
Elevate your design and manufacturing processes with Autodesk Fusion
When you think of artificial intelligence (AI), chances are that a vision of supremely intelligent computers and robots taking over the world springs to mind. We’ve been conditioned by sci-fi books and movies to fear the worst.
The reality is far different; mundane even. AI is essentially the operation of algorithms that automatically optimize themselves as they go—a process known as ‘machine learning.’ It may sound simple, but it yields powerful results that are revolutionizing the world. This includes the manufacturing industry where AI-assisted CNC machining is currently streamlining the manufacturing process for many businesses.
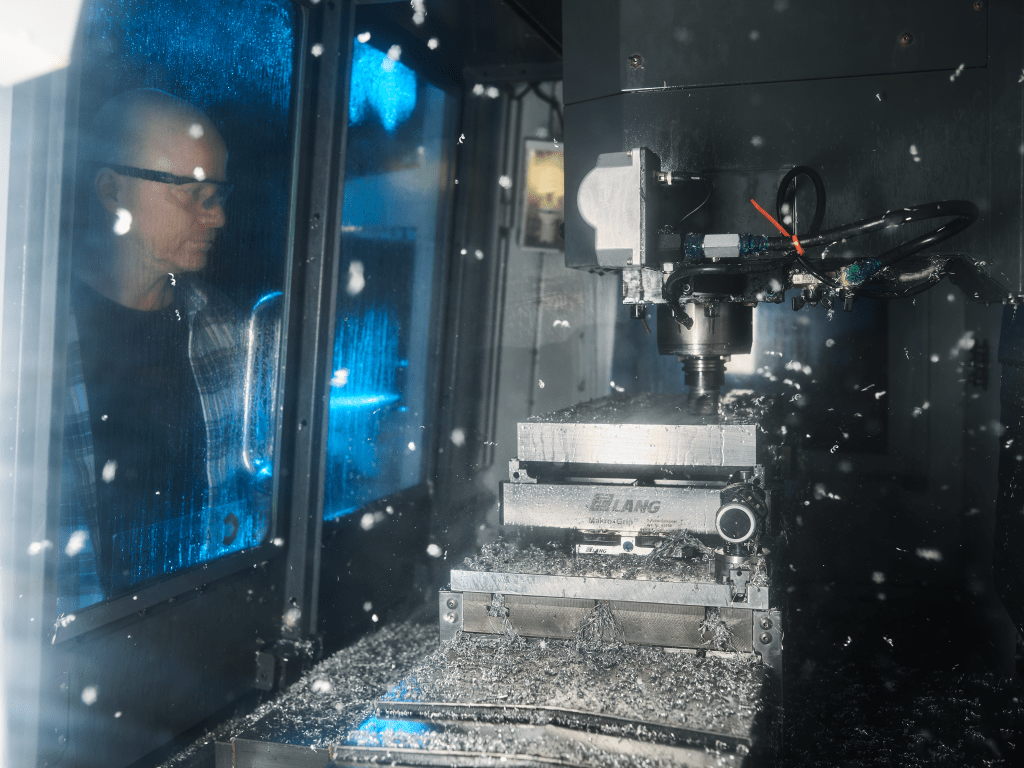
What is CNC machining?
CNC machining is a process that uses a computer linked to a machine with interchangeable tools. A machinist programs the computer with a design, with some machines allowing the automatic import of 3D drawings from CAD software like Autodesk Fusion. The machine then carries out machining tasks such as cutting, grinding, drilling, and lathing.
Although the process is highly automated, CNC machinists are required to change the tools, set up the computer, and calibrate and monitor the operation of the machine.
How does AI improve CNC machining?
Just like any other industrial process, CNC machining has the potential to go wrong sometimes. That’s where AI can be incredibly useful. Let’s explore the ways AI-powered tools in Autodesk Fusion can help your team take its CAM process to the next level.
Drawing Automation
Drawing Automation in Fusion streamlines the design detailing process, significantly accelerating drawing creation. It automatically identifies purchased components and excludes them from drawing sets, while also generating dimensioning strategies that fully document designs in a matter of seconds.
This capability allows manufacturers to cut down on manual work, minimize errors, and speed up the time-to-production. By ensuring consistency and boosting productivity, this automation empowers teams to concentrate on innovation and refinement instead of repetitive tasks.
Toolpath optimization
AI analysis can optimize toolpaths by adjusting them to achieve the highest productivity and minimal wear. Autodesk’s collaboration with CloudNC has reduced toolpath programming times in Fusion by up to 95%.
Additionally, the Autodesk Assistant incorporates natural language AI prompts for CNC machining, simplifying the process of cutting parts. For example, you can give a command like “machine the top face of this part,” and Fusion will automatically select the appropriate machining strategy.
Simulation
CNC machining is only one component of the broader manufacturing landscape, though. Achieving profitability requires optimizing the entire production process, including factory operations. Connecting building and manufacturing processes unlocks unprecedented efficiency. It allows for quicker, more informed decision-making, confident achievement of production targets, and reduced time to market and inventory costs.
Simulation plays a crucial role in these informed decisions by highlighting necessary changes in design, workflows, and products before incurring expensive physical alterations.
Streamlining business logistics
Going a step further, the cloud-based Design Automation Service API for Fusion enables anyone to incorporate Fusion’s automation features into their business workflows. Many of our customers are using this capability to invest in manufacturing automation for online quotations and machining. This helps them attract more business and boost profit margins.
Future of AI-assisted CNC machining
The future of CNC machining will almost certainly be a more connected one, with the whole manufacturing process linked via cloud computing, AI optimization, diagnostics, and fault correction.
Will human CNC machinists even be required in the future? Yes, at least for the foreseeable future, someone needs to operate the computer, load the designs, oversee the process, and rectify any faults. The dystopian view of intelligent computers taking over the world is far-fetched, but they will certainly play a more prominent role in manufacturing over the years to come.