This post is also available in: Italiano (Italian)
Italy-based motorcycle company Vyrus transitioned CAD/CAM in-house to create its latest custom bike, Alyen, using Fusion 360.

As a brand, Vyrus encapsulates several distinct aspects of the Italian motor valley in north-central Italy. Unbridled passion for engines, motorcycles, and cars, dedication to research and innovation, and awareness that motorcycles and cars are much more than just a means of transportation. Because between chassis and pistons runs a special emotional bond between human and car which enthusiasts in this region can fully experience. Vyrus is a motorcycle company located in this region that builds custom motorcycles for a select few. The company recently completed its latest motorcycle project, Alyen, using Fusion 360 for 3D modeling and CAM in-house.
Until recently, out of habit and due to issues related to the lack of a good design tool that could complete the design and production cycle from start to finish, Vyrus has turned to external design studios for CAD design and CAM processing of drawings for managing the machine toolpath.
“In some ways, this method helped us stay streamlined, but it also ended up creating several problems,” explains Ascanio Rodorigo, Technical Manager at Vyrus. “Firstly, we were never sure of the delivery time of the work required, so there was no immediacy in being able to check a result against the software output and make changes quickly. Also, since we were customers like everyone else, we had to stand in line and wait our turn, stretching the time frame beyond any reasonable limit. In short, using external vendors often becomes more complicated and slower than necessary.”

Another significant aspect is Vyrus motorcycles, and its new bike Alyen boasts a structure composed of pieces created primarily from solid material. This significantly impacts suppliers’ invoices who buy raw material and deliver finished products after hours of machine tooling.
To tackle the Alyen project, Vyrus needed to give centrality back to the technical office and the prototyping department. Additionally, the team needed to improve the quality of work and save money, especially since these are limited-edition and sometimes one-of-a-kind products.
As is always the case with such decisions, the person responsible investigates and looks for possible solutions before deliberating. Marco Garavelli began to research to find out what was possible and what the important products on the market were.
“The range of CAD/CAM offerings was really very broad and in some ways pretty confusing,” says Garavelli. “While researching, I came across Autodesk Fusion 360, and it immediately seemed to be an interesting product. The first thing that amazed me about Fusion 360 was how easy it was to pick up. While with all other software, I had problems. With Fusion 360, even without specific experience in the field, I found that I could become able to work independently rather quickly. As a design system, Fusion 360 is the most intuitive and quickest to learn and use that I have ever encountered. For me, this was almost completely unheard of!”

Aside from the fact that Fusion 360 is easy to use, Garavelli also highlighted its flexibility and comprehensiveness. Several times during our meeting, he pointed out that, unlike other systems that perform the same functions, Fusion 360 makes a series of environments available to its users. It’s easy to get one’s bearings and navigate without fear of making mistakes.
“Fusion 360’s value lies in the excellent quality that this software manages to guarantee the user throughout the creative and design process. I am not ruling out the possibility,” Garavelli continues, “that if we analyzed every single function, we could find a product on the market that performs better. Still, I am certain that there is not a package so complete and so high level, which can guarantee excellent results operating within a single environment and above all with agility and impressive quality.”
However, convenience was not the only factor Vyrus considered — quality and cost savings were also crucial. For Vyrus, Alyen was the first practical test of Fusion 360. The bike has recently been unveiled and will soon be delivered to the first lucky customers.
“Alyen is a lucid madness,” explains Rodorigo. “It is a motorcycle designed according to completely new and unusual rules. It is a unique product intended for lovers of unique and special items. We designed this bike to be completely outside of the box. It’s so unique that over two-thirds of the components are machined from solid using highly technical and lightweight materials.” In short, Alyen was an ambitious project that was not easy to achieve. It was a long-term dream of Rodorigo and Garavelli that required a new approach.

“Fusion 360 has been an essential step in realizing the dream that we have been working on for years,” explains Rodorigo. “If we had used more traditional systems and methods, I can assure you that Alyen would never have seen the light of day. For us, Fusion 360 proved to be the turning point. I sometimes think that not even those who work with Fusion 360 at Autodesk are aware of the advantages of having a single tool that assists you in the simulation, design, and creation of individual elements through CAM. The work is so fast that when the part is still fresh from the milling machine before it has even cooled, we can modify the dimensions directly in CAM to realize another part on the fly that we believe will be better suited to the project.”

A part destined for a motorcycle as unique as Alyen must respond to technical characteristics and precise aesthetic rules. For those who, like Vyrus, have worked mainly with subcontractors for many years, this is a leap forward of unimaginable proportions.

“Quantifying the advantage in terms of time is embarrassing,” Rodorigo explains. “Today, thanks to Fusion 360, the time required to conceive, design, and build any item is perhaps a tenth of what it was before. And time is money. However, the final tally must also consider the cost of each piece. Here there is an advantage of more than 50% compared to before. That’s not all: We no longer need to store spare parts due to purchasing the minimum number of items from suppliers to justify the order. Thus, we immobilize our capital. This is also something we must thank Fusion 360 for. All of this without diminishing the overall quality of the product. Another important aspect is that Fusion 360 is inexpensive due to a marketing system that offers a subscription at a much lower cost than imaginable.”
The company is fully committed to this path: within a reasonable timeframe, Vyrus recovered all previous designs and projects and migrated them into Fusion 360.
“Fusion 360 has transformed our way of working,” concludes Garavelli. “The process of previous models saw a prototype built substantially by hand from which the final components were then reconstructed through a reverse engineering process. Today, everything is focused on design, and this, despite Vyrus being a small company, has given us the mentality and operational capabilities typical of large industrial players. Fusion 360 gives us a significant advantage in terms of competitiveness and quality.”

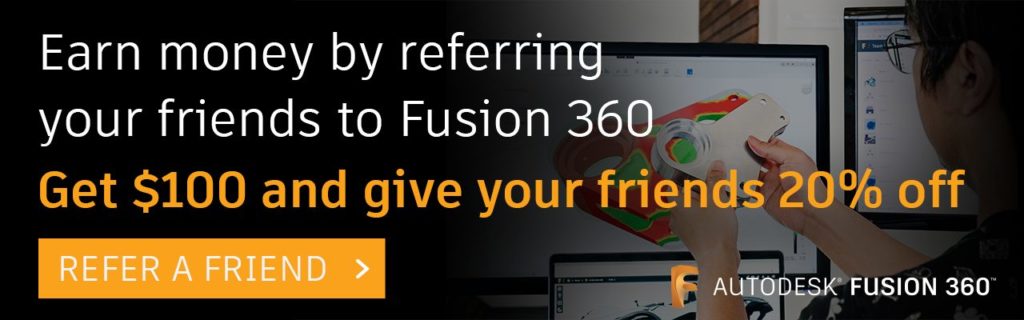