
Elevate your design and manufacturing processes with Autodesk Fusion
Get a sneak peek at what’s to come and understand the ‘why’ behind our investment areas in the 2025 Autodesk Fusion Roadmap.
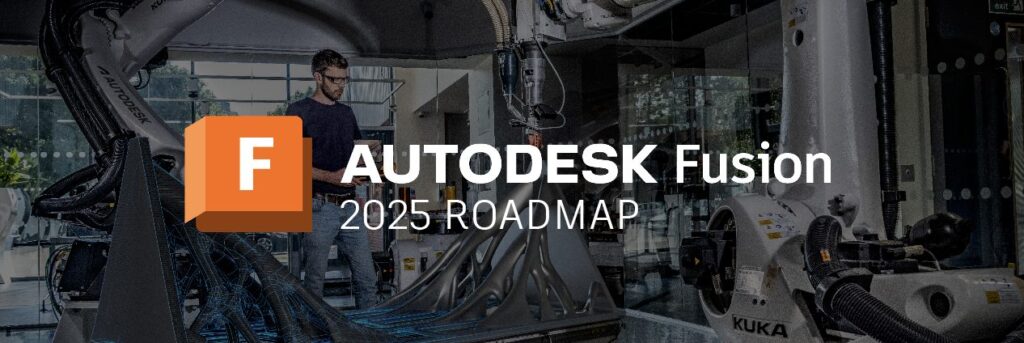
2024 was an exciting year for Fusion, and 2025 will be no different. Last year, we focused on moving toward our vision of flexible, connected data from design to production to help you unlock numerous opportunities like better decisions, better collaboration, and, above all, the opportunity for major productivity gains.
Ultimately, we want Fusion to enable your teams to move beyond repetitive, non-value-added, time-consuming tasks so that you can focus on what really matters to your business: driving innovation.
By connecting data across all our tools and integrating AI-powered tools into daily Fusion workflows, we’ve broken down traditional silos, accelerating productivity in every discipline. In 2025, we’ll continue to expand on ways AI can benefit your process, aim to make your daily tasks even easier, and revisit features we haven’t updated in a while.
Table of Contents
- Disclaimer: Safe Harbor Statement
- Fusion 2025 Focus Areas: Three key pillars
- Cloud data and collaboration
- AI and automation
- Design and manufacturing
- Help us shape the future of Fusion
Disclaimer: Safe Harbor Statement
During the course of this communication, we may make forward-looking statements regarding future events and the future performance of the Company. These forward-looking statements are subject to assumptions, risks, and uncertainties, which are discussed in documents we file from time to time with the SEC and specifically in our Annual Report and 10-K filed for the most recently completed year-end. These documents contain and identify important factors that may cause the actual results to differ from those contained in our forward-looking statements.
Additionally, we may make statements regarding planned or future development efforts for our existing or new products and services. These statements are not intended to be a promise or guarantee of future delivery of products, services, or features but merely reflect our current plans, which may change. Purchasing decisions should not be made based upon reliance on these statements
The Company assumes no obligation to update these forward-looking statements to reflect events that occur or circumstances that exist or change after the date on which they were made.
Fusion 2025 Focus Areas: Three key pillars
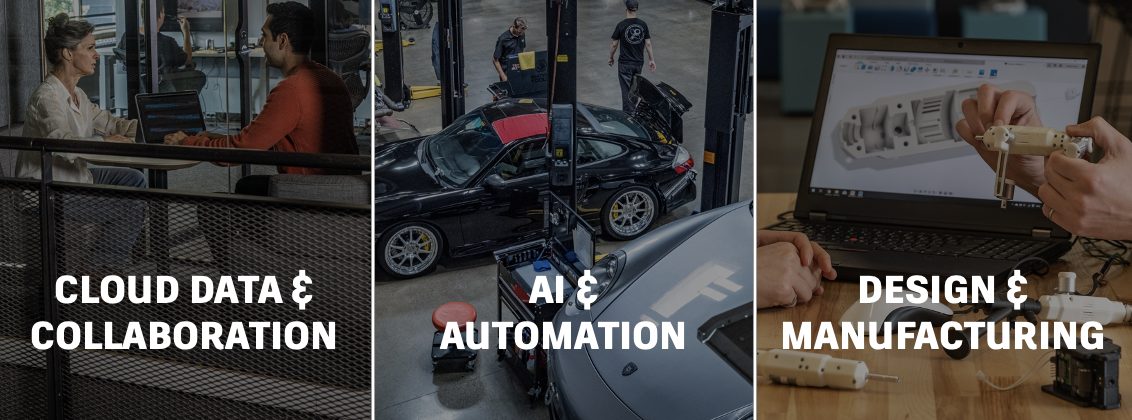
To follow through on our goal to streamline your daily workflows, we plan to focus on three core pillars this year: Cloud Data and Collaboration, Design and Manufacturing, and AI and Automation. We have very exciting things in store, from our investment in assemblies and quality of life to new features like auto constraint, which will leverage AI to offer predictive constraints for your sketches. Let’s dive in!
Cloud data and collaboration
The Fusion data management experience has come a long way. We are the pioneers of cloud-based CAD/CAM, breaking new norms in the industry. Offering easy access to your data from anywhere, anytime, and on any machine.
The past few years have shown the true benefit of cloud-based data. It’s imperative to enable individuals and teams to collaborate in real time, staying connected with their projects even when working remotely. Now, we’re working on connecting your data on a common data platform. We’re doing so by improving our Bill of Materials, expanding on our APIs, and making sure that relevant data is captured and retained through the entire design-to-make process.
Platforms made for collaboration
Team-based collaboration begins by consolidating team data into an environment where all members of the team can work with this data in a centralized hub. For users working in a ‘single user storage’ hub, some of these benefits of a centralized storage location are missing.
To gain access to these great features, we’re working on experiences to help single storage hub users to Fusion hubs. As soon as projects are transferred to a Fusion hub, a number of benefits will be unlocked such as the Home Tab, configurations, cross-project references, fasteners, and folder-level permissions. One of the benefits of a Fusion hub is the additional security capabilities and the administration of users. Back in 2024, we introduced folder-level permissions, and we have delivered additional enhancements with hub-level groups since. By listening to your feedback, we’ve been able to expand the folder permissions model to make it easier to not only create groups but also find and reuse these groups in other folders.
Learn more about Fusion Hubs here.
Unified cloud data
Collaborative property editing
We plan to enhance the list of properties found in Fusion to help users better describe the components in their designs and improve the editing of property values. These enhancements will enable multiple users or automations to edit these property values simultaneously across various Fusion clients. Property changes will be instantly committed to the cloud without the need for a save action, reflecting real-time updates. Additionally, our API support will enable automations to update metadata without the concern of locks or conflicts, simplifying the process. These improvements aim to streamline the experience of adding values to fields, fostering a more efficient and collaborative environment for you to enjoy.
Continued investment in Bill of Materials
Last year we introduced Bill of Materials (BOM) to Fusion. BOM enhances our vision of data transformation and a unified cloud data experience by integrating essential product information, enabling more efficient management and collaboration across the entire design and manufacturing process. Continued investment in BOM is crucial to advancing our platform’s capabilities and providing you with the cutting-edge tools you need to excel.
We’re working on expanding Fusion BOM capabilities to include some great enhancements based on your feedback. The new properties mentioned earlier will be added as additional BOM columns and we’ll enable property value editing within the BOM experiences. We’re also working to add physical property information from the designs to the BOM, helping to provide insights into mass, density, and bounding box information. Lastly, we’re adding a new flat BOM view to help make it easier to get a list of parts that are used within the assembly, making your workflow smoother and more efficient. These upgrades aren’t just about adding new features; they’re about improving how we manage properties within Fusion.
Learn more about Bill of Materials here.
