
Elevate your design and manufacturing processes with Autodesk Fusion
This post is also available in: English (Anglais)
Da smarte Geräte immer komplexer werden, sind Hersteller, die cloudbasierte Produktentwicklungslösungen wie Fusion 360 verwenden, der Konkurrenz voraus. Dieser Artikel befasst sich mit den Daten und gibt Ihnen Ratschläge für die Einführung eines optimierten Workflows zwischen den Beteiligten.
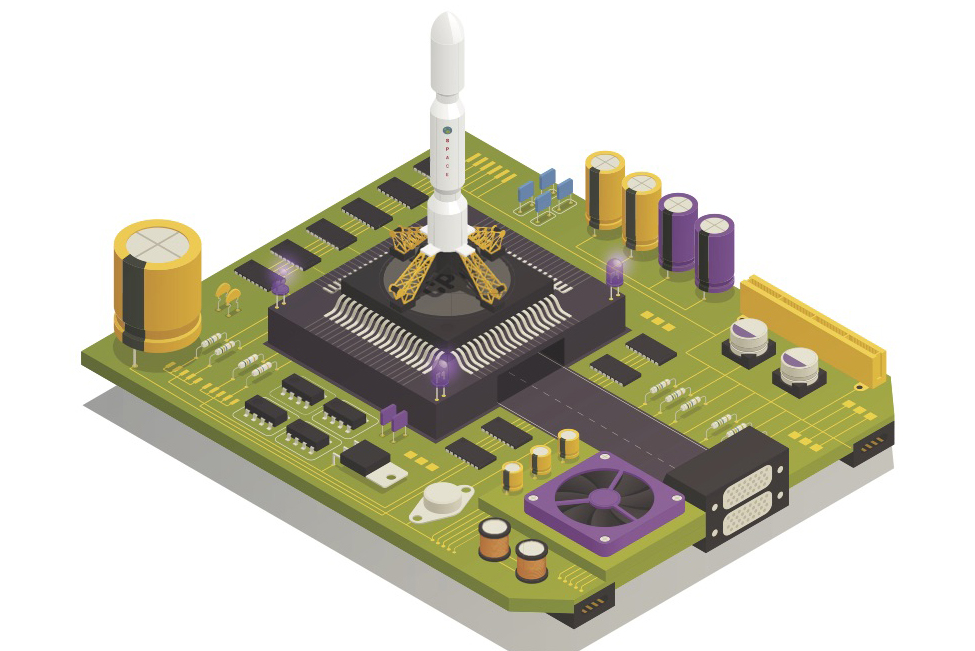
Immer mehr traditionelle mechanische Produkte verwandeln sich in smarte, vernetzte Geräte, die Elektronik, elektrische Verteilersysteme und Onboard-Software benötigen. Dieser einzelne Trend verändert die Arbeitsweise der Hersteller dramatisch, denn smarte Geräte erfordern die Zusammenarbeit mehrerer Entwicklungsteams, die Etablierung neuer Arbeitsabläufe und die Lösung neuer Probleme, die in direktem Zusammenhang mit den Konstruktionseinschränkungen und Datenverwaltungsproblemen von vernetzten Produkten stehen.
Neue, von Lifecycle Insights in Auftrag gegebene Untersuchungen deuten auf ein IT-Ökosystem für die Produktentwicklung hin, das besser für die Herstellung intelligenter, vernetzter Produkte gerüstet ist, ohne Zeitpläne oder Budgets zu gefährden. In dieser Reihe von Blog-Beiträgen werden wir uns einige wichtige Erkenntnisse aus dieser neuen Studie ansehen und herausfinden, welche Schritte Hersteller unternehmen können, um die Effizienz und Leistung zu verbessern.
Smarte Geräte
Die Komplexität von smarten, vernetzten Produkten nimmt in einem noch nie dagewesenen Tempo zu, angetrieben durch eine Kombination aus digitalen Innovationen, die diese Produkte möglich machen, und einer steigenden Nachfrage der Verbraucher nach Produkten mit diesen neuen Funktionen.
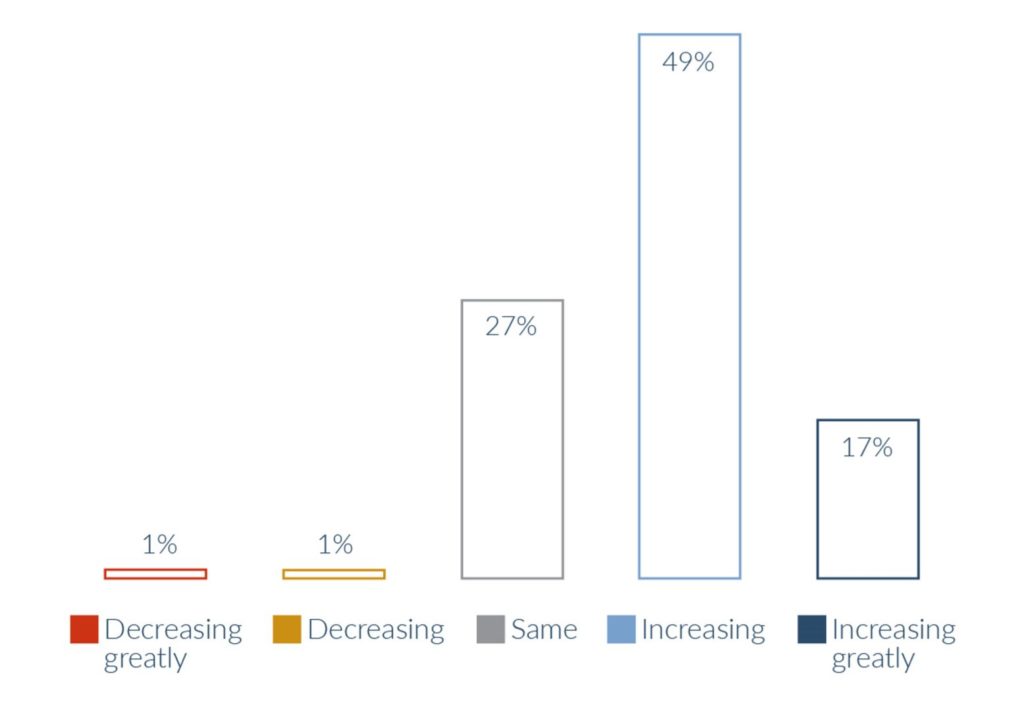
Abbildung 1. Die Mehrheit der Elektronikingenieure ist der Meinung, dass die Komplexität von Leiterplatten und Elektronik entweder zunimmt oder stark ansteigt.1
In einer kürzlich durchgeführten Studie gab eine Mehrheit (zwei Drittel) der Elektronikingenieure an, dass die Komplexität von Leiterplatten entweder zunimmt oder stark zunimmt (siehe Abbildung 1). Dies kommt nicht überraschend. Jüngste Fortschritte wie Multi-Board-Systeme, starrflexible Bestätigungen, IC-to-Board-Gehäuseschnittstellen und andere Innovationen fügen dem Produktdesign neue Komplexitätsebenen hinzu.
Die multidisziplinäre Design-Herausforderung
Eine wichtige Folge der zunehmenden Komplexität ist die Umwandlung traditioneller Design- und Entwicklungsprozesse in multidisziplinäre, domänenübergreifende Unternehmungen, an denen mehr Design-Beteiligte mit vielen verschiedenen Standpunkten beteiligt sind. Einige der neuen Teilnehmer an diesem Prozess sind:
- Analysten, die die elektronische Energieverteilung und Signalintegrität lösen
- Spezialisten, die das Chip-Packaging des Produkts entwickeln
- Experten, die die Herstellbarkeit des endgültigen Designs beurteilen (Design For Manufacturing – DFM)
Wenn mehr Beteiligte in den Prozess einbezogen werden, kommt natürlich eine weitere Ebene der Komplexität hinzu, da diese größeren Teams auf neue Art und Weise innerhalb sich schnell entwickelnder Arbeitsabläufe zusammenarbeiten. Die Entwicklung hochwertiger smarter Geräte erfordert neue Technologien, die die Zusammenarbeit dieser größeren und vielfältigeren Teams erleichtern.
Warum fortschrittliche Hersteller enorme Wettbewerbsvorteile haben
Das Aufkommen smarter, vernetzter Geräte verändert die Arbeitsweise von Herstellern dramatisch. Eine große Frage, die sich stellt, wenn Hersteller eine Änderung der vertrauten Arbeitsabläufe in Erwägung ziehen, ist: Wird es sich lohnen?
In einer kürzlich durchgeführten Studie über Hersteller untersuchten die Forscher die Ergebnisse basierend darauf, wie « fortschrittlich » die Organisation war. Mit anderen Worten: Wie sehr verließ sich der Hersteller auf neue IT-Systeme anstelle von etablierten Systemen? Die Studie teilte die Befragten in drei Gruppen ein: sehr progressiv, mäßig progressiv und am wenigsten progressiv.
Die Studie zeigte zwei sehr wichtige Unterschiede zwischen den drei Gruppen:
- Die fortschrittlichsten Unternehmen geben weniger aus.
Die fortschrittlichsten Unternehmen geben im Durchschnitt jährlich 1.038.000 $ weniger für Prototyping und Tests, Änderungsaufträge und PCB-Respins aus als die am wenigsten fortschrittlichen Unternehmen (siehe Abb. 3). Außerdem sparen sie jährlich 491.500 $ pro Projekt und 183 Tage pro Projekt ein, indem sie weniger PCB-Respins durchführen. Diese Informationen scheinen zu bestätigen, dass sich die Einführung neuer Technologien tatsächlich auszahlt.
- Die fortschrittlichsten Unternehmen verwenden einen hybriden Ansatz.
Die fortschrittlichsten Unternehmen nutzen Cloud-basierte Elektronik-CAD-Anwendungen in deutlich höherem Maße als die beiden anderen Gruppen, allerdings nicht isoliert. Einige nutzen dateibasierte, lokal installierte Anwendungen zusätzlich zu Cloud-basierten Tools, während andere Elektro-CAD-Anwendungen nutzen, die mit On-Premise-Servern verbunden sind. Diese Art des hybriden Ansatzes gilt nicht als Best Practice, da sie die Arbeitsabläufe komplexer machen kann. Aber diese Ergebnisse zeigen, dass die Praxis funktionieren kann, wenn die Hersteller neue Technologien nutzen, um alle auf der gleichen Seite zu halten.
Nutzung von Cloud-Lösungen zur Optimierung der Produktentwicklung
Die Hersteller integrieren immer mehr Leiterplattensysteme in smarte Produkte. Mehr Leiterplatten bedeuten oft auch mehr Probleme, wie Fehler, Überhitzung und Probleme mit der Signalintegrität. Um diese Probleme zu lösen, verwenden Hersteller einen kollaborativeren Ansatz, um die digitale Definition einer Leiterplatte gemeinsam zu nutzen und es allen Beteiligten zu ermöglichen, nahtlos an demselben Design zu arbeiten.
Herkömmliche Strategien, die auf E-Mail-Dateien basieren, greifen zu kurz, da E-Mails leicht verloren gehen oder versehentlich gelöscht werden. Designdateien, die an E-Mails angehängt sind, werden schnell veraltet, was zu Problemen bei der Versionskontrolle führt und das Risiko birgt, dass Ingenieure an veralteten Versionen arbeiten. Aus diesem Grund setzen die fortschrittlichsten Hersteller – also diejenigen, die fortschrittlichere IT-Systeme eingeführt haben – auf eine Mischung aus dateibasierten, lokal installierten und Cloud-basierten Lösungen, um Dateien auszutauschen und alle Beteiligten auf dem gleichen Stand zu halten (siehe Abb. 4).2
Einer der kritischsten Punkte bei der Zusammenarbeit ist die zