
Elevate your design and manufacturing processes with Autodesk Fusion
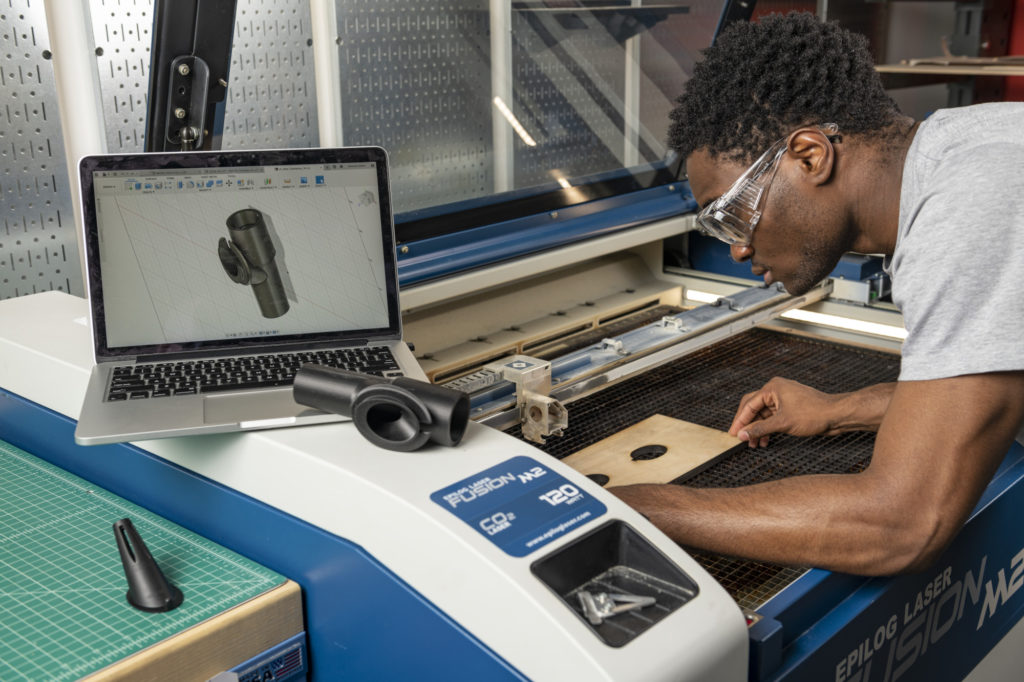
The gap between initial concept/design intent and final design response can be closed by industrial design prototyping. A prototype embodies design intent and allows for hands-on research by industrial designers and engineers, which provides room for problem-solving alterations and validation. Additionally, stakeholders and end-users can examine the functional prototype for UX design flaws and manufacturability before jumping to the final manufacturing process.
What is Industrial Design Prototyping?
Traditionally, industrial design prototyping involved model making by hand. Handmaking models can still be an important step in the creative process. However, new technologies have shifted the process. Today’s product development process typically involves the pre-production process of exporting designed products from digital software, like Fusion 360, into physical and functional samples used for market research and presentation. Before innovations in 3D product design, prototyping could be expensive and time-consuming. With integrated 3D CAD/CAM software, designers can implement sweeping revisions using parametric design features and more.
There are several methods of industrial design prototyping: iterative, parallel, competitive, and rapid. These different methods of prototyping produce varying models of proof-of-concept during the product development process.
Iterative Prototyping
Iterative prototyping involves creating a prototype from the product design, testing it for usability and functionality, and then revising what didn’t work. After testing has concluded, the research team will design a new iteration and manufacture it for testing. The old iteration is then thrown out or set aside. Iterative prototyping is practical and allows for quick identification of challenging design problems but can be expensive and wasteful depending on the number of iterations required.
There is a version of iterative prototyping — evolutionary prototyping — that removes the need for more than one iteration. The idea behind evolutionary prototyping is to gradually refine the first iteration as improvements are identified based on incoming feedback. Eventually, the first and only prototype becomes the final product after extensive machining and revising.
