
Elevate your design and manufacturing processes with Autodesk Fusion
Tool and die-making are significant aspects of the modern manufacturing process. Fusion offers built-in features and tools that support the use of tools and dies in the manufacturing process.
In the complex landscape of manufacturing, “tool and die” are must-know concepts for any designer or engineer. These specialized components are key enablers of modern-day mass production, and, hence, it’s necessary for product designers to have a thorough understanding of this field.
In this article, we’ll look deeper into the nuances of tool and die making, its various types, and the benefits Autodesk Fusion 360 offers designers in this field.
Understanding tool and die
Before diving into the technicalities, it’s crucial to distinguish between “tools” and “dies”. While both terms are often used interchangeably, there exist some subtle differences between the two in practice.
In the broadest sense, the term “tool” can be used to describe any mechanical device used in metalworking for cutting, forming, or molding. This includes components like drills, cutting blades, jigs, and fixtures.
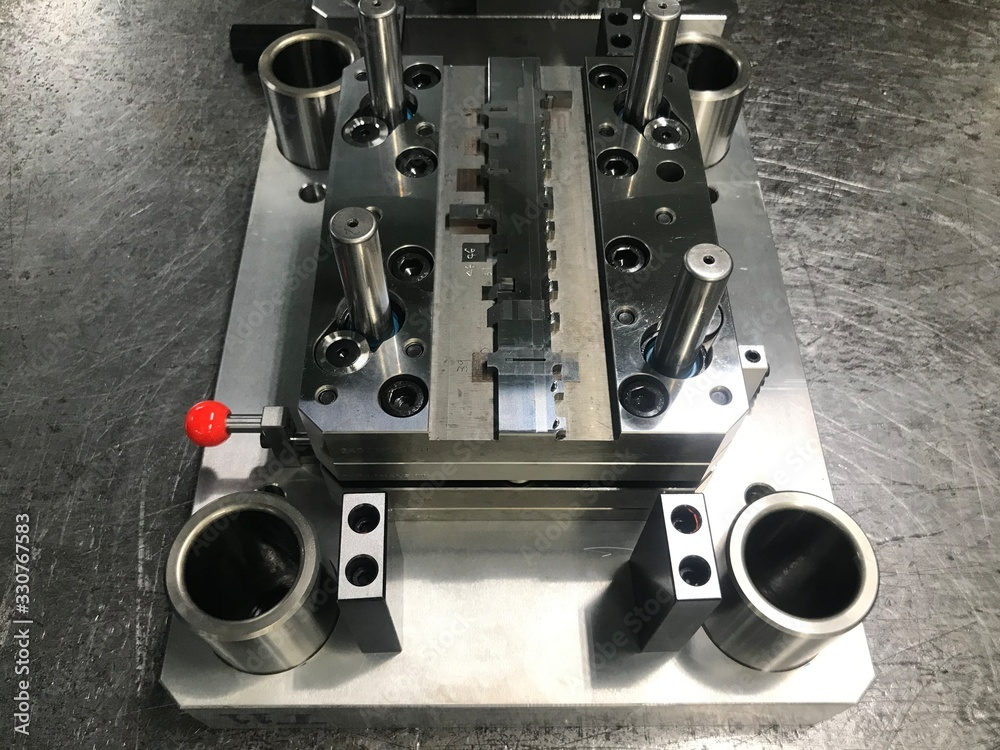
A “die,” on the other hand, is a specialized tool specifically designed to change the shape of a material — usually metal. In this respect, dies are often the female components of a larger tool assembly or press. They work by receiving the material and giving it a new shape through cutting, forming, or processes such as stamping.
A closer look at technical variants
To better understand the technologies, it’s important to explore the different types of dies that exist for use.
Generally, all dies can be classified as one of two types: cutting dies or forming dies. Cutting dies are engineered to remove, shear, or cut material, while forming dies focus on altering a material’s shape without removing any substance. Within these classifications, there are a variety of die types.
- Simple Dies: Simple dies perform a single action — either cutting or forming — per stroke. They are most effective for less complex parts and are a cost-effective choice for simpler designs.
- Compound Dies: More complex than simple dies, compound dies are multi-action tools that execute several cutting and forming actions in a single stroke. They are particularly useful for intricate geometries, as they minimize errors during the workpiece’s transfer between multiple stations.
- Progressive Dies: These dies perform multiple operations on a single blank, with each stroke initiating several actions on different workpiece segments. These are ideal for high-volume production.
- Transfer Dies: Transfer dies operate similarly to progressive dies but use pre-cut blanks that are mechanically transferred between stations. These are ideal for larger or more complex parts.
Why Tool and Die Making Matters
There are a multitude of reasons why product designers should care about the intricacies of tool and die-making.
By grasping the intricacies of how tools and dies work, designers can create products that are not only innovative, but also more cost-effective and easier to manufacture. This knowledge enables better material selection, higher precision, and tighter tolerances — all of which are critical for industries requiring exact specifications like automotive and medical devices.
Furthermore, being versed in tool and die-making fosters effective communication between designers and manufacturing engineers, streamlining the production process and accelerating time-to-market. In essence, a deep understanding of tool and die-making gives product designers a competitive edge, allowing them to innovate within the bounds of what is manufacturable, thereby enhancing both product quality and profitability.
