
Elevate your design and manufacturing processes with Autodesk Fusion
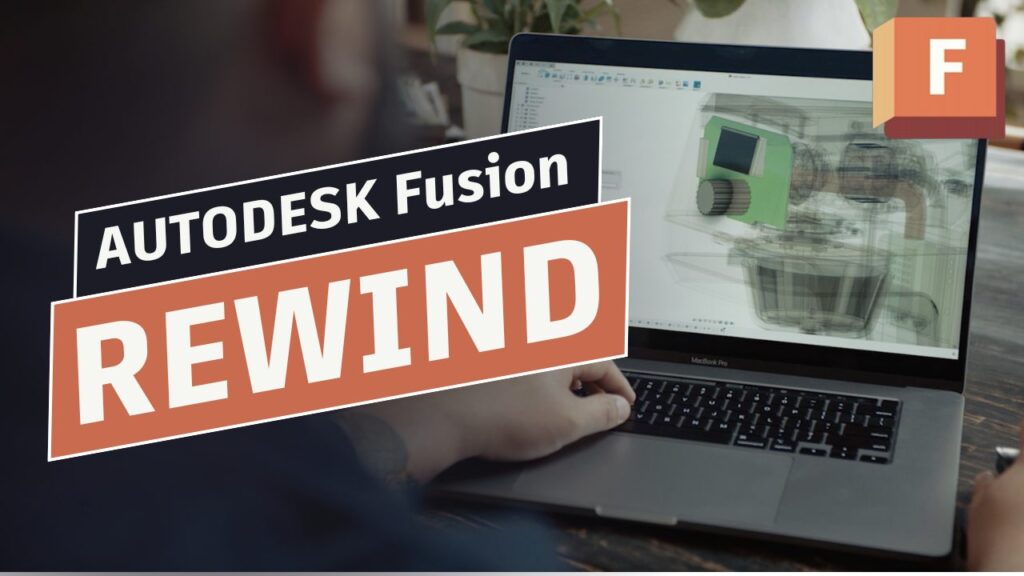
2024 is flying by—can you believe we’re already at the halfway point? It’s the perfect time for us to pause, reflect, and evaluate Fusion’s progress since we shared our 2024 roadmap back in January. This mid-year What’s New rewind will highlight key features we’ve delivered already this year.
Table of Contents
- Performance review
- Data management and API
- Design and engineering
- Manufacturing
- Electronics
- Digital transformation at your fingertips
- Community connection
- Cheers to the rest of 2024
Performance review
First, let’s check on our performance since the start of the year. We are tirelessly working behind the scenes to invest in performance enhancements and improvements for you to enjoy. This year, we’ve emphasized assembly performance to ensure you are equipped with streamlined, efficient tools that can manage complex assemblies easily.
This investment enables you to handle larger projects and provides a smoother design process. Just a few examples include that Compute Joint After Edit is up to 45% faster, select Joint, Edit Joint, and Animate Joint are up to 5x faster for large assemblies, and Insert Into Current Design is up to 45% faster in large assemblies. Opening Designs from the data panel and Fusion startup time improvements are also worth noting.
Beyond the assembly environment, we are continuing to invest in fortifying Fusion’s robustness and resilience through rigorous testing and debugging.
Data management and API
Data management is essential for managing and optimizing how we oversee our facilities, products, and projects. In tandem, API Access opens our platform to innovators from various fields, enabling them to create specialized solutions that extend our existing toolset. We’ve made significant investments in Fusion’s data management tools and API this year. Let’s dive in!
Integrated bill of materials
A bill of materials (BOM) is the listing of items that comprise a product and includes details like part numbers, quantities, part descriptions, lifecycle state, etc. Fusion’s new integrated BOM capability provides additional tools to collaborate and share product information between engineering and consumers of engineering data upstream and downstream. Learn more here.
Manufacturing Data Model API support for custom properties is now in public beta
The launch of Manufacturing Data Model API V2 introduced new capabilities to the GraphQL API and established a foundation for the future of the Manufacturing Industry Cloud.
As part of this Beta version of the API, we also introduced several new capabilities, including the ability to create Custom Properties via GraphQL API that will be visible to Fusion users. This is an exciting project that will be evolving over the coming year, but we invite you to get started with this capability now to help shape the future here.
New and enhanced projects
We are happy to share that we have released a new project type with more granular controls, new enhanced roles, and groups. This new project type provides the following:
Granular access control
Now, you can assign roles to both members and groups at different levels: project, folder, and even subfolder. For instance, you can designate someone as a viewer at the project level to safeguard crucial data, while giving them the editor role within a specific subfolder, allowing them to make design edits.
Enhanced roles

We’ve improved and added new roles so team members have just the right level of access.
- Viewer role (Improved): We have improved our viewer role to permit members to see projects in Fusion, while still protecting the contents from being downloaded.
- Reader role (New): A brand new role allowing administrators to protect important data from being updated. This new role permits users to open, access and reference data. Securely referencing important designs and frequently used parts is an example of applying the reader role to a user or group.
- Manager (New): This new role permits a member to manage users without having full admin privileges to permanently delete files. This permission was combined with the previous project admin role.
Groups
Save time by managing your members with groups, a set of members who share a specific responsibility or task. We have heard everyone’s feedback on providing an easier way to assign roles to many team members at once. No longer do you have to manage roles for every member. You can create your own groups, add users, and assign a role. All new groups created can be used hub-wide. You can quickly assign permissions and manage access for multiple people at once.
Upgrade
All new projects you create will include the capabilities outlined above. It’s also easy to upgrade your existing projects to have these new capabilities. Whether your project is currently Open, Closed, or Secret, learn how to upgrade here. Learn more about new and enhanced projects in Fusion here.
Manage Extension support for configurations
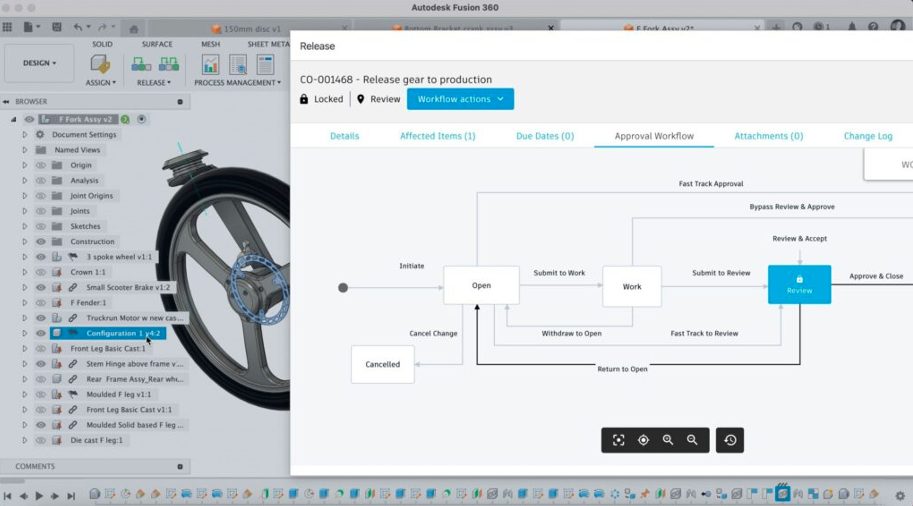
Manage Extension commands have been enhanced to manage configurations consisting of external references. Now configurations can have item numbers assigned to them and can be released via quick release or change orders.
Design and engineering
Streamlined daily workflows
Configurations enhancements
Ever since we launched configurations last year, we’ve been continuing to invest in the exciting new capability. We’ve already made numerous quality-of-life enhancements that will make your configuration experience even smoother.
As a side note, we’ve been thrilled with the response to configurations so far. In 2024 so far, Fusion users have created 346K+ configured designs. Francis Deslauriers, founder of Unik Metal loves how configurations help him iterate quickly and receive valuable customer feedback. “Configurations allow me to work on an entire product line inside of one design,” he says. “It’s really valuable to be able to see how different parts interact and how we can reuse them.”
Ground to parent
Previously, the default behavior of Fusion was that all newly created components were completely free to move relative to the root component. Ground To Parent defines an inherent rigid relationship between a child component and its parent component so that they move together.
This works in the same way as an as-built joint, by locking in place the coordinate systems of the two components, and is indicated by an anchor icon next to the component name. This reduces the clutter in the timeline and saves many clicks to achieve the same effect. Learn more about Ground to Parent.
Insert component command
Previously, the only way to insert a design into another design (to create an external component relationship) was to go to the Data Panel, find the design you want, right-click on it, and choose Insert Into Current Design.
To eliminate confusion with this workflow, we’ve introduced a formal command in the toolbar on the Insert panel. The command opens a file browsing dialog so you can select the design you want to insert and then insert it as an xref component into the current design.
Rounded shell
A new Shell Type option has been added to the Shell command. This exciting new feature allows you to select between Sharp (current method) and Rounded (new method). The Rounded option creates rounded offset corners, and it can produce a partial result when a full one is not possible, allowing you to then modify it using Fusion’s surface tools. Learn more about Shell.
Solid sweep
Solid Sweep is a new sweep type available from the sweep dialogue box. Instead of sweeping a profile across a path, this enables you to sweep a solid body across the path. Learn more about Sweep.
Enhanced customization
Fastener Library enhancements
Last year, we introduced an integrated fasteners library that makes it easy to browse and add various types of fasteners to your designs. This year so far, the Fusion community has run over 282k+ Fastener Library Events. We’ve been continuing to invest in this handy tool and have already enhanced the library in a few ways.
One example is the ability to create a Favorites list, which enhances the productivity of fastener placement by enabling you to create a subset of frequently used parts. You can easily access these parts without the need for searching or browsing. Additionally, The ‘Replace Fastener’ command offers the ability to substitute an existing standard part in a design with a different type. For instance, a hex head bolt can be replaced with a socket head bolt.
Drawings and documentation
Drawing Automation
This year, Fusion users have already exported 2.8M+ drawings. Drawing Automation is a game-changing new feature that makes it even easier to generate accurate drawings. It saves you significant time by automating the tedious steps of creating a drawing.
Drawing Automation offers a ton of handy benefits, and the best part is that it works out of the box with no setup required. This means you can try the feature out with your existing templates or create new templates. It’s fully customizable to suit your preferences. What are you waiting for? Learn how to leverage drawing automation here.
Perspective views
One of the most anticipated drawing features is now available. You can now create perspective views of your model using narrow or wide focal lengths. Perspective views provide a sense of depth that isn’t possible with orthographic views. They more accurately represent how we see objects in real life, which is why they are often used in instruction manuals or assembly documentation.
Match dimensions
Match Dimension enables you to copy tolerances set from one dimension to another. Simply right-click on a dimension and select Match Dimension from the available options.
You can now click on a similar dimension type to apply the same tolerancing to that dimension. You can also box select multiple dimensions to add this to more than one where needed. Note that the dimensions need to be of the same type (i.e., Linear to Linear, Diameter to Diameter, or Radius to Radius) to apply.
Manufacturing
Milling improvements
New toolpath strategies
Blend is an exciting new toolpath finishing strategy for machining a selection of connected faces with passes that blend smoothly between two designated drive curves.
Advanced Swarf is another new strategy that allows straight-sided walls to be machined with the side of the tool. It can create 3-, 4- and 5-axis toolpaths. You can optionally select floor surfaces and/or surfaces to be avoided, giving additional control over the toolpath.
Machine collision detection
Fusion’s machine collision detection feature is designed to identify potential collisions and axis overtravel on your machine tool before running the program. By proactively detecting these issues, it helps ensure the safety of your operations while minimizing expensive machine downtime. Moreover, it allows you to validate and fine-tune your programs more efficiently, instilling greater confidence in their execution.
Simulate connection moves for milling strategies
Movements outside of a toolpath (movements such as tool changes, homing of axes, and initial positioning) can now be simulated with machine simulation. These movements are not only animated in machine simulation, but they are also collision and limit-checked. Note that to use this feature, you must first add the appropriate simulation movements to your post-processor.
Turn/mill improvements
We’ve made multiple turn/mill updates that empower you to run your machines with a greater level of effectiveness. A few highlights include enhanced control over threading tools, the addition of a first pass for threading, a new turning face mode, a new dedicated bar pull strategy, and more. Additionally, we added a new turning groove roughing strategy to replace the legacy turning groove strategy. Check out these enhancements in detail here.
Additive and inspection improvements
Additive Arrange improvements: Select all components & Monte Carlo Packer
Additive Arrange is used to nest multiple components in the build volume of a 3D printer in as little space as possible while avoiding collisions. 2D packers are great for Additive processes that require support structures. 3D packers are used for self-supporting processes such as SLS and MJF. With this version we are releasing a new 3D arrangement type called Monte Carlo.
During the Monte Carlo packing process, you have the option to control the initial orientation of components. Once the orientation is calculated, parts stay in that orientation throughout the process.The packing process is similar to vibrating parts on a shaker table within the build volume of the printer, where parts move into open gaps. The goal of Monte Carlo packing is to move the components as low as possible in the build volume, to minimize the arrangement build height.
The Monte Carlo packer prevents interlocking problems as parts bounce off of each other during the shaking process. To make the selection of multiple components easier, we also added a select all command to the Additive Arrange dialog.
Electronics
Cadence integration
Earlier this year, Autodesk and Cadence joined forces to revolutionize PCB design and 3D modeling. This partnership brings together two leaders in the design and manufacturing world, offering Cadence Allegro X and OrCAD X users a direct pathway to Autodesk Fusion for all their PCB 3D modeling needs, setting new industry standards and opening doors to innovation.
New selection functionality
We’ve upgraded the selection feature! Simply being near a component’s area now highlights it for easy selection. This enhancement is complemented by cross-probing capabilities, allowing for seamless asset identification between schematic and board views, which vastly improves the design navigation process.
Via stitching
Back in March, we introduced a via stitching approach that enables you to enhance your PCB’s electrical and thermal performance effortlessly. With this new feature, you can precisely define via stitching areas and tackle more complex designs while adhering to DRC guidelines—taking your PCB design to the next level with confidence and ease. Learn more here.
Simulation for electronics design
Simulation plays a crucial role in electronic design. It allows engineers to verify parameters and circuits’ functionality before committing to hardware fabrication. The latest update to Fusion’s Schematic workspace includes an enhanced SPICE simulation editor, which supports assets with PSPICE mappings. We also added the capability of exporting your simulation results to an Excel-compatible format, allowing you to perform many more calculations to verify and plot your results.
Additionally, Fusion’s Signal Integrity Extension, which leverages Ansys’ robust simulation capabilities, has also recently introduced coupling analysis. This feature enables designers to evaluate the influence of adjacent signals on critical traces so they can make informed adjustments.
Improved performance & usability
Autodesk Fusion’s electronics workspace is constantly evolving. As we continue to improve and add features to Fusion, we focus on continuously improving the performance during your design time. Earlier this year we adopted SKIA graphics, as well as identified and fixed over 100 reports, making one of the most impactful results for our developing team based on issues solved based on customer feedback.
Digital transformation at your fingertips
Let’s take a brief look back at the steps we’ve taken already this year toward revolutionizing the future of design and manufacturing:
An integrated experience
The future of integrated product design and manufacturing extends to shop floor management. Now, more than ever, it’s important for design and manufacturing businesses to connect people, processes, and data throughout the entire product development lifecycle.
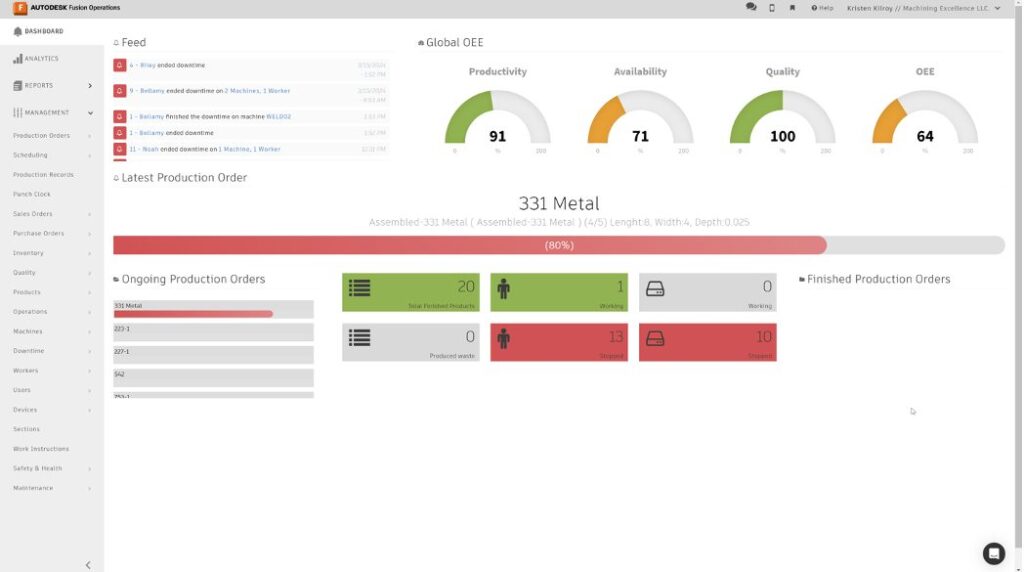
Autodesk acquired the Manufacturing Execution System (MES) Prodsmart in 2022 as a step toward this goal of connecting the stages of product development. It enables access to real-time production information, enabling teams to track product data from design through to production. In an effort to better align the powerful capabilities of Prodsmart with Fusion, we renamed Prodsmart to Autodesk Fusion Operations.
As another step towards our holistic, connected vision for product development, Fusion Manage Fusion 360 Manage with Upchain has now been renamed to Autodesk Fusion Manage. We’re also further integrating our robust partner network into Fusion, including our electronics design integration with Cadence.
Autodesk AI
And, of course, it wouldn’t be a roadmap in 2024 without mentioning the significance of AI – a term that’s undoubtedly on everyone’s minds. Autodesk has been investing in AI for over 10 years, and we’ve absolutely been keeping the AI momentum rolling this year. For example, new Fusion features like drawing automation enable you to automate repetitive tasks in your everyday workflow.
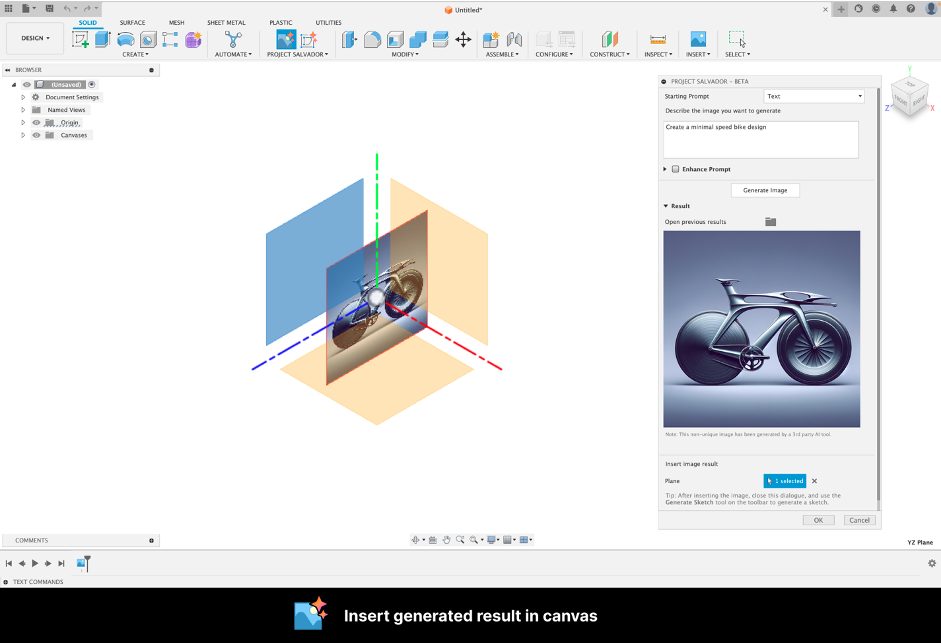
We’ve also been experimenting to find new ways to integrate generative AI into the design process. Project Salvador is a new plug-in for Fusion that leverages generative AI to unlock advanced product design ideation. It chains third-party AI models together with Autodesk Fusion to create seamless ideation workflows between the tools. And our recently announced Research Project Bernini is an experimental generative AI model that quickly generates superior 3D shapes from a variety of inputs, including a single 2D image and more.
Community connection
Do you want early access to exciting new Fusion features? The Autodesk Fusion Insider Program enables its 6.5K+ members to access the next version of Fusion, including all the new features, improvements, and fixes, 3-4 weeks before the general public.
As a member, you’ll gain inside knowledge of when we are deploying an update, what’s new, and what’s coming next. You will also have access to exclusive events, be able to try pre-release functionality, and give feedback directly to our product teams. What are you waiting for? Join the Autodesk Fusion Insider Program here.
Have a specific Fusion question? The Fusion forums are a great place to start. There have been over 1.6M visits to the Fusion form this year so far! You’ll find answers to commonly asked questions and can directly communicate with other Fusion users.
Cheers to the rest of 2024
Phew! That was quite a lot to take in. We’ve already come such a long way in the first half of 2024 and can’t wait to look back on what we release in the second half of the year. Our plans for Fusion are dynamic, and we’ll always do our best to keep you in the loop as the year continues. We value your feedback, insights, and ideas year-round as they are critical to our collective success. And on that note, stay tuned! We’ll share what’s to come for the rest of 2024 in a separate update soon.