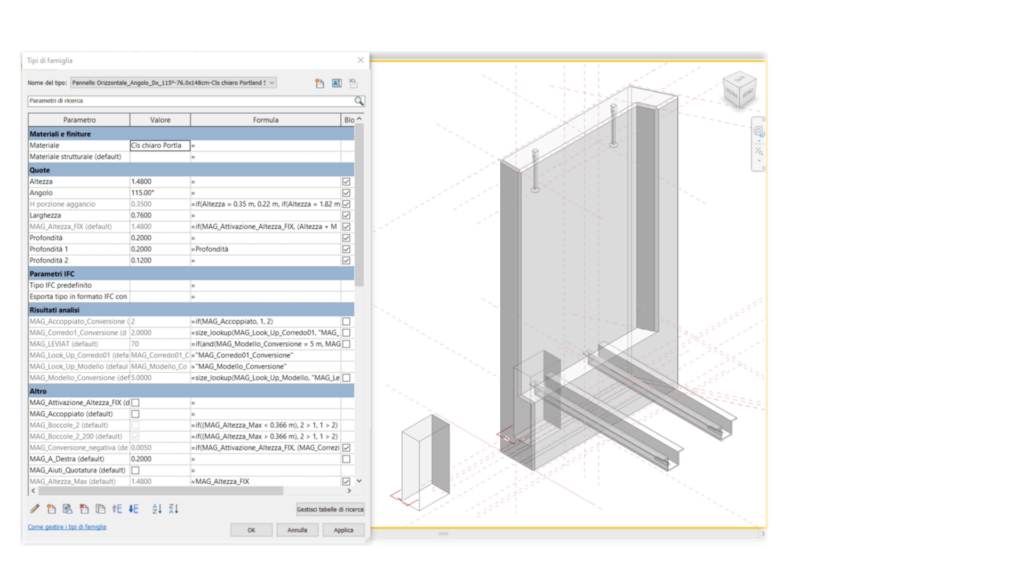
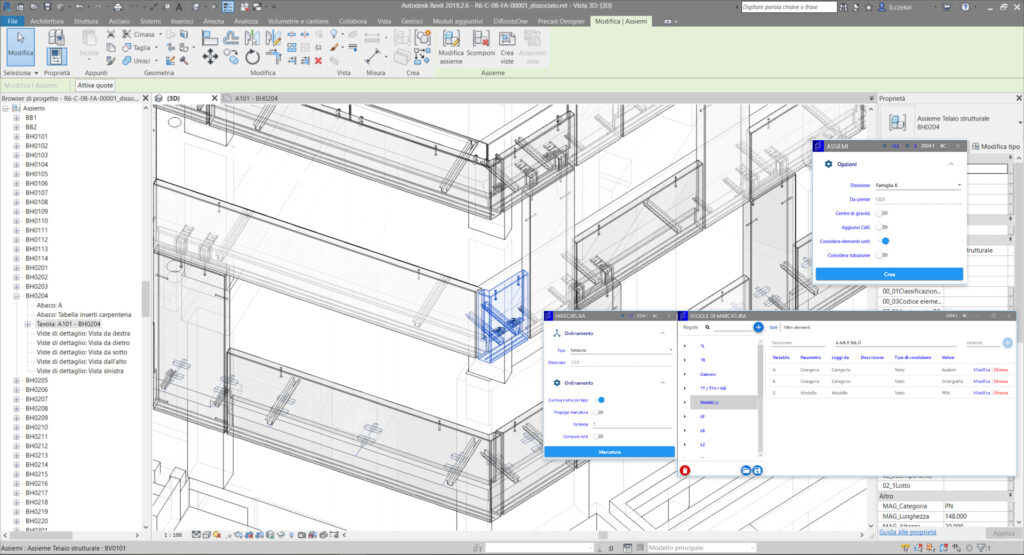
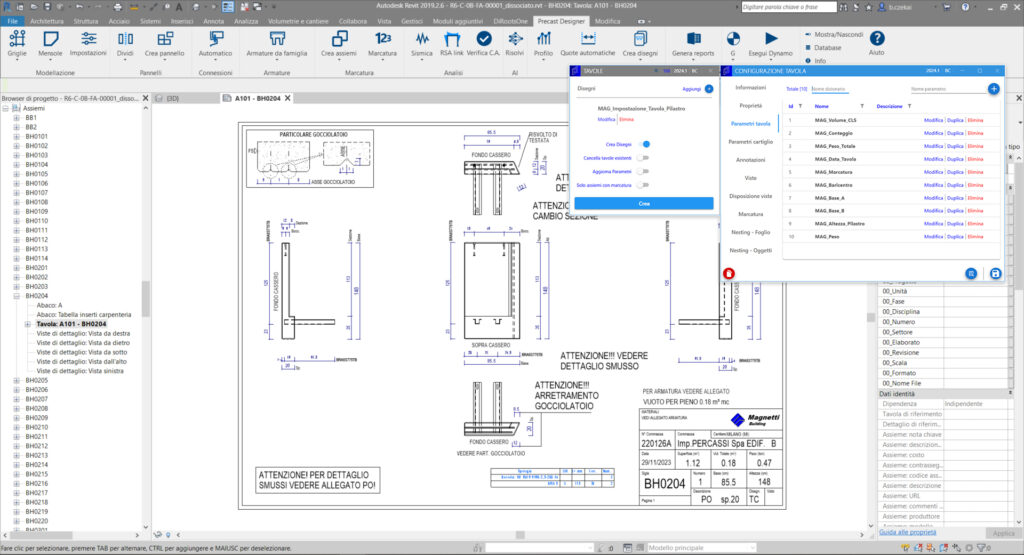
Next, using the Precast Designer for Revit, the panels are numbered based on customizable rules with embedded tolerances when comparing very similar instances. For example, the entire geometry of an element and its embeds can be used as the criteria for identifying identical elements, or one can also factor in the differences between different parameters. And, because the precast industry has so many diverse methods, one can even keep track or disregard the differences between the embedded items in a precast element.
The final step of the modelling and detailing for fabrication stage consists of creating the deliverables for the factory. Magnetti owns both the design and the fabrication of the elements, which makes coordination between the teams owning these two processes easier. Still, to produce high-quality products, high-quality shop drawings are needed.
The Precast Designer for Revit generates automatic shop drawings according to Magnetti’s standard, as it leverages Revit’s Structural Precast API, to extend its native capabilities. The layout of each sheet and how elements are dimensioned and labeled are configured such that the drawings look similar to the ones Magnetti had been creating using CAD technologies.
A special feature of the app is the ability to digitally sign each sheet using the blockchain technology. Magnetti sees a lot of potential in this, as it would enable them to have an improved management of revisions and is one of the key components of an integrated traceability system. An example of use is the management of paper documentation. This system ensures that the most recent documentation is used. The technology is integrated with the drawing configuration. Every time an element is ready for production the assembly is locked and a blockchain hash is generated and saved in the QR code.
