
Elevate your design and manufacturing processes with Autodesk Fusion
The Fusion Manufacturing Extension significantly enhances 3-axis machining capabilities by automating workflows, improving toolpath creation, and increasing efficiency, ultimately saving time and costs while delivering superior part quality.
The 3-axis machining center is a staple in the manufacturing industry, known for its versatility in producing anything from simple 2D brackets to intricately shaped components. Maximizing the potential of these CNC machines is crucial for reducing production times and increasing profit margins. For those using Autodesk Fusion, the Manufacturing Extension might seem like a tool designed exclusively for 5-axis programmers. However, its benefits extend to 3-axis machining as well. In this blog, we’ll explore how the Fusion Manufacturing Extension can transform your 3-axis programming, enhancing efficiency, quality, and overall productivity.
Revolutionizing 3-axis programming with the Fusion Manufacturing Extension
Let’s delve into the key capabilities of the Fusion Manufacturing Extension and their advantages for everyday programming tasks on 3-axis machine tools. While these examples focus on plastic injection molds, the functionalities discussed are equally applicable to various other parts and production machining scenarios.
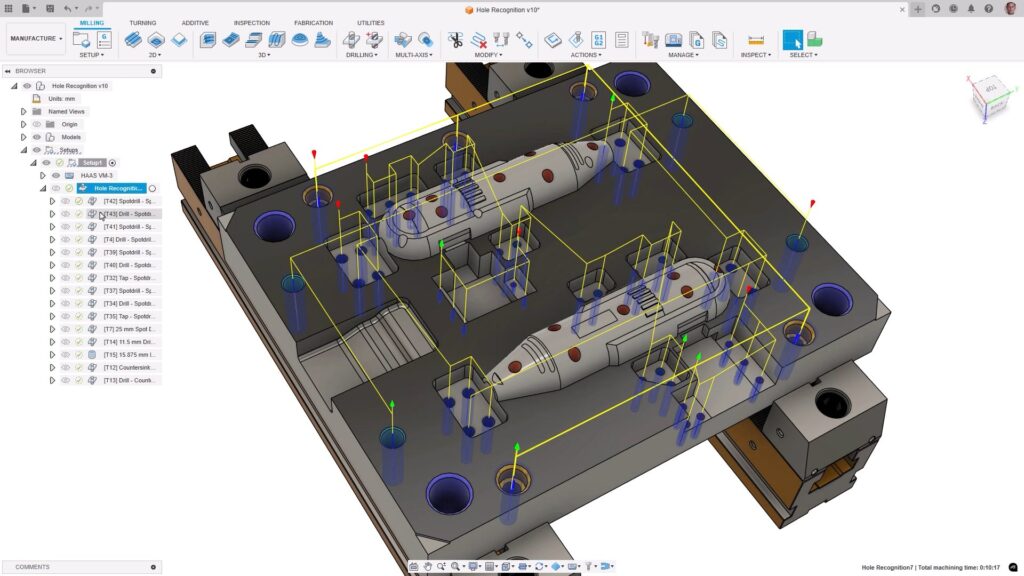
Automatic hole recognition
Many components feature numerous holes of varying types and sizes, making manual programming time-consuming and prone to errors. Automatic hole recognition in Fusion automates this process by detecting the holes and applying customizable templates of standard hole-making processes.
Consider a core plate with multiple holes to be drilled. Manually creating all the toolpaths is labor-intensive and error prone. Automatic hole recognition identifies and lists all the holes, allowing you to apply machining templates to each. For instance, you can flip the hole direction for ejector pins, ignore guide pin holes, and set the correct action for tapped holes. You can also select tool libraries and additional parameters from the options tab. This automation significantly streamlines your hole programming, increasing efficiency and consistency.
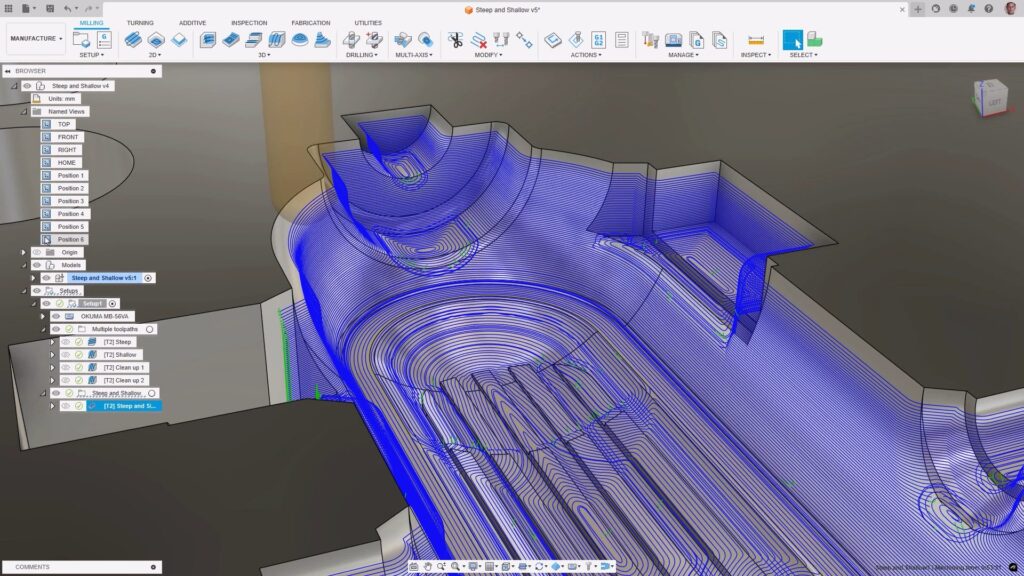
Steep and shallow toolpaths
Complex geometries often have regions that are steep or shallow, requiring different machining strategies for optimal surface finish. Steep and shallow automates this process, simplifying the creation of efficient toolpaths.