Manage Extension & BOM workflows for internal components
While we recommend designing assemblies by referencing existing designs to optimize reuse, there are times when the ideal workflow calls for the creation of internal components, such as top-down design methods or using configured designs. In these cases, duplicate models are generated that represent the same part number.
To help support these use cases, we’re working on an enhancement to group these designs based on their part number, helping to maintain consistency with Bill of Materials across a Fusion hub where these duplicates live. This enhancement will also be used to streamline the release and change management workflows of these components with the Manage Extension, helping users avoid the creation of duplicate items within the extension.
Enhanced API capabilities
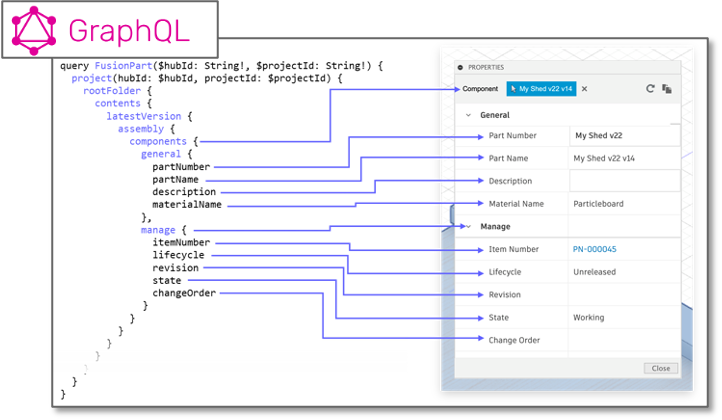
The Fusion API empowers you to develop scripts, add-ins, and applications that enhance and personalize the software functionality. This allows you to automate tasks, introduce new features, integrate with external systems, and much more. We also plan to add exciting new capabilities to the API like writing data to the data model via custom properties. So for this cloud API that is separate from the Fusion client API, we have chosen GraphQL because it offers a single easy-to-use interface by federating multiple services in Autodesk Platform Services.
More importantly, this API is based on query language, which means that developers can query for specific information and get just that back, rather than getting a large blob of data back like traditional rest services. You can query for an individual component’s life cycle state or an entire BOM view, without having to also get all other properties back or having to parse through them in your app.
AI and automation
Advancements in AI and automation are a crucial part of our vision for the future. By moving beyond repetitive, non-value-added, and time-consuming tasks, you can focus on what truly matters to your business: driving innovation.
Sketch AutoConstrain
Sketch AutoConstrain will simplify the process of constraining sketches. By using AI tools and heuristics, the system analyzes your sketch and offers predictive, stable constraints. You can easily edit dimensions and constraints, and the system adapts to your changes, providing new suggested results based on the latest information. Note that you will still be able to constrain sketches yourself. This feature is meant to help new users make more robust sketches and speed up their workflow.
Fasteners Library enhancements
We’re working on a custom lengths feature that will enable you to create custom lengths for fasteners and add them to your library. The system will automatically update fasteners in the proper increments as parts get thicker, longer, etc.