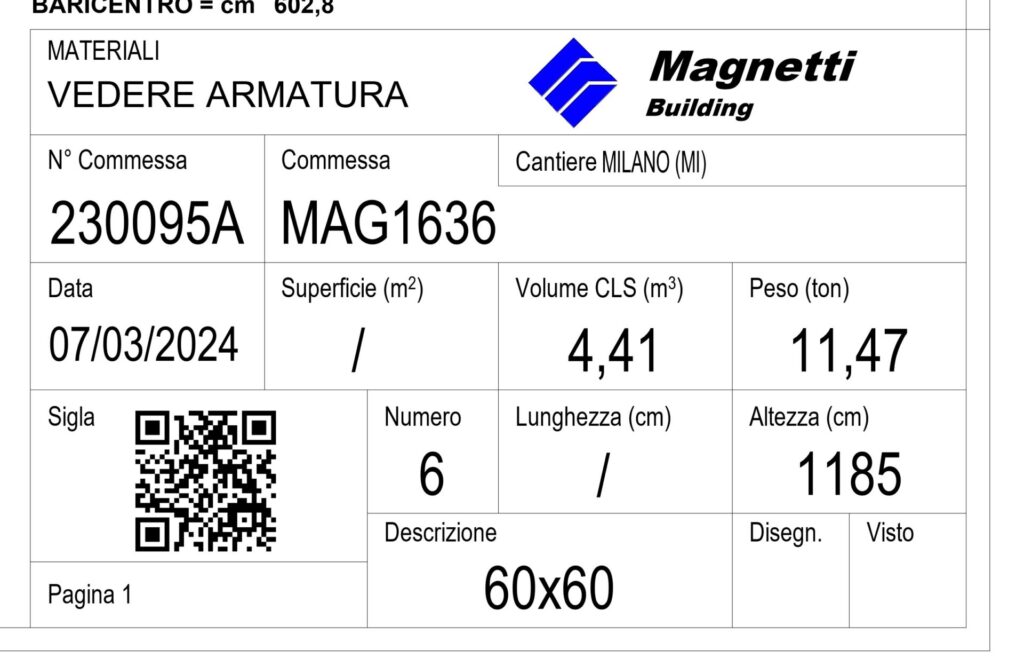
As I mentioned in the beginning, Magnetti is implementing the CAD to BIM migration across several phases. Phase 2 has recently started being rolled out, and it has brought about substantial enhancements. Across their innovation-driven projects, the reinforcement is now automatically generated based on structural analysis results, which the Precast Designer for Revit can read from Autodesk Robot Structural Analysis Professional, Autodesk Structural Bridge Design, and any other structural analysis software that can exchange analysis results with Revit.
For framing elements, the reinforcement and the pre-stressing strands are created. The connections between the planar elements and between columns and beams will also be automatically generated.
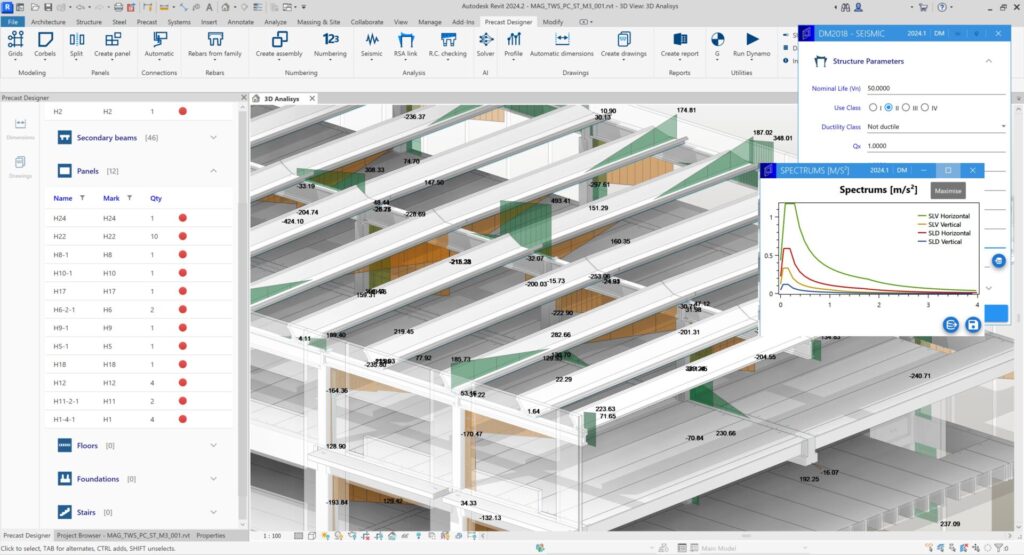
If multiple results packages are available from Robot Structural Analysis Professional, the Precast Designer for Revit allows you to choose which one should be used for code checking.
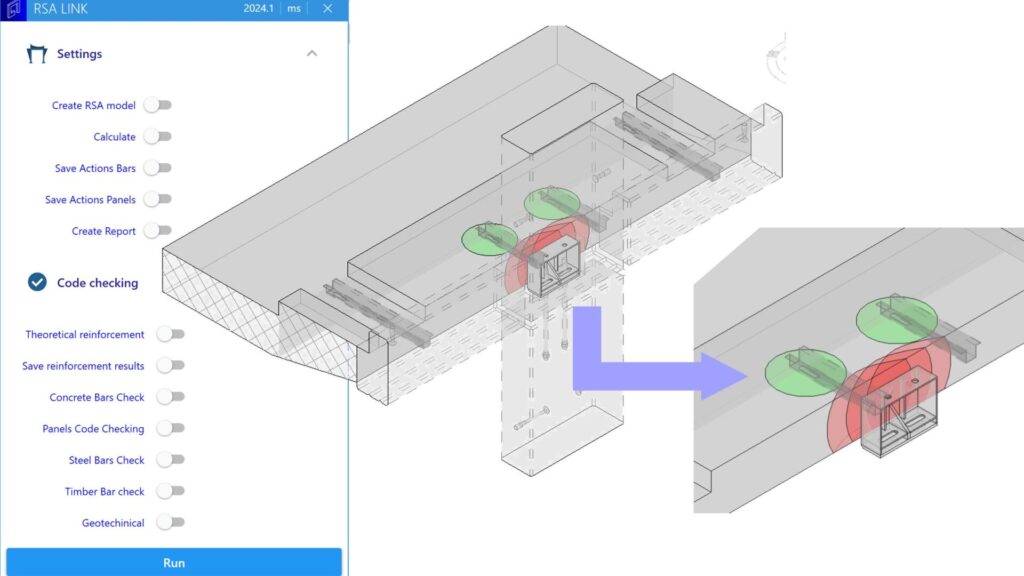
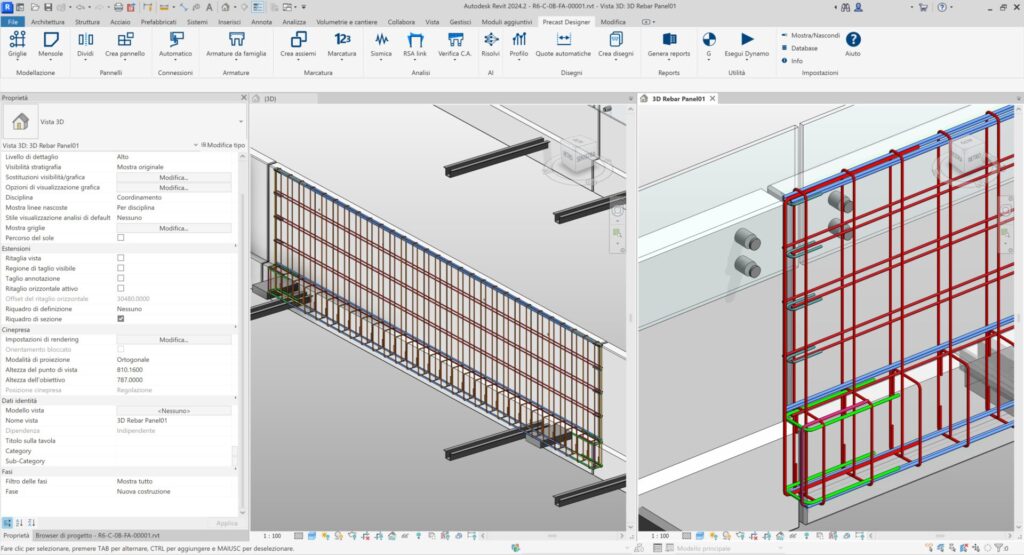
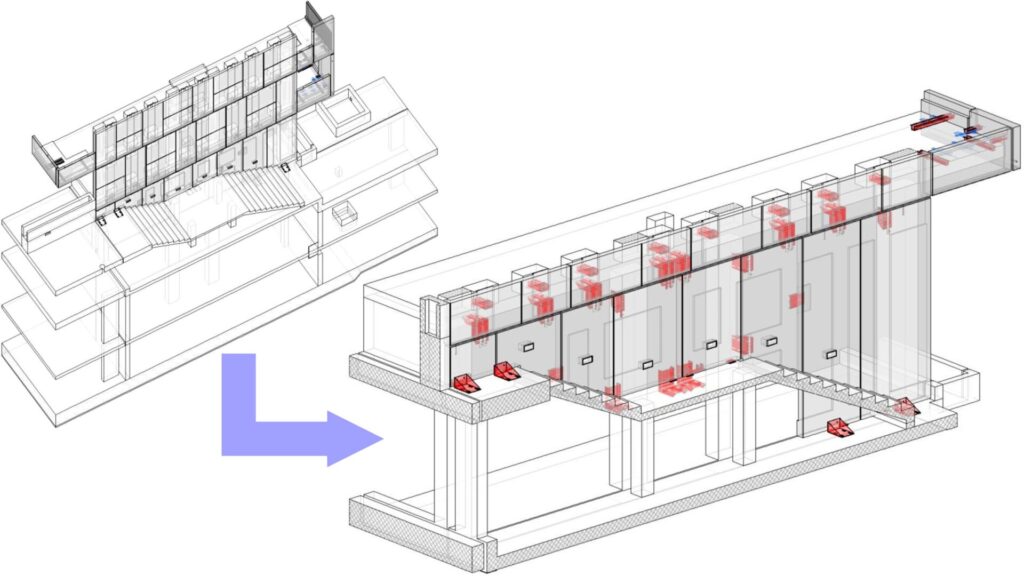
Using Revit’s comprehensive set of annotation tools for shop drawings, including bar bending details and precast drawings automation engine, the Precast Designer for Revit helped Magnetti automate their element shop drawings per their factory standard, as well as detailed drawings of the connection pieces used to link the precast elements.
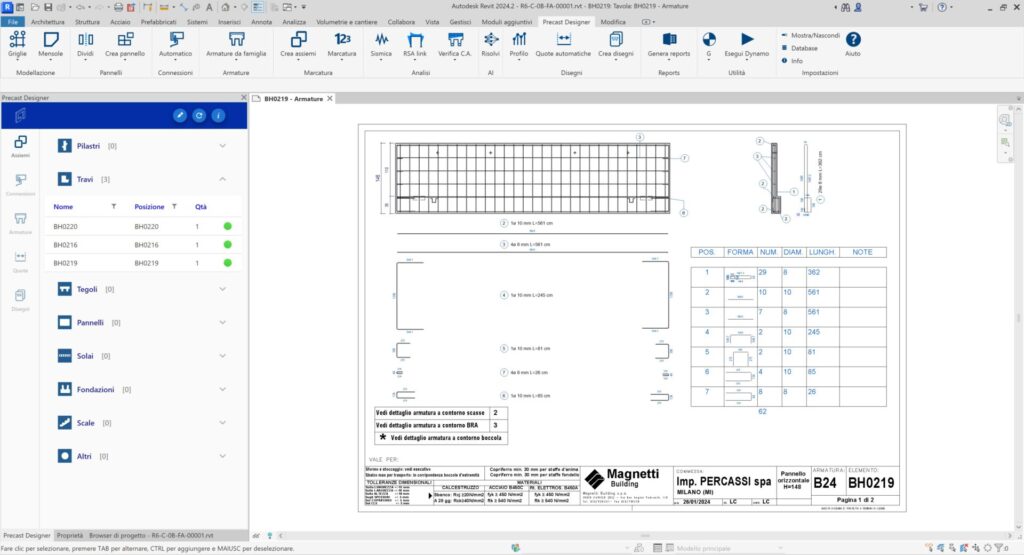
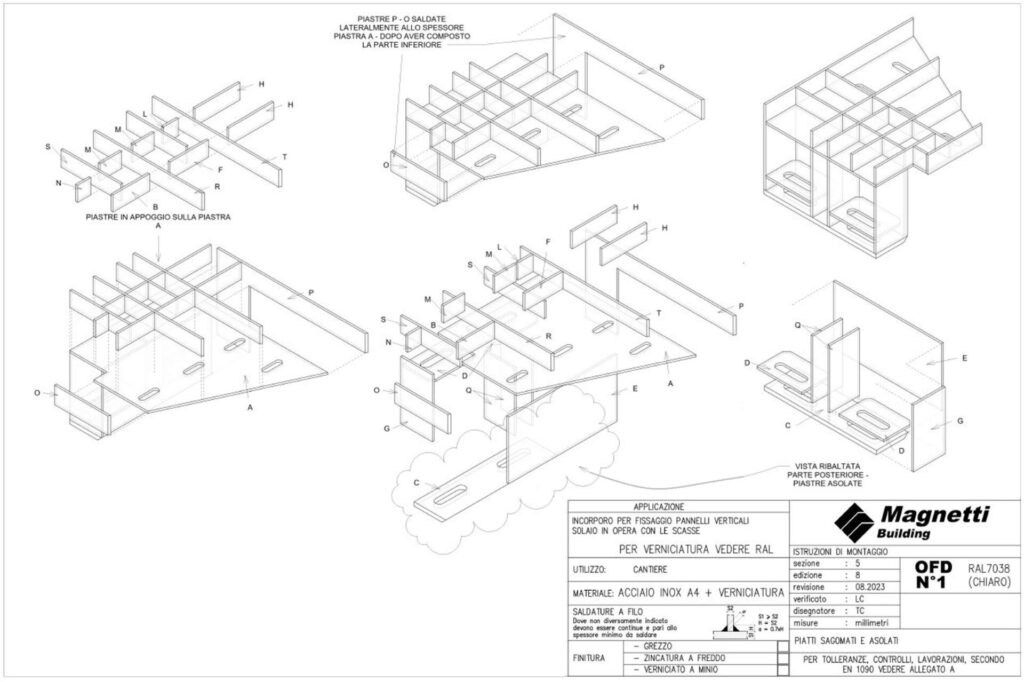
For the next stage, IFC-based collaboration will be rolled out to drive logistics and fabrication. Since the standard IFC format is rather limited when it comes to what information is exported, Magnetti will rely on the Precast Designer for Revit to get customized IFC files, containing all the parameters needed downstream from the modelling phase.
For fabrication, specific geometric and non-geometric information is used, such as material specifications, assembly instructions, and quality control parameters which guide the production of building components. This integration helps ensure accuracy and consistency throughout the manufacturing process, ultimately improving productivity and reducing errors. As a next step, Magnetti and Massimo’s team will evaluate some advanced manufacturing systems with built-in support for IFC, ensuring that design data encoded in IFC format can be seamlessly integrated into the fabrication workflow.
Additionally, the IFC files facilitate the transportation, storage, packaging requirements, and distribution of the precast elements as they contain data on the dimensions, weight, marks, and other parameters that allow the logistics office to efficiently plan and execute delivery schedules.
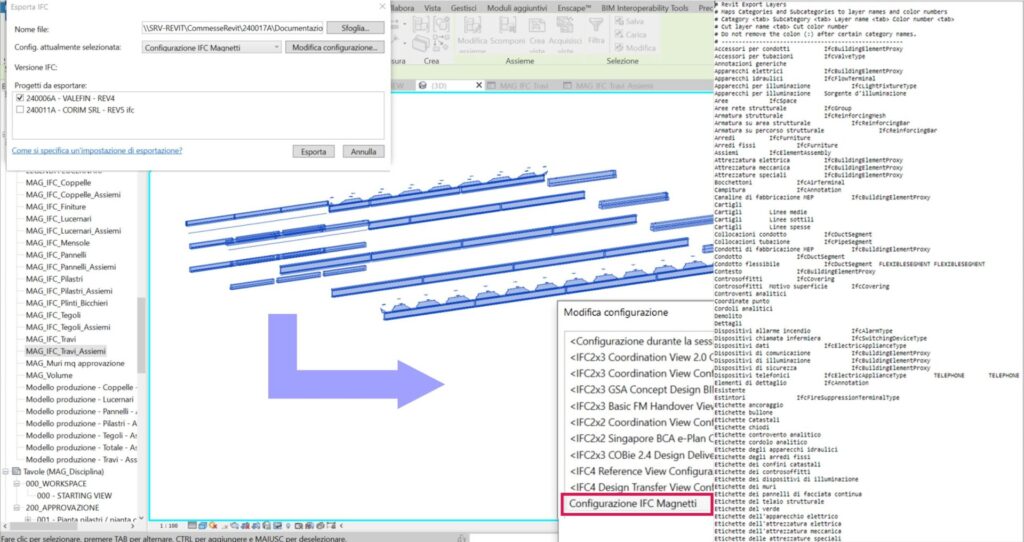
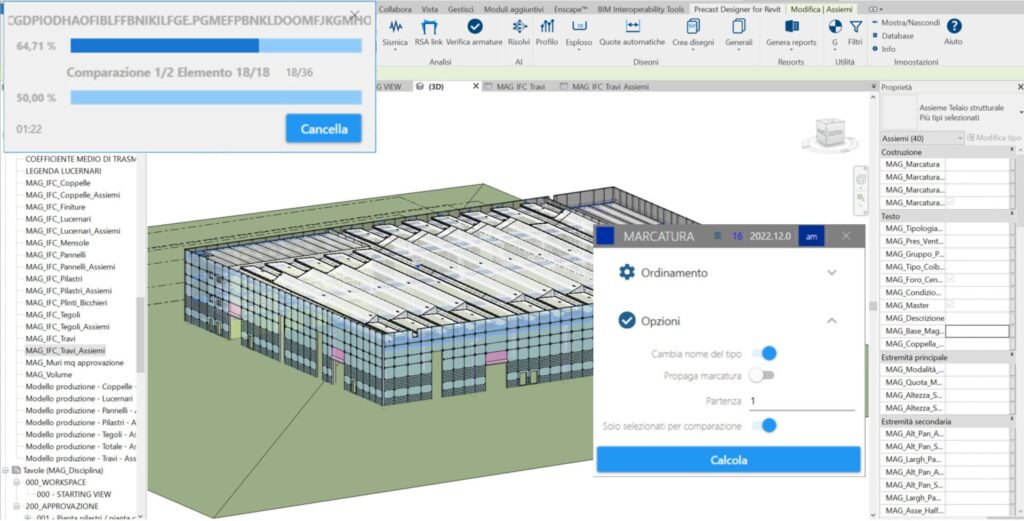
Fabrication is the most expensive process, according to Magnetti. By implementing BIM, they were able to optimize the production schedule, while increasing the output and the quality of the precast elements. According to Magnetti, the number of errors in the fabrication and construction phases decreased by 80%.