Autodesk Fusion: Elevating the Craft
Autodesk Fusion is a powerful tool for designers in the realm of tool and die-making.
In terms of high-level trends, Fusion’s integration of CAM programming with advanced tool path strategies reflects the broader movement toward the digitization and automation of manufacturing processes. By offering an all-in-one solution for design, simulation, and manufacturing, Fusion is setting new benchmarks in this specialized field, making processes not only efficient and precise but also versatile and safe.
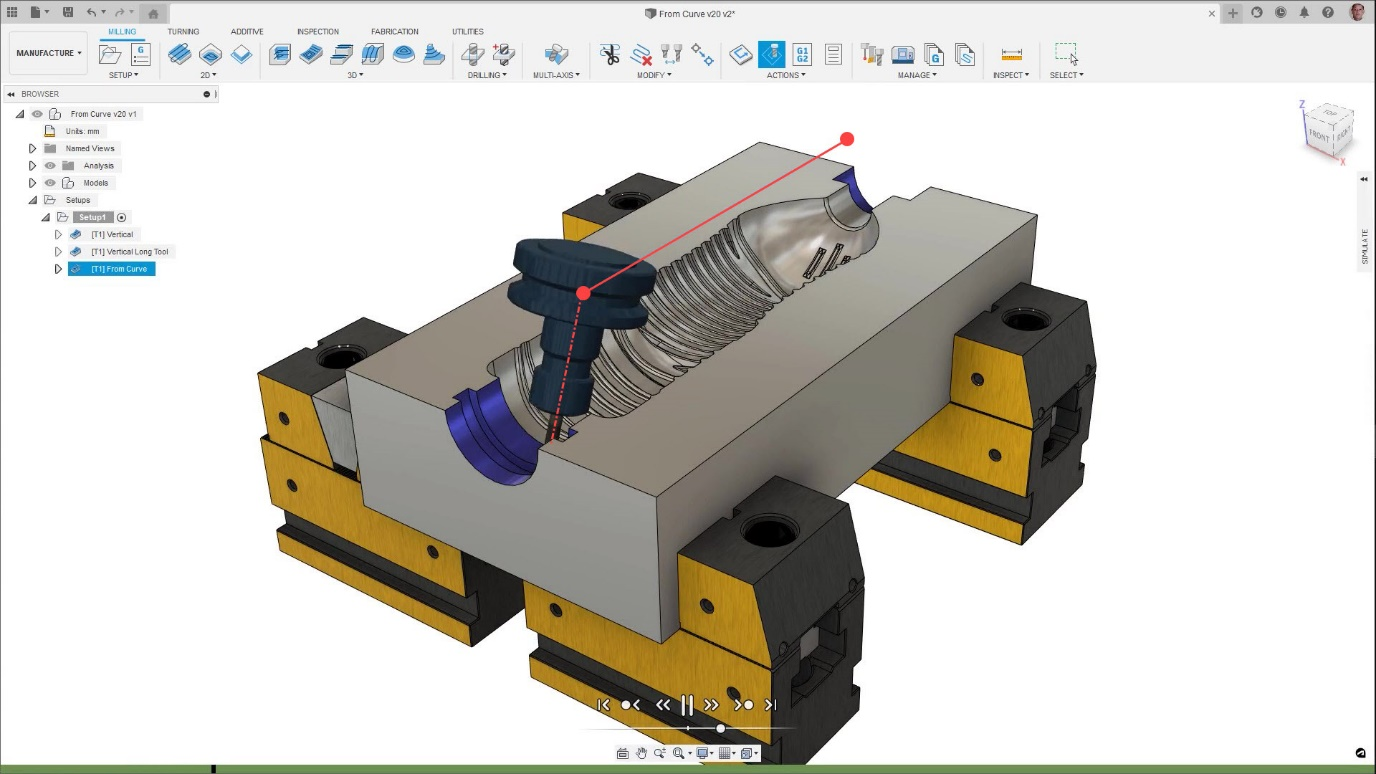
One of the most significant features of Fusion for tool and die-making is its extensive library of tool path strategies, which includes both 2D and 3D tool paths like pocketing, contouring, and drilling. These are essential for machining features and holes in various components. This is then coupled with an adaptive clearing feature, which not only enables rapid removal of large volumes of material, but also minimizes tool wear, thereby extending the lifespan of machining tools.
Additionally, the software has robust ability to provide specialized 3D tool paths that consider three-dimensional part geometry. This enables the machining of complex components like dye forms, mold cavities, and cores to a high-quality surface finish. Fusion further simplifies the machining of cylindrical components through specialized tool paths like rotary pocket and contour, which are particularly useful for machining mold cores and deep cavities.
Other features like collision avoidance features help ensure safe and effective machining position, reducing the risk of costly errors and enhancing overall safety.
Master tool and die
Professionals involved in modern manufacturing require a deep knowledge of tool and die technologies. Tools like Autodesk Fusion empower users to harness knowledge into practice, navigate the complex landscape of tool and die, and ensure that products are produced with the best quality possible.