Design for manufacturing (DFM) is one of the most crucial aspects of part design. By checking a part for manufacturability before sending it into production, designers can avoid mishaps such as production delays because of reworks, increased production costs, and poor product quality.

Designing a part that meets your requirements is a significant achievement, but, unfortunately, it may only be half of the battle. If your design is not suitable for manufacturing, it could have detrimental impacts on time-to-market, production costs, and product success.
This is where the concept of design for manufacturing (DFM) comes into play. DFM is a methodology that emphasizes designing products with manufacturing in mind, ensuring that the part is easy to produce and meets the required quality standards.
In this post, we’ll explore why it is essential to check your part for manufacturability before sending it into production and how DFM principles can help you optimize your part design for efficient and cost-effective manufacturing.
What is design for manufacturing (DFM)?
Design for manufacturing is the process of designing a product that can be efficiently and economically manufactured. In general, the DFM process involves considering various manufacturing aspects, such as materials, production processes, tooling, and assembly. The goal with DFM is to assess these considerations during the product’s design phase in order to minimize manufacturing costs and production time, as well as to improve the product’s quality.
DFM focuses on several key principles, including simplifying the design, minimizing the number of components, reducing the number of manufacturing operations, and optimizing the design for the chosen production method. Implementing these principles can lead to several benefits, such as reduced development time, improved quality, and lower production costs.
Why is checking for manufacturability important?
Checking your part for manufacturability is essential to ensure that the part can be manufactured efficiently and cost-effectively. When a part is not optimized for manufacturing, it can result in significant delays, added costs, and quality issues.
Here are some reasons why checking your part for manufacturability is critical:
1. Avoiding production delays and rework
Designing a part that is not optimized for manufacturing can lead to production delays and rework. For example, if the design is too complex, the production process may take longer, or the tooling may be more expensive to develop. If the part requires multiple manufacturing operations, it may result in additional production time, leading to delays.
2. Reducing production costs
A part that is not designed for manufacturability may require additional tooling, more complex manufacturing processes, or a higher number of components, all of which can increase production costs. Designing the part for manufacturability can help to optimize the design for the chosen manufacturing process, reducing costs and improving efficiency.
3. Improving product quality
Designing a part for manufacturability can help to improve product quality. For example, designing the part with tolerances that are easier to achieve can reduce the likelihood of errors or defects. This can reduce the likelihood of assembly errors, leading to a more reliable product.
Xometry + Autodesk Fusion: The next generation of DFM
The Xometry add-in for Autodesk Fusion offers a range of benefits to designers, including real-time pricing and lead times based on material and process selection. The tool provides visual design for manufacturing feedback, highlighting any potentially troublesome areas in a 3D model, such as thin walls or non-manufacturable features. This allows designers to resolve issues before they become a bigger problem and helps to optimize cost and lead times.
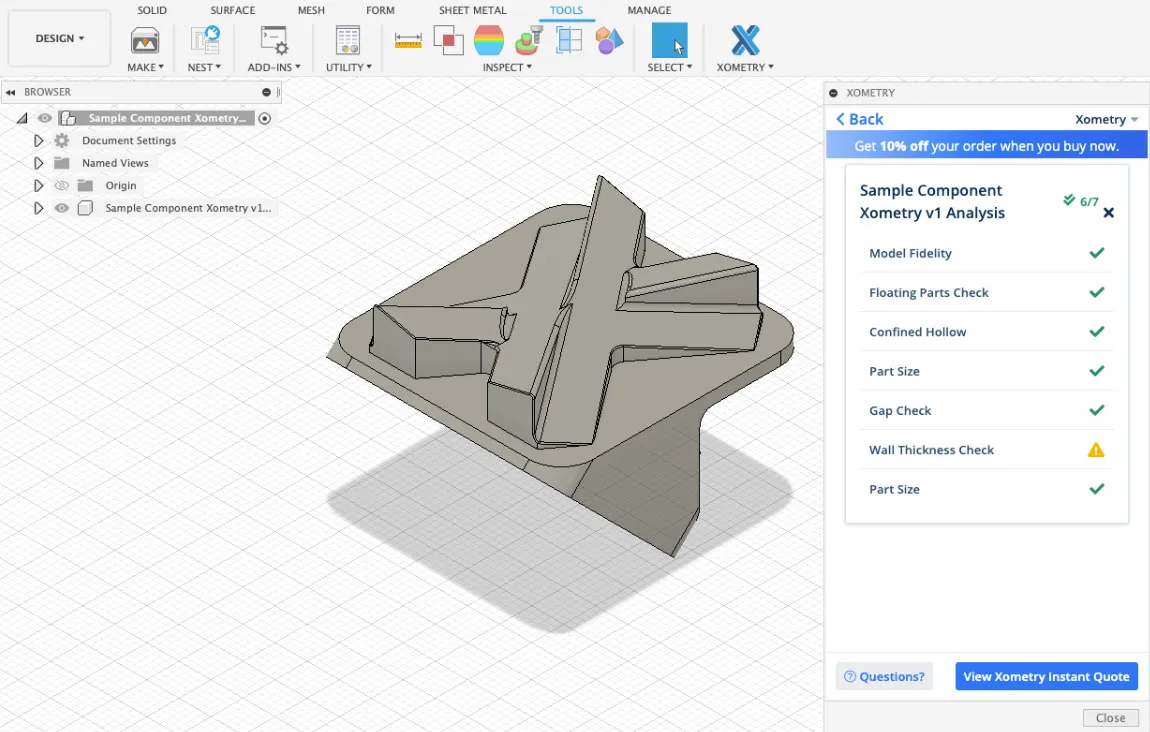
In addition to checking for DFM issues, the tool also offers the ability to easily check the feasibility of a design in different manufacturing processes and materials, review DFM recommendations based on the selected manufacturing processes and materials, and share visual feedback with colleagues. Custom manufacturing feedback and instant quoting allow engineers and designers to see the impact of their design choices on budget and product development timelines.
Xometry’s visual DFM feedback is especially useful because it allows designers to identify difficult-to-manufacture features that can result in higher costs and specialized processes. By spotting these issues upfront, designers can resolve them before they pose a bigger problem, leading to lower costs and improved efficiency.
Whether your project is in early prototyping or ready for mass production, the principles of DFM—as realized through Fusion and the Xometry add-in—can make a drastic impact on your project, today. Designing for manufacturability has never been more important, and it’s also never been easier.