Relying on a single source of truth with the Revit model, they will be able to optimize the delivery of the precast elements to the construction site, using tools that can more efficiently bundle items based on a truck’s capacity combined with the weight and the length of the prefabricated components.
On the construction site, they can use cranes more efficiently by optimizing layouts on which elements are lifted by each crane.
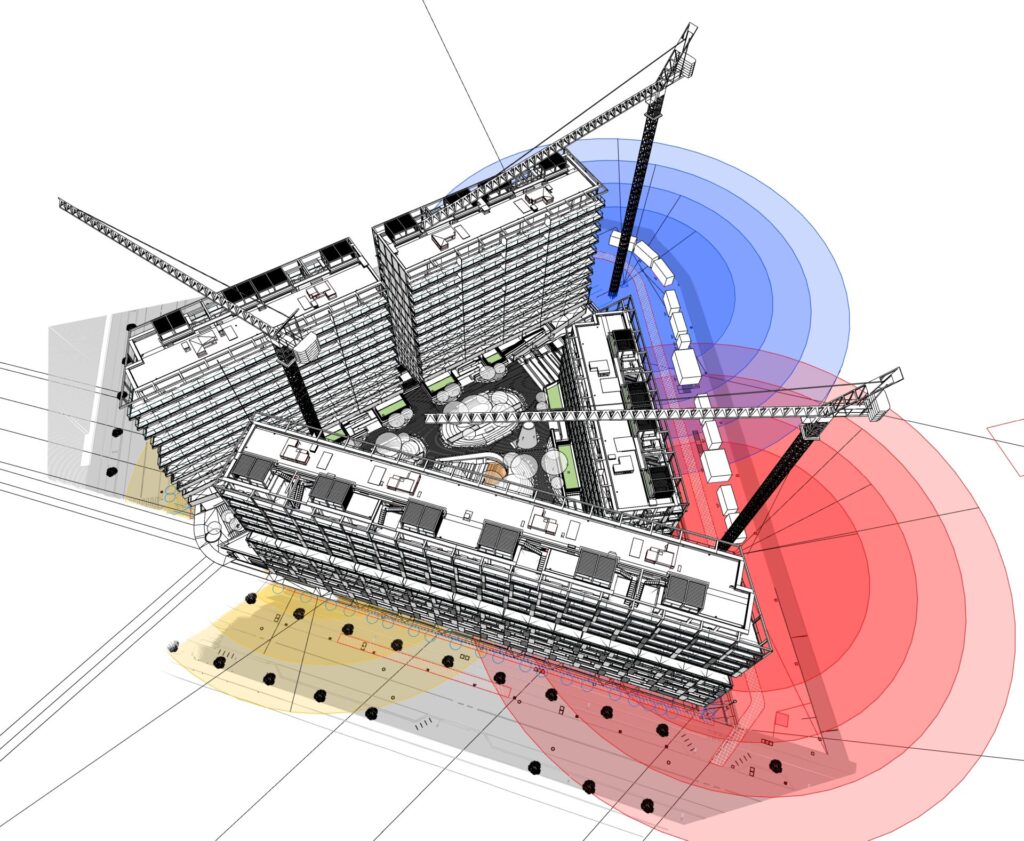
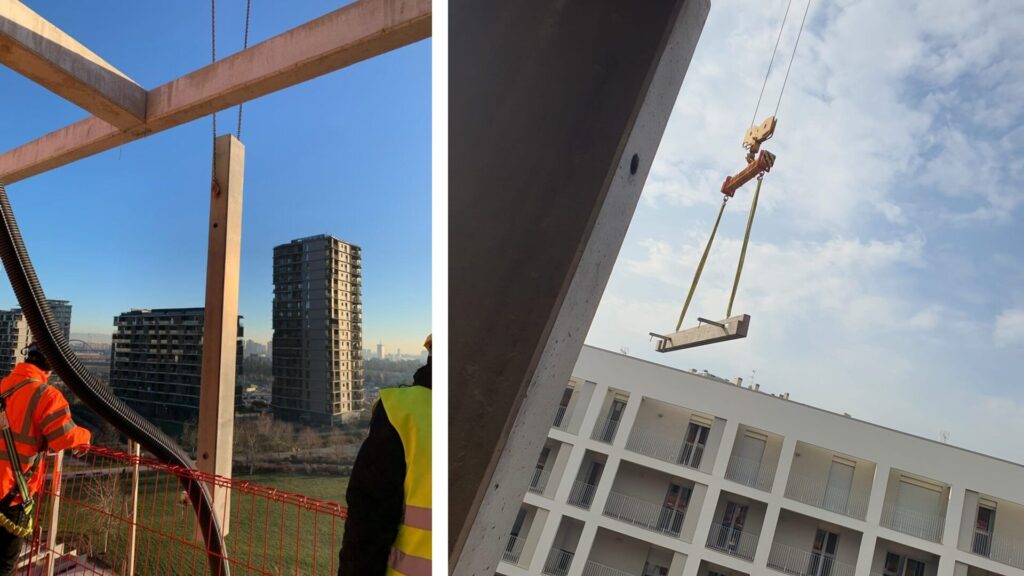
In the end, Magnetti expects they will have optimized their entire design to fabrication and construction workflow. The ecosystem the company is a part of has dramatically changed in the past 50 years, targeting a specific market is no longer the most viable path forward, as customer demand became more and more fragmented. They need to respond to unique requests from all kinds of customers and projects.
So far, they report a 20% reduction in the time for designing and detailing precast projects, and they have experienced a 20% time reduction of the construction process. These are solid numbers, especially considering that Magnetti had already perfected CAD-based automated workflows across the decades.
Whether they need to talk to architects, engineering firms, general contractors, or building owners and no matter if it’s a new large industrial structure, a small precast building, or an owner who needs to enlarge an existing building, the switch to Revit and the Precast Designer for Revit is what makes Magnetti feel comfortable they can make anything.