New to machining? Take a deep dive into CNC turning vs. CNC milling to determine which option best fits your process. To properly navigate the world of manufacturing, it’s important to know the strengths and weaknesses of each method.
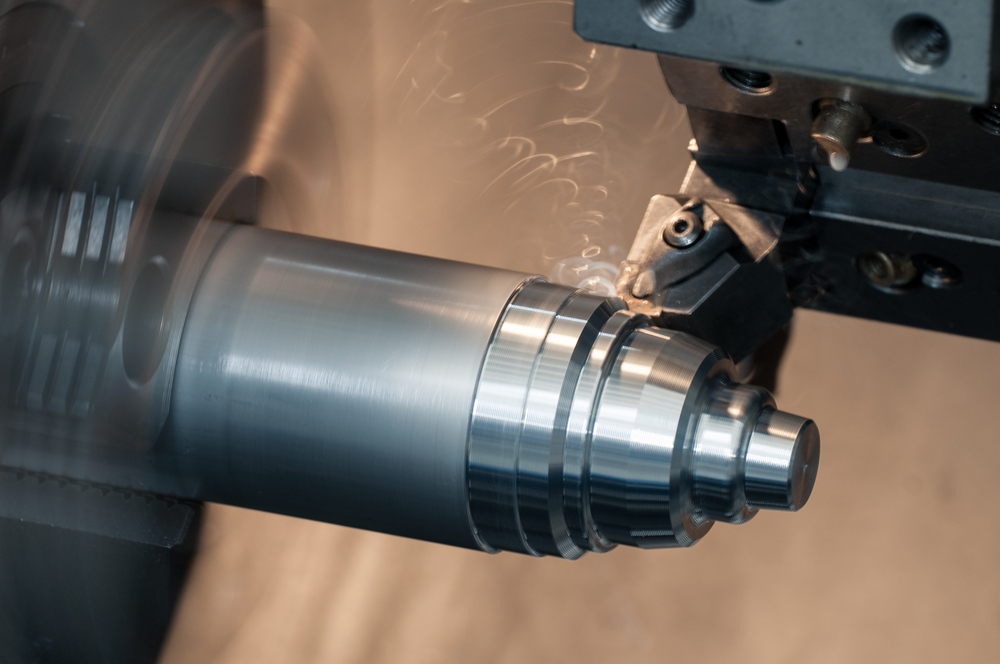
You have a part to make and CAD drawings in hand. Now comes the machining. Should you mill the part or turn it? Ultimately that depends on the hardware available. If your shop only has mills, you have your answer. But for the sake of exploring the two processes, let’s look at them side by side.
This article explores the differences between CNC turning vs. CNC milling and how Autodesk Fusion can be a game-changer for machinists in both realms. We’ll largely discuss 2D turning and 2.5D milling, ignoring machines and processes where turning and milling can seem to blend into one complex process instead of two distinct ones.
Keep in mind that this is not the end all be all of CNC turning vs. CNC milling knowledge. For those of you looking for additional information, there will be links to other pages, articles, and videos that will go into more detail. Let’s jump in.
What is CNC machining?
Before diving into the differences, it’s important to define CNC machining.
Computer Numerical Control (CNC) is a machining technology that automates machine tools, such as lathes, mills, and grinders. By feeding a set of coded instructions into the machine, it precisely manipulates raw material to create parts that meet exact specifications.
What is CNC turning?
Milling and turning are two common CNC machining methods. They are both subtractive, meaning they remove excess stock material to achieve the final result—your part. Apart from that one fundamental similarity, they are two distinctly different processes.

CNC turning occurs on a machine called a lathe where the material turns but the tool remains stationary. Typically, the part is held in a rotating spindle using a chuck that can clamp with jaws or hydraulics to hold the part in place. While the spindle spins, a turret equipped with a cutting tool moves toward the raw material and removes it as the material turns, creating the desired shape.
The tools in the turret are very rigid, and the turret rotates to change which tool engages with the material. Since the part is spinning while the tools remove material, the resultant shape is some form of revolved profile: a sphere, a cone, a cylinder—you get the idea. The spindle and turret are controlled by a built-in computer, giving the lathe the ability to make complex profiles with high accuracy.

CNC turning centers are like a more complex lathe and can include one or more turrets, secondary spindles, and various tooling options, as well as different power and speed capabilities. A CNC Turning Center is more expensive but will produce more in less time.
What is milling?
With CNC milling, there are many different machine configurations, but typically you think of the part remaining stationary while a spinning cutting tool moves to carve out the desired shape. Typically, the part is held on the machine bed with clamps or a vice. Cutting tools like endmills or drills rotating at high speeds shave off material to reveal the designed part. Imagine a sculptor carving a statue out of a block of marble, really, really quickly, and you get the idea of milling.
This article goes deeper into the different milling tool types.
Mills come in many configurations that can add complexity and increase functionality. Even simple configurations add value because of their flexibility. Milling machines shave away wood, metal, composites, and other materials with ease. Most mills offer modular or flexible workholding, and it’s very common to machine custom vise jaws on the same machine that will eventually cut the part.
Depending on the machine you have, you can make parts for industries like automotive, aerospace, industrial machinery, robotics, wood furniture – the list goes on and on. Because of the ability to create complex shapes, hold complex shapes, and cut a variety of materials, milling offers tons of flexibility.
When do I use CNC turning vs. CNC milling?
Generally, if it’s round, you’ll turn it. Examples include washers, bolts, ball bearings, casters, and even chess pieces.
Use milling for any part that’s not round—or even if it is! CNC milling is a very common machining method because of its flexibility in shape, material, workholding, and so on. You can pretty much make any shape you need on a mill.
Machinists use milling in many different ways, including:
- As a secondary process for an already-manufactured part, like a cast, to create accurate slots, threads, and holes.
- To fabricate a part from start to finish.
The result: highly accurate, high-tolerance parts of nearly any shape. Use milling for prototypes and production runs of all sizes.
Should mill then turn, or turn then mill?

From a geometry perspective, you will likely turn then mill. A milling machine can hold onto a round part easier than a rotating chuck or lathe can grasp a complex part. However, there are “soft jaws” for turning chucks that can hold complex shapes, so it’s not impossible to mill first and turn second. Typically these kinds of process choices are driven by the part requirements, like which features need the most accuracy.
Moving a part from one machine to another means losing some accuracy from feature to feature, so it’s important to consider locating and final part requirements.
What are the advantages and disadvantages of CNC turning vs. CNC milling?
If all you have is a 2-axis lathe, you’re essentially limited to round parts. When turning tools or inserts wear, the process to replace them in the turret is highly manual, so production comes to a halt until maintenance can take place. If metal chips break into the tool instead of against themselves, they can damage the tool or the machine. There’s an art to monitoring chips when your machines run 24/7.
Most milling machines allow you to change tools easily and monitor wear. When you change a tool, you can use a tool probe to run wear compensation data and breakage checks with just a few lines of code. If a tool needs replaced, it’s relatively simple to automate the machine to swap in a new tool without skipping a beat.
For all their flexibility, there are still some things milling machines don’t do well. Any square internal corner between two vertical walls requires post-processing to achieve. Tall walls require an equally long tool, which can deflect significantly and result in a poor surface finish that requires additional finishing either by hand or in a different setup.

For both milling and turning, it’s beneficial to design fillets to keep your machine motion nice and smooth, and to make sure you’re not shoving a tool in a corner. Jittery tool motion and sudden increases in engagement can cause wear and breakage, interrupting the entire process. Fillets help ensure the machine moves smoothly between different features, creating a better surface and more consistent loads on the tool.
What is a toolpath anyway? Why are they important?
The path through space that a tool takes to produce the exact geometry of your part is called the toolpath. Your toolpath can be 2D, 3D, 4, or 5-axis. Again, what you use will likely depend on what you have available to work with.
- For a good starting point, check out this article that takes a look at 10 basic milling strategies.
- For more information on 3D toolpaths, our help guide digs into the details about what each 3D toolpath does and what types of geometry each is best suited for.
How Autodesk Fusion helps
Autodesk Fusion offers a targeted set of features that elevate the capabilities of machinists in both CNC turning and CNC milling.
One important feature is the 3+1 and 3+2 (positional) machining, which minimizes the number of setups required. This not only streamlines the manufacturing process but also contributes to faster cycle times. The additional axes enable the use of shorter, more rigid cutting tools, that directly affect the overall part accuracy and improve surface finish quality.

For those seeking to push the boundaries in CNC machining, Autodesk offers the Fusion Machining Extension. This extension unlocks advanced multi-axis capabilities, providing machinists with the tools to tackle more complex geometries and intricate designs. The extension is a valuable asset for projects that demand a higher degree of precision and flexibility.
All things considered, Autodesk Fusion acts as a comprehensive platform that addresses the needs of today’s machinists. From reducing setup times to enhancing tool rigidity and offering advanced multi-axis functionalities, Fusion optimizes every aspect of
Great! Now what?

There is so much to learn and apply in every machining project. There are considerations like your machine’s capabilities, what tools you have, and the features you’re trying to make. Comparing milling to turning felt a bit like comparing apples to oranges. They may both be subtractive processes, but the details are very different! Hopefully, this was a fun exercise in looking at those differences and considering how each would affect the process of machining a final part.
Try Autodesk Fusion for free today to get started with CNC turining and/or CNC milling.