A mold cavity with diverse geometrical regions is a perfect example. Manually isolating each area and creating individual toolpaths is inefficient and can compromise surface quality. The Steep and Shallow toolpath identifies and addresses these areas with a single toolpath. You can define threshold angles, choose machining strategies, and set overlap distances to ensure a high-quality finish. This intelligent approach reduces programming time and enhances surface finish.

Corner toolpath
Finishing corners in a machining project is critical for achieving high-quality results. Fusion’s corner toolpath is designed to enhance corner finishing by efficiently removing localized stock while managing cutter load.
A cavity finished with a 6mm ball endmill may still have areas needing further machining with a smaller tool. The corner toolpath simplifies this by identifying these areas and applying the appropriate toolpath strategies. This ensures a smooth and accurate finish, reducing tool wear and saving time.
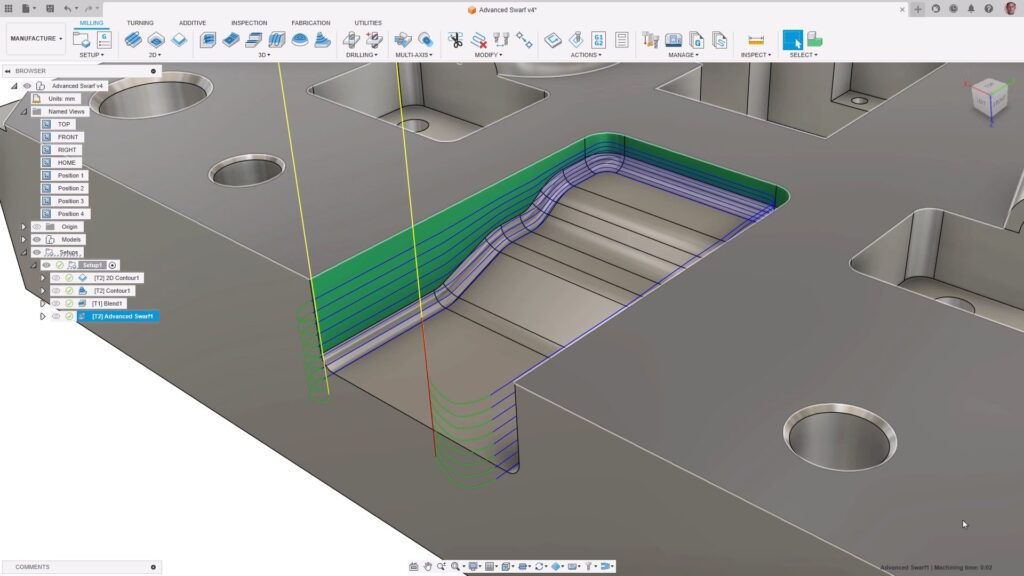
3-axis advanced swarf
Swarf machining, which uses the side of an endmill to follow a geometry shape, is typically associated with 5-axis machining. However, Fusion’s advanced swarf toolpath can create swarf-style toolpaths suitable for 3-axis machines.
A pocket with an irregular floor is a great example. Traditional 2D toolpaths won’t work efficiently. By limiting the axis of motion to 3 and selecting the faces to machine, the Advanced Swarf toolpath can follow the floor shape, creating a quality finish with just 3-axis motion.
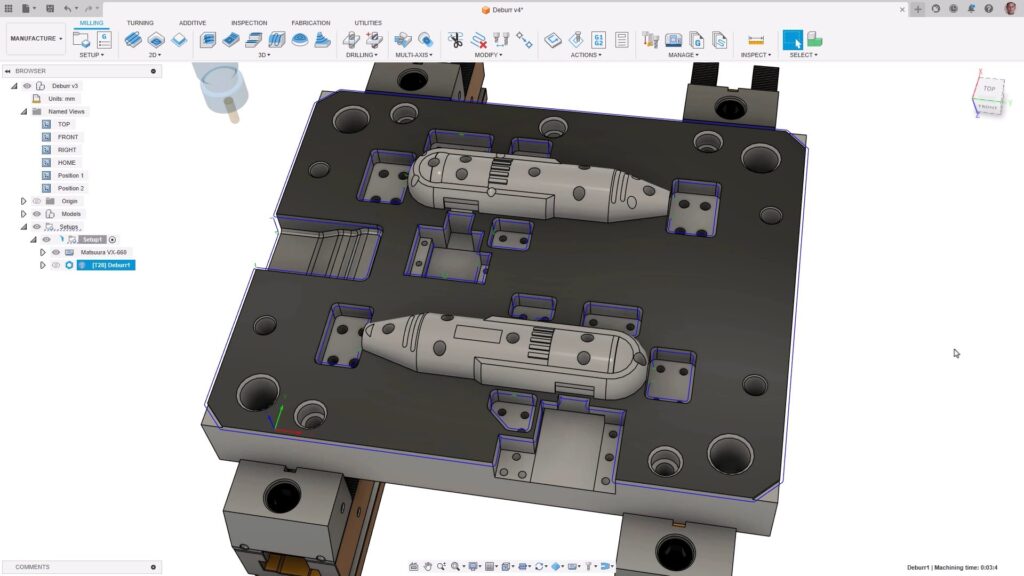
Deburr toolpath
Removing sharp edges and burrs is a common post-machining task usually done manually. Deburr automates this process, creating efficient toolpaths for part deburring.
By selecting edges to deburr manually or automatically, you can define the machining process and edge type. The final toolpath uses a ball endmill to follow and remove burrs, increasing efficiency and accuracy in the post-machining process.
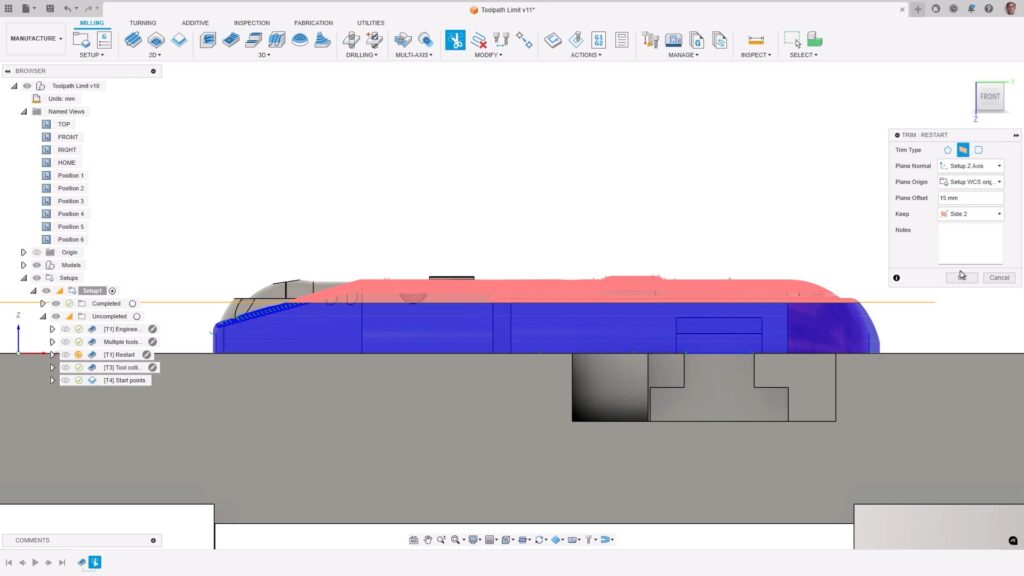
Toolpath modification
Sometimes, your CAM software produces toolpaths that aren’t quite right. Fusion offers a suite of modification tools to tweak toolpaths without recalculating them, saving time and effort.
Whether trimming unnecessary toolpath segments, moving start points, or replacing tools, Fusion’s toolpath modification tools provide flexibility and control. These tools can save hours of programming time and improve machining efficiency.
