How do companies come out on top in the fast-paced aftermarket automotive industry? Cloud-based product development tools like Autodesk Fusion.

The aftermarket automotive industry encompasses car parts and accessories designed and manufactured by third parties for use after the original manufacturer transaction is complete. This booming industry was estimated to be worth approximately $383 billion in 2020, with an excellent outlook for growth.
Aftermarket parts run a wide spectrum — from more mundane items like tires and windshield wipers to thrilling performance enhancements like composite aerodynamics, machined billet components for racecars, custom camshafts, and tuned exhaust systems for enthusiasts all around.
Many auto machining companies specialize in a particular area of automotive performance or one specific automobile brand. For example, BBi Autosport primarily focuses on Porsche parts.
Though aftermarket auto machining companies tend to be on the smaller side, the industry is not a niche one. The parts designed, manufactured, and implemented in this space end up in Tier 1 factories globally on a regular basis. In many ways, automotive CNC machine companies are trendsetters that impact wider automotive results and public perception.
Aftermarket automotive part companies rely on industrial designers and mechanical engineers using various CAD/CAM tools to develop high-performance parts quickly. Autodesk Fusion 360 is one of the more common tools used by companies in the design and automotive cnc machine space for a few key reasons.
Addressing unique CAD/CAM challenges
Aftermarket automotive teams are often smaller and more agile than large automotive companies. Think about it: teams must react quickly to changing vehicle models and customer needs for them. For smaller design and engineering teams whose projects vary in complexity, CAD tool selection often boils down to three primary concerns: affordability, capability, and data management.
Affordability
Fusion costs a mere $680 per year at the time of this writing. This is a fraction of the cost of most feature-packed CAD systems, enabling many smaller companies to become adopters with minimal downside risk.
Capability
Fusion offers a wide suite of tools and features that enable aftermarket companies to succeed with both tried and true workflows and emerging ones. Scan-to-CAD workflows, for instance, are now a popular way to bring parts to market more quickly. Fusion makes it easy to work directly from 3D scan data in its 3D modeling space, enabling teams to iterate with speed and confidence in part manufacturability before hitting the shop floor.

In Fusion, teams can 3D model parts using direct, surface, parametric, mesh, or freeform techniques. They can also create detailed visualizations of complex products and hierarchical assemblies, including exploded views and animations. Fusion also includes dedicated sheet metal tools for managing bends, flanges, and reliefs in various materials, including paper and cardboard for packaging.
Data management
Fusion is entirely cloud-based, enabling seamless integration across teams. This provides a strong foundation for data management and version control that might otherwise be a stumbling block for small, agile teams. In addition to seamless data management within its own environment, Fusion is also compatible with various third-party file formats. Teams can share and export designs as needed for almost any manufacturing or review process.
Extensibility
Fusion is more than just a CAD solution. It includes everything you need to design, validate and manufacture a part. Integrated PCB design, mechanical simulation, integrated CAM capabilities, and a selection of advanced extensions make Fusion one of the most well-equipped software packages for complex automotive cnc machine projects.
Autodesk Fusion success stories
GoWesty
GoWesty is a Los Osos, California-based company that makes and sells parts for 1968-2003 Volkswagen Buses, Vanagons, and Eurovans. The small GoWesty design and engineering teams develop hundreds of new products annually and use Fusion for most of their new development projects.

One example is their sliding door latch kit (shown above). When the original OEM latches began to fail, GoWesty engineered this kit to replace the mechanisms that weren’t working. They preserved the more complex and expensive parts by modeling and iterating on the entire assembly. The team used the canvas features in Fusion to match the catch profiles. They then implemented simple changes to the original design that addressed weak points.
“The way Fusion manages individual projects works well for us because we’re typically working on one part at a time instead of massive system assemblies,” said Brian Hardoin, the managing mechanical engineer at GoWesty. “It’s really handy to be able to work on dozens and dozens of projects independently on the cloud and not have to worry as much about file organization.”
BBi Autosport
Huntington Beach-based automotive company, BBi Autosport, focuses on designing aftermarket parts for Porsches and building custom cars for races like Pike’s Peak International Hill Climb. For the 100th anniversary of the iconic hill climb, BBi Autosport designed and built a car entirely from scratch in Fusion.
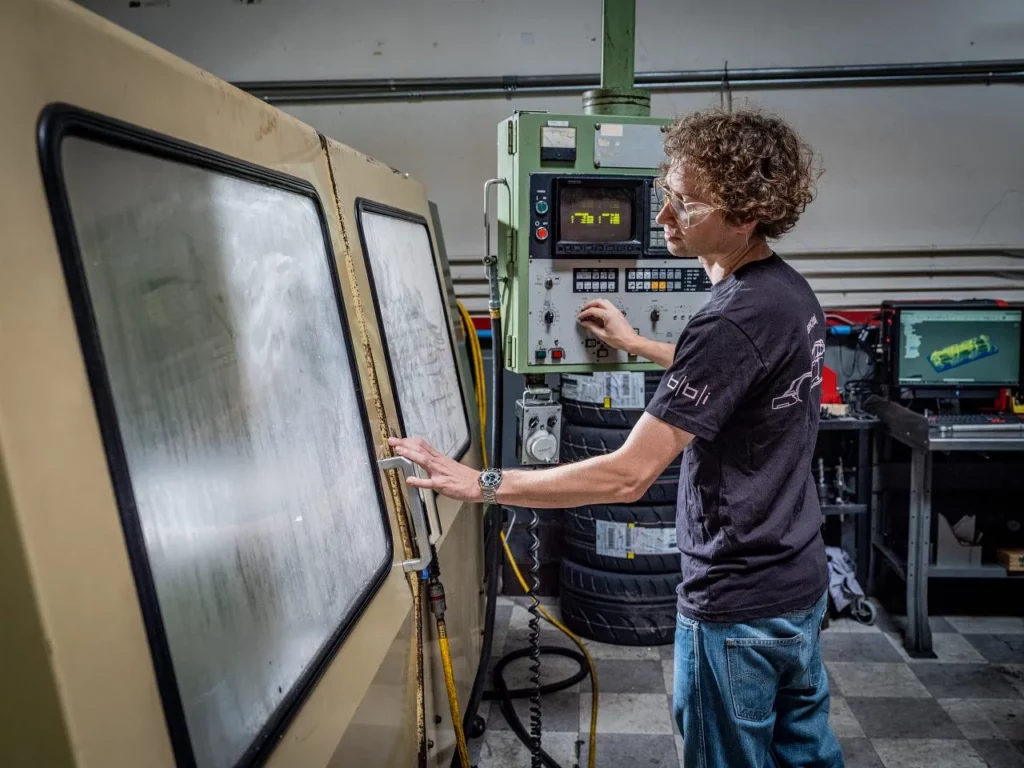
“There’s a trickle-down effect from our motorsport division to our consumer product division,” notes BBi Autosport founder Betim Berisha. “We found with almost the click of a button, Fusion is capable of exporting our 3D models to our CNC machine to manufacture right then and there, ending up with a finished part that is ready to hit the racetrack or ship out the door to our client.”
Eversfab
In a similar vein, Eversfab is a small custom automotive company located in Louisiana, focused on creating high-quality parts for race cars. One recent project involved designing a custom roll cage for a Corvette and leaned on several of the more powerful features in Fusion.

The first step involved using 3D scanners to capture the base geometry of the car. The mesh tools in Fusion were used to incorporate the scan data into the design environment. From there, they designed the roll cage to interface exactly with the existing mesh geometry, as shown in Figure 5.
“I chose Fusion for its intuitive interface and because it was Mac-compatible. There was a learning curve, sure. But Fusion has become my go-to app for in-depth design as well as quick sketches,” said Founder Jason Evers.
Fusion 360 for the aftermarket automotive industry
Companies like GoWesty, BBi Autosport, and Eversfab are just a few examples of automotive aftermarket manufacturers using Fusion to tackle their CAD/CAM needs. Fusion provides the perfect mix of affordability, capability, and organization, making it well-suited for aftermarket automotive companies of all sizes.
What are you waiting for? Make better aftermarket parts using Automotive cnc machine solution, Autodesk Fusion: