This post is also available in: Deutsch (German)
With the help of our internal sustainability team, we took a look at different 3D printing infill types and gave each a sustainability ranking based on power consumption and material usage.

At surface level, things can seem gloomy for sustainability in the additive manufacturing industry. Between power consumption, the use of plastics and the plethora of other challenges, it’s easy to write 3D printing off as an unsustainable practice. Well, we’re here to show you that it doesn’t have to be that way. This series of blog posts is dedicated to building sustainable 3D printing practices. First up is this article, which covers how to maximize the benefit of additive infill strategies.
Before we get started, let’s rip an important Band-Aid off: making a new product is not unethical, nor is 3D printing. Asking yourself whether what you’re making is necessary is always important. However, as long as what you produce is intended to be used, then it is not unethical to simply manufacture.
Designers and engineers think about a broad range of aspects when creating a part; ergonomics, manufacturability, production costs, safety, machine accessibility, etc. However, we often don’t consider sustainability unless we’re talking about materials. Sustainability goes beyond material, though. It’s also about how you design your product for disassembly, how much waste and energy you use in operation, and more. In fact, 3D printing can be more sustainable than subtractive methods, since 3D printing uses only the material needed and often generates less waste.
We want to acknowledge that product specifications often don’t give much room for sustainability considerations. If you’re ever in a position where you have room to explore sustainability, though, we’re hoping this series will point you in the right direction.

What is Infill?
Infill is a necessary portion of 3D printing that enables you to print faster with semi-hollow structures, using the lattice to maintain a level of strength in your part.
Infill Sustainability Rankings
For this article, we worked with our internal sustainability team to evaluate our infill patterns in Fusion FFF. We looked at each one and calculated the material used and the time taken for a small 25x25x25mm cube of 20% infill at 0.2mm layer height. We kept it strictly infill and printed without top or bottom shells and without perimeters.
The intent of this study was to look at how much material is used compared to the time it takes to print so that we can consider sustainability from both power consumption and material usage perspectives. The chart below shows what infill strategy was used and how much filament (measured in length of filament as opposed to material volume) was consumed. We’ve given each infill a sustainability rating to do the hard work for you:

Material usage and time of print varies widely across different infills. If either can be reduced for a print, then the user would reduce the amount of material used as well as the amount of energy drawn by the printer for the print.
We also plotted this data as a graph to better visualize the results:

You can clearly see how Gyroid infill is the most efficient for both Material usage and print time. By using gyroid infill for your prints you will make your parts more sustainable as well as print faster! An additional benefit to the gyroid infill is how it behaves depending on the material you print with. For example, if you want a springy sponge feel to your part, using Gyroid with TPU will achieve that.

We placed Gyroid at the top of the infill options list in the additive manufacturing workspace to help you easily use this best practice by default.
Want to learn more about additive capabilities in Autodesk Fusion 360? Check out these tutorials and these courses from Autodesk University.

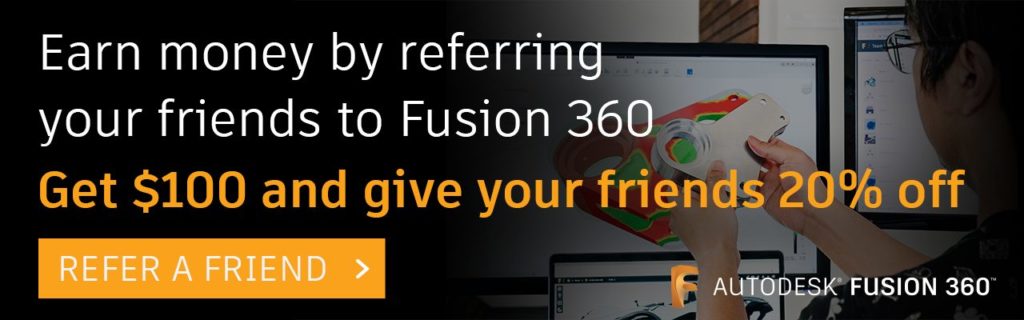
This article is co-authored by Thomas Stock, Research Engineer at Autodesk and Zoé Bezpalko, D&M Sustainability Strategy Manager at Autodesk.