Parallel Prototyping
On the other hand, parallel prototyping is a concept-based method where several design concepts are compared concurrently. Multiple designs are drafted and then compared to find the best versions before a physical prototype is manufactured. This method promotes creativity and conceptual ideation. Parallel prototyping can be expensive due to a large number of contributing factors.
Subsequently, there is a parallel prototyping version — competitive prototyping — where multiple design teams develop concepts independently. Competitive prototyping is useful for larger projects that have the potential for higher risk factors.
Rapid Prototyping
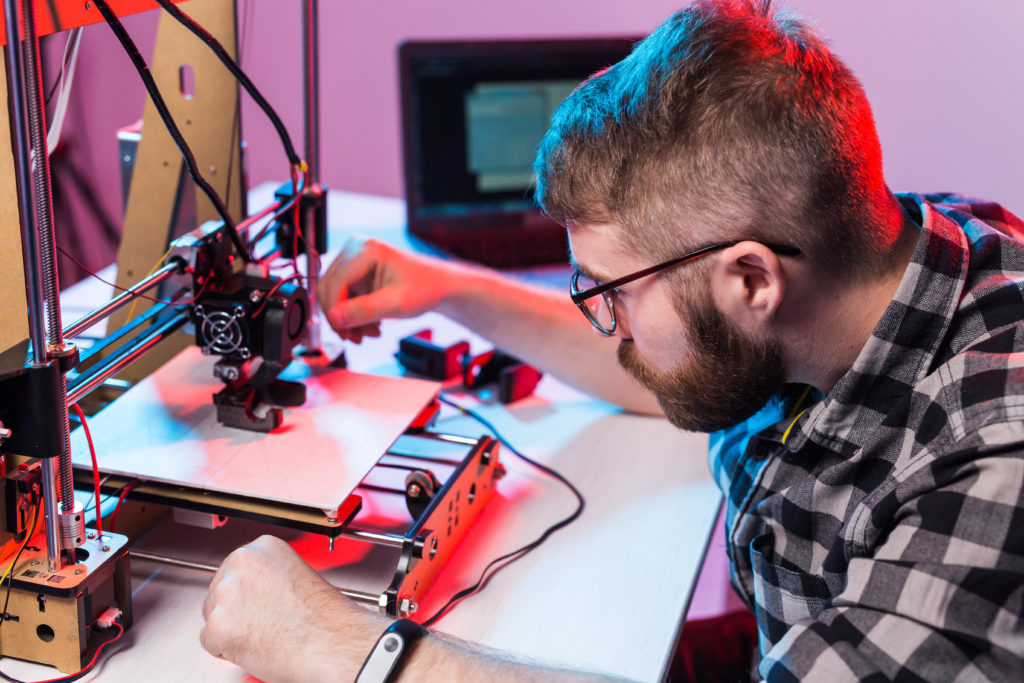
Rapid Prototyping
Rapid prototyping is a more recent product design testing method that incorporates some aspects of the iterative process. This method is fast and accessible for product designers who can access CAD software and 3D printing technology in-house. Rapid prototyping utilizes innovative technologies—CAD software and 3D printing—to create seamless data transfer from computer to printer. This method is an affordable way to run usability and functionality tests on newly printed mockups.
Previous methods might take a few days to manufacture and compare iterations of the product depending on fabrication technology and communication requirements. Rapid prototyping is a process that could be minimized to a daily cycle where the new product iteration is designed/revised during the day and then printed overnight.
Which type of prototyping is best for your design?
The idea that one prototyping process is better than the last is partially subjective, depending on company preference, product specifications, and manufacturing constraints. However, based on speed, cost, and quick access to 3D printers, rapid prototyping can be quite advantageous.
Looking to make your design process a breeze? Try Fusion 360 today.
