By now, I’m guessing you’ve heard about the Fusion 360 manufacturing extension? If so, you’re almost certainly wondering what it includes and how it impacts you. In this blog, we’re going to dig into one of the most exciting additions relating to toolpath optimization, specifically the inclusion of a new Steep and Shallow machining strategy. To see Steep and Shallow in action, watch the video below where Kieran manufactures a mold tool to demonstrate its benefits big and small.
Automated to save programming time and effort
Steep and Shallow finishing automates the machining of feature rich, free form shapes. It does this by creating a single toolpath that cuts the entire part with an intelligent combination of Contour toolpaths for the steeply angled faces, and Parallel/Scallop machining for the shallower regions.

1) Shows the 3D Offset toolpath in the shallow areas. 2) Shows the Constant Z toolpath in the steep areas.
Steep and Shallow machining is one of the most commonly used toolpath strategies in Autodesk PowerMill. It was for this reason that the team decided to enhance the code and put the feature into Fusion 360.
Let’s consider the machining of the part shown in the following image.
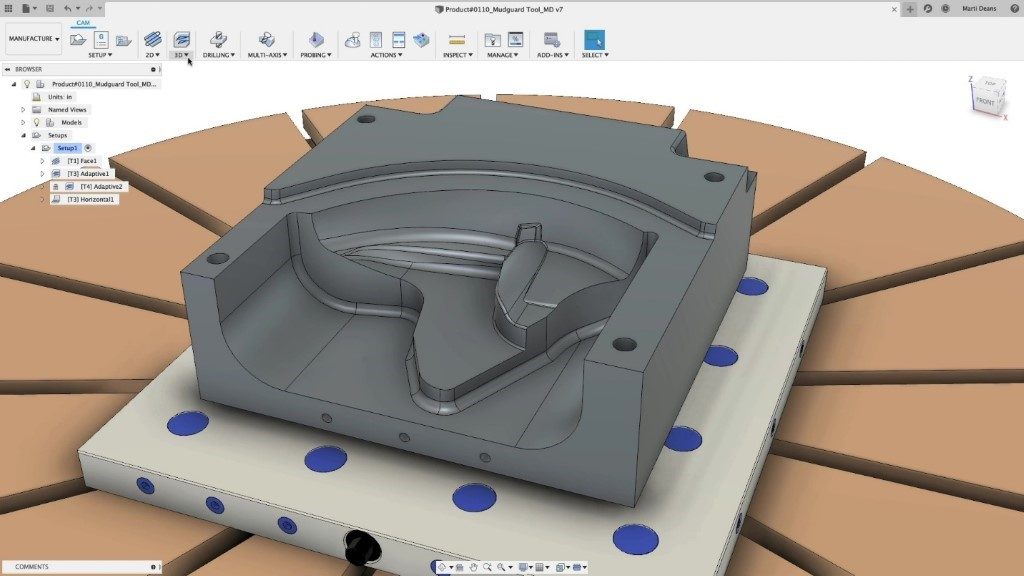
Example model
This part contains a mixture of near vertical side walls, horizontal pocket bases, and doubly curved faces/fillets. Because Fusion 360 considers the model holistically, it can create toolpaths where the machining of the steep and shallow regions is interleaved together. This reduces the amount of air cutting while also helping to avoid heavy cuts that could damage the cutting tool or workpiece.
The Steep and Shallow toolpath for this part can be seen in the image below.

Steep and Shallow toolpath
Advanced options give you even more control, quality, and ultimately…happiness
While this strategy aims to simplify the programming of parts, numerous advanced options have been provided to offer greater control to deliver better surface finish and improved utilization of machine and cutting tools.
Independent control over steep and shallow machining
Fusion 360 provides separate controls over the stepdown used when machining the steep regions, as well as the stepover used for the shallow areas. In addition, it is possible to control the cutting condition for both – i.e. whether to use climb or conventional milling or both.
Threshold angle
This user-defined parameter controls which parts of the model are considered as being steep and which regions are considered as being shallow. Fusion 360 uses this threshold to change the shape of the toolpath. Increasing this number results in more of the component being machined with a Scallop/Parallel toolpath type. Reducing the threshold angle results in more of the part being cut with a Contour toolpath type. Typically, the threshold angle will be set around 30 – 45 degrees.
Overlap distance
To ensure all material is removed from the component, the steep and shallow toolpath segments can be automatically extended such that they overlap by a user-defined amount (see Image below). This constant distance overlap improves the quality of the blend between neighboring cuts, gives a better surface finish meaning there’s less of a need for manual polishing.

The overlap distance setting ensures steep and shallow toolpaths remove all material
Machining priority
Fusion 360 provides two options when it comes to machining priority – these being “Top First” and “Steep First”. These change the order that the toolpath is run. When “Top First” is selected, the upper, shallow sections are machined before the steeper side walls. This can help avoid heavy cuts when the cutting tool engages into stock on the tops of features. When “Steep First” is selected, the steep parts of the model are machined before the shallow regions.
Parallel – automatic direction
This option applies if Parallel is selected for the machining of shallow regions. When activated, Fusion 360 automatically adjusts the angle of the toolpath segments to minimize the number of retractions away from the part which can reduce machining cycle time (see below).

Automatic direction aligns parallel toolpath segments with the geometry being machined
Parallel – wall clearance
If shallow regions are machined with Parallel toolpath style, this user-defined offset can be used to keep the cutting tool away from the steep regions of the component at the end of each parallel pass. This helps avoid the cutting tool leaving marks on the part that would need to be polished (Image below).

The wall clearance option helps prevent witness marks from being left on the part
Scallop – smooth offsets
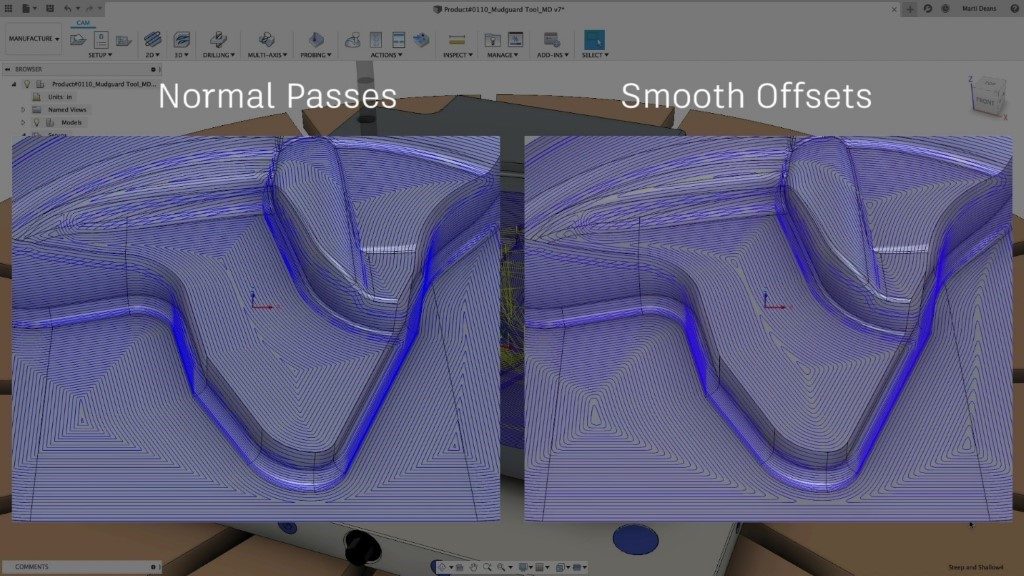
Smooth corners in Scallop toolpaths enable faster CNC machining and better surface finish
This option applies if shallow regions are machined using the Scallop toolpath type. If activated, Fusion 360 applies smooth arcs to any sharp corners in the toolpath. These smoothed toolpaths have a number of positive benefits. Firstly, they tend to shorten machining cycle times as the CNC machine can maintain a constant feed rate for the entire program and not keep accelerating/decelerating in the corners. Secondly, these toolpaths apply a more consistent load on the cutting tool which helps avoid dwell marks being left on the part.
Scallop – Remove cusps at junctions
A common problem with Scallop toolpaths is the fact that additional material can be left unmachined in the corners of the toolpath. As the offsets spread over the component, each corner will result in small upstands (or cusps) that will need to be removed by manual polishing. Fusion 360 addresses this using the “Remove cusps at junctions” option. When activated, additional toolpath segments are automatically added to the toolpath to remove the upstands.
The option to “remove cusps at junctions” greatly improves surface finish with Scallop toolpaths.
Scallop – Spiral scallop
The Scallop toolpath type can be further controlled using the “Continuous” option. When switched off, Fusion 360 creates toolpaths where each segment is offset from its neighbor by a constant amount (see below). These segments are then joined together with a series of smooth, tangential link moves that the CNC machine can navigate smoothly and quickly.
If the “Continuous” option is switched on, Fusion 360 creates a spiral toolpath (see image below) where the distance between neighboring offsets can vary. The real benefit here is that this toolpath has significantly fewer link moves meaning the surface finish will be much better. A spiral toolpath will typically have a marginally shorter cycle time than a non-spiral version.

Scallop toolpaths can be created with multiple, constant offsets (top) or a single spiral (bottom)
In addition to these strategy specific advanced options, Steep and Shallow also benefits from the following, standard Fusion 360 capabilities:
Filleting
As part of the toolpath calculation, Fusion analyses the CAD model and identifies internal corners that are smaller than a given radius. A user-defined value is then used to add a fillet to all internal corners prior to the toolpath being calculated. The use of the “Fillet” option helps avoid tool breakages caused by shock loading the cutting tool as it engages into large amounts of stock.
Feedrate optimization
Fusion 360 analyses the toolpath and identifies any sharp changes in direction that could be problematic when run on the CNC machine tool. Once identified, the cutting feedrate is automatically reduced as the cutting tool approaches the corner. It is then increased gradually until the original programmed feedrate is achieved.
Fusion 360 manufacturing extension available now
Whether you’re new to Fusion 360 or a seasoned pro, we’re confident the addition of Steep and Shallow machining, in the new manufacturing extension, will improve your CAM programming efficiency, helping you to start cutting chips sooner and produce better quality parts faster.