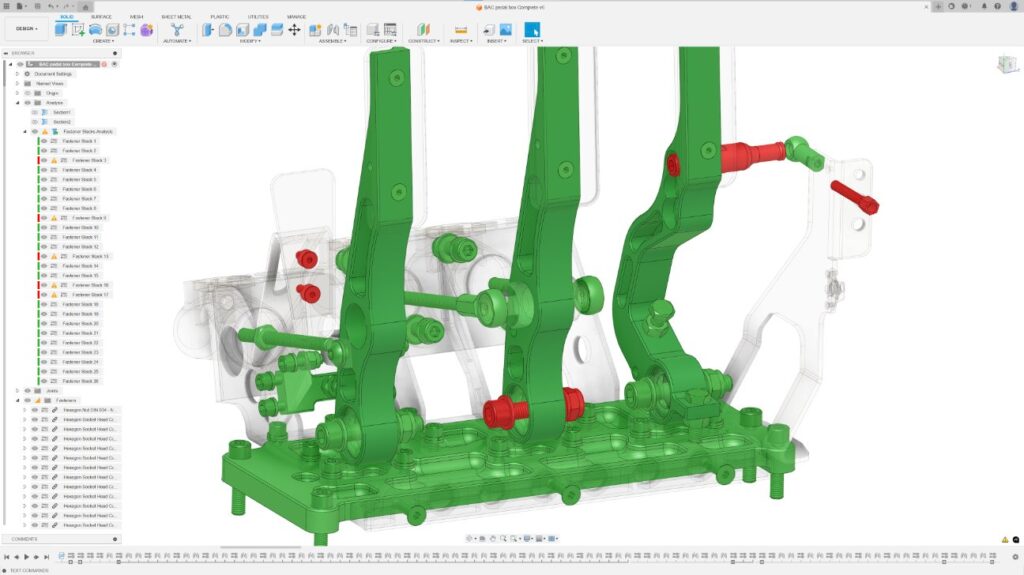
Additionally, the fastener validation tool will automatically analyze an assembly and identify fastener-related issues, such as noticing a threaded hole without a fastener. It will suggest adding a fastener in the appropriate place. While we can’t prevent all mistakes, this tool can help identify mismatched thread types or sizes, warn you, and offer to swap the incorrect fastener with the proper one. It’s a great way to continuously analyze your work.
Learn more about fasteners here.
Automated Drawings
We plan to leverage AI when dealing with fasteners in drawings. AI will examine assemblies to identify fasteners, omitting them from automatic drawings, thus helping to reduce overhead and provide accurate Bills of Materials.
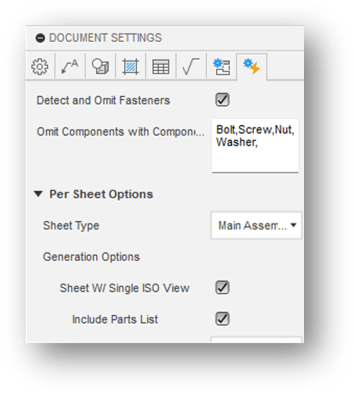
This will make it easier to make the right parts with the right bill of materials. It also helps free engineers up from the current manual search process, which is fraught with errors and logic, so they can focus on more value-added tasks. We’re also aiming to add enhanced configuration management, which would allow the automatic creation of drawings for multiple configurations.
Multi-Axis Clearing
AI is already helping to program parts faster, and we’ll continue to add more capabilities to enhance automation. For example, the Multi-Axis Clearing operation will analyze the curved floors and angled walls of models for five-axis roughing, providing better access to undercut areas, not only reducing repetitive selections but also generating more optimal toolpaths.
Design and manufacturing
Design
Over the last year, millions of designs have been created using Fusion. Key priorities included the release of AI and automation in drawings and features that make it easier to create assemblies. Additionally, smaller enhancements like two-sided offset were big hits with our community, as they provide time savings and make Fusion more fun and easier to use. Let’s take a look at what we have planned in Assemblies, Configurations, Simulation, and Automation.
Assemblies
Fusion users are betting their businesses and livelihoods on Fusion, and we want to ensure it’s up to the task. When it comes to enhancing assemblies over the next year, we’re focused on three areas: performance (is it fast), user experience (is it easy), and capabilities (can you complete your designs).
A new performance feedback tool will allow us to capture key information from your specific workflow data. This will enable us to release targeted enhancements to make real workflows faster. It will be a comprehensive test suite that tracks multiple use cases at once.
We are working on a new assembly experience that gives you access to your tools in a way that allows you to build your products very, very quickly. It will allow you to connect components quickly and easily together. We’re planning to create a unified command that makes it super easy for you to connect opponent components in an assembly. It’s going to encompass kinematic relationships and spatial relationships, how it goes in, and then how it behaves once it’s in, and we’re going to make it easy to use and easy to find.