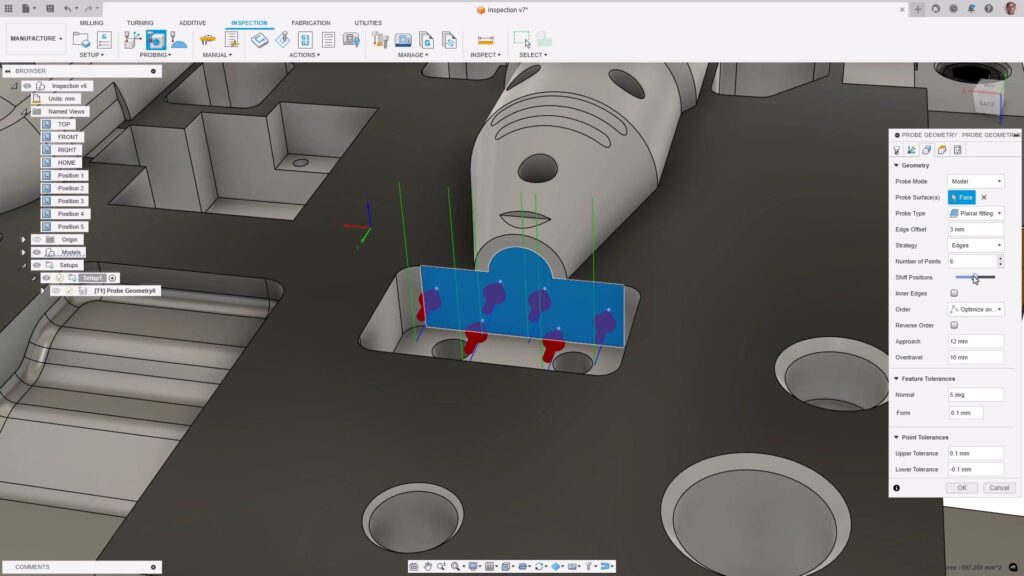
Probing inspection
Traditionally, parts are inspected on a CMM after machining. Probing inspection allows for in-process inspection, identifying errors early and reducing the risk of scrapped parts.
Creating probing operations for features like holes, walls, and corners, you can export these operations as NC programs. The results are recorded, imported into Fusion, and reviewed. This ensures your parts meet quality standards and frees up your CMM for final inspections.
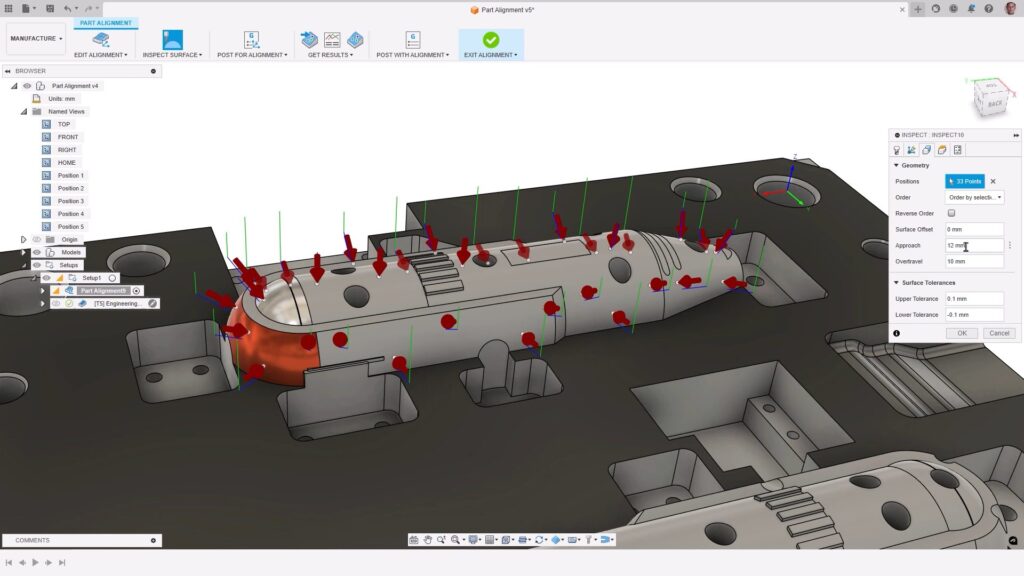
Part alignment
Setting up complex or previously machined parts can be time-consuming. Part alignment streamlines this process, aligning the NC program to the part’s location on the machine.
Using the touch probe, you can determine the part’s current location, import the results into Fusion, and automatically calculate necessary translations. This simplifies setup, ensuring accuracy and efficiency.
The ROI of Fusion Manufacturing Extension
The Fusion Manufacturing Extension offers substantial value for 3-axis machining. By automating workflows and enhancing toolpath creation, it can save significant programming time and improves surface finish quality.
Further, the suite of modification tools and in-process inspection capabilities can further save time and improve quality. Combining these savings, the extension can save up to 30 hours on a single project, translating to substantial monetary value based on your shop rate. These savings shorten the ROI for the extension, but its benefits extend beyond time and cost savings, enhancing your ability to take on complex work and improving your business’s reputation.
Investing in the Fusion Manufacturing Extension is a smart choice for enhancing your 3-axis machining capabilities. Its advanced features, automation, and workflow improvements make it an invaluable tool for boosting productivity and achieving superior manufacturing results. The Fusion Manufacturing Extension can transform your machining processes, delivering significant time and cost savings while improving part quality.