Configurations
Configurations in Fusion offer the ability to create configurations of any type or size of your product. The beauty of configurations, as they are today, is that we built them off of our data model, so it separates that data from the individual files, making it easy to create different configurations and not have to worry about every file dragging along with it.
We’re working on a rules engine that will give you greater control over that complexity. It will be code-based but low code, meaning you don’t need to learn Python or any other program to take advantage of this feature. This rules engine will help you reduce repetitive and error-prone tasks and will really empower you to build automation.
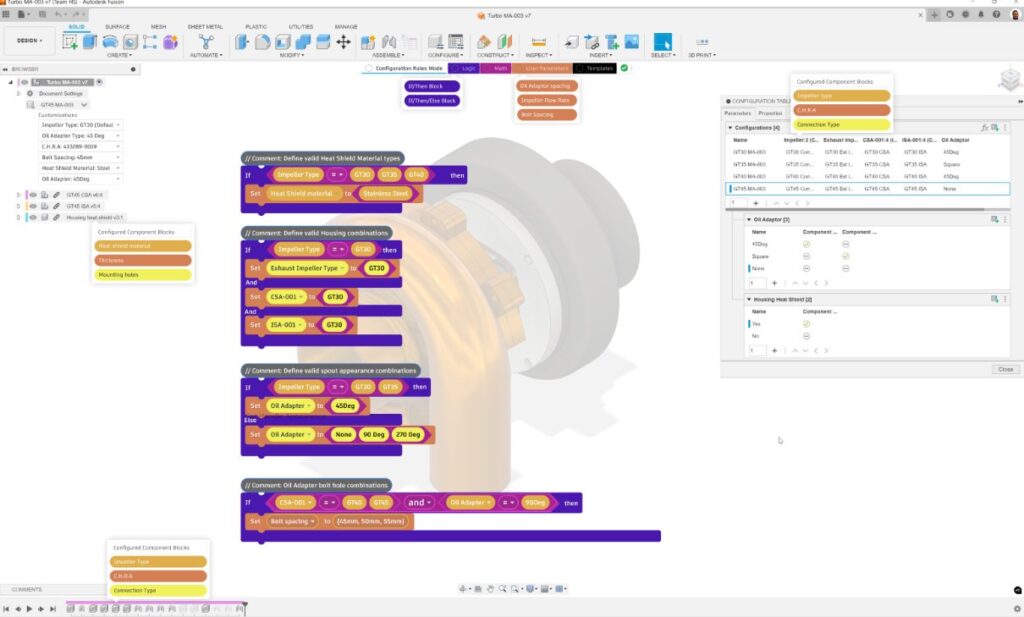
The rules engine offers you the ability to automate decisions that drive choices in an ‘if this, then that’ format. We’re not going to give you templates that just say you have to do it our way. We’re going to give you those tools. Ultimately, this rules engine will help you reduce repetitive and error-prone tasks. It will really empower you to build automation. It also opens up the possibility to create your own product configurator.
Drawings
Drawings automations are only as good as the foundation they’re built on. In that vein, we plan to continue enhancing drawings features throughout the year. One example will be advanced ECAD Integration, including improved view, drill tables, and custom sketch symbols.
We’re also working on enabling you to create and reuse custom sketches in drawings. This means giving you the ability to create your own sketches in drawings and use them as symbols, empowering you to get exactly what you want and reuse it over and over again.
Sheet metal
We’re investing more in sheet metal tools to enable comprehensive creation of sheet metal assemblies, multi-body connections and easier manipulation of complex shapes. For example, if you have two sheets of metal, you need to be able to connect them easily. Currently, it’s challenging to do this in Fusion, requiring the use of loft and other tools. We aim to simplify this process so you can connect two edges directly.
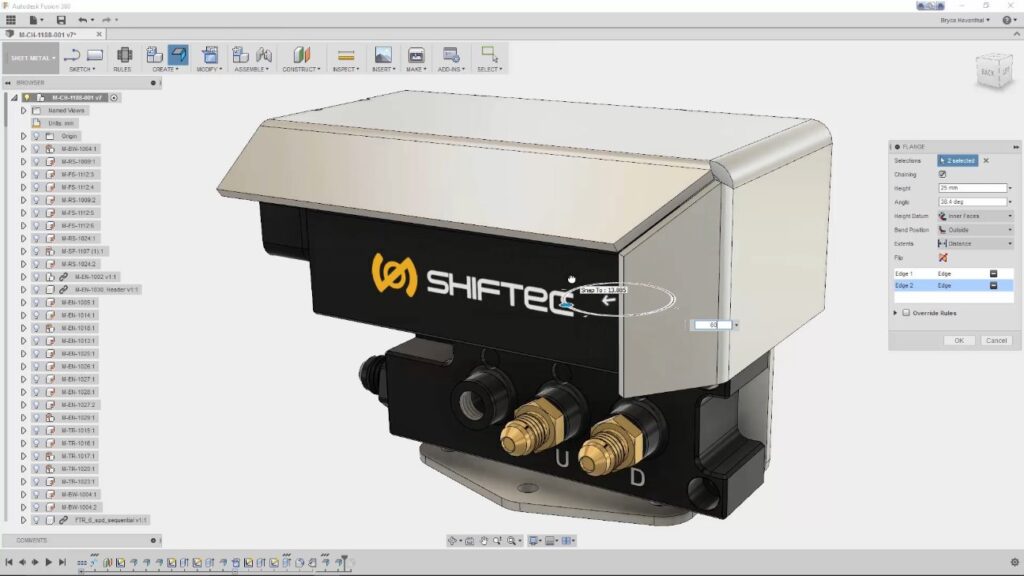
Simulation
We’re aiming to make simulation more accessible by giving you guided information on what you can do with your simulation results. Currently, users have to interpret their results and try to figure out next steps, which you have to be trained to know how to do.
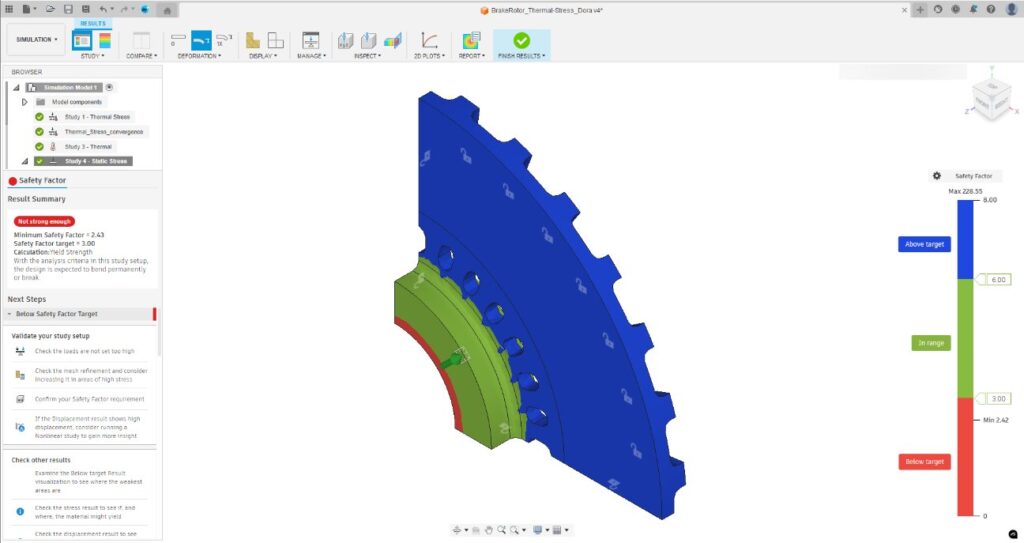
We want simulation to be easier to understand so that more people can use it effectively. We’re working on revamping and modernizing the simulation interface so that you can use it to do things like set goals for your design and measure progress via targeted, easy-to-interpret visualizations and a summary of what happened and recommendations for next steps.
Electronics
The success of any tech-enabled consumer product design depends on getting the electronics design right. Fusion provides a seamless transition from 2D to 3D PCB design, integrating smoothly with electromechanical design workflows and enabling designers and engineers to collaborate more effectively than ever before. In 2025, we’ll continue to dedicate our efforts to promoting stronger collaboration between mechanical and PCB engineers. Our top priorities will be broadening the range of electronics design tools at your fingertips and maintaining high standards of performance and usability.
Manufacturing
Over the past year, we made efforts to ensure smoother transitions from design to manufacturing workflows, such as adding automatic thread recognition to improve turning threading operations. Significant enhancements have also been made in simulation, including machine simulation and collision detection. Additionally, new multi-axis finishing strategies have greatly advanced the milling capabilities, offering better control.
We want to make sure to continue to deliver value in the manufacturing space. To do this, our key focus areas for the upcoming year are to mature and automate workflows where we have strength, close critical gaps where they exist, and drive value across the entire manufacturing platform.
Turn/Mill
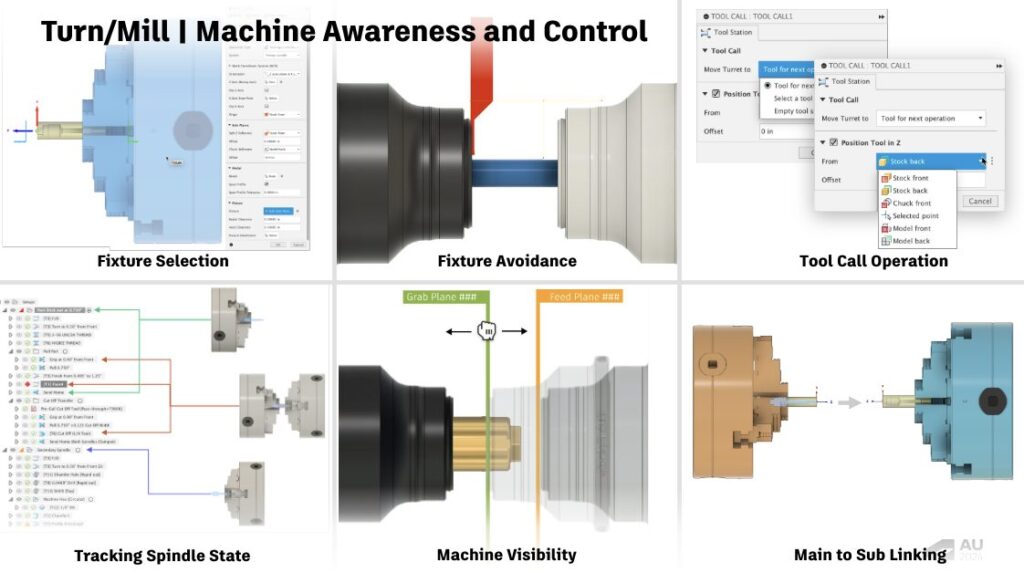
We’re upgrading turning tool holders so you can import a 3D model for higher accuracy and safety over the existing parameterized holders. The upcoming profile trace strategy will allow for more precise control over turning tool paths, offering direct control over the exact path the tool takes so you can access previously inaccessible areas. We’re also adding the ability to limit 5-axis toolpaths to 4 and 4+1 axis to meet the needs of milling on TurnMill machines, enhancing both milling and turning workflows.
Enhancing workflows across domains
Our goal is to ensure that when you use design features, they also work for you in manufacturing. For example, when you X-Ref a part file into another document, you will be able to bring along the CAM data with it. So, if you programmed a part and needed to swap it into a different work holding, all that programming work that you already did will be available from those part files.
Similarly, in capturing design intent, we are planning to add stock material to manufacturing setups and tool presets. When you create a manufacturing setup, an appropriate stock material will automatically be assigned based on the predefined mapping to design materials. When selecting a tool from the library, you will also be able to see if that tool has a relevant preset based on the setup’s stock material. The presets list will be conveniently sorted, placing the most relevant options at the top of the list for easier selection.
Last but certainly not least in this area, we are working to make sure all the goodness delivered in Design brings value to your manufacturing workflows. Over the past year, we have consumed configurations from design in manufacturing to let you generate toolpaths quickly for families of parts. Now, we are planning to save and cache the toolpaths on a per-configuration basis, so that toolpaths remain saved and available when switching between design configurations, removing the need to regenerate each time.
Connected shop floor
Another way we’re continuing our mission to strengthen the connection between CAD and CAM is by making intentional progress to connect to the shop floor and then potentially expand into places like the factory and beyond. This includes connecting Fusion directly to machines on the shop floor to display an overview of machine utilization, as well as the ability to directly send NC code from Fusion to the machines. The direct connection to machines on the network will allow for consistent code transfer, even across different machines and controls.
Milling
We also plan to make huge improvements to the creation of custom hole templates, adding much more control over each segment of the hole profile, including defining key dimensions as ranges or nominal values and the ability to assign color and priority. Working together, these new features will help ensure the proper hole template is deployed when programming.
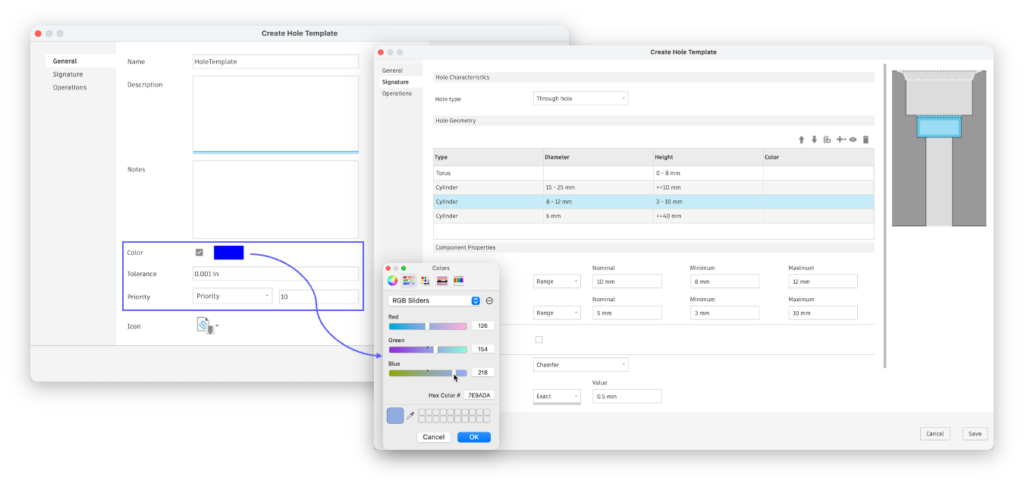
Drilling toolpaths will also be further enhanced to include options to avoid shaft and holder collisions, and they will gain multi-axis capabilities, supporting 4, 4+1, and 5-axis outcomes. These enhancements aim to make drilling toolpaths safer and more efficient.
We also plan to enhance tool path efficiency and safety by incorporating machine model information into the tool path. This will help avoid collisions between the machine spindle and other components like the table or work holding at the point of toolpath generation.
Help us shape the future of Fusion
Do you want to have early access to some of the upcoming features we just discussed? Consider joining our Insider Program. Joining the Insider program gives you the opportunity to provide us with direct feedback to make these features better before they get rolled out more broadly.
DISCLAIMER: Roadmaps are plans, not promises. We’re as excited as you to see new functionality make it into the products, but the development, releases, and timing of any features or functionality remain at our sole discretion. These statements are not intended to be a promise or guarantee of future delivery of products, services, or features but merely reflect our current plans, which may change. Purchasing decisions should not be made based on reliance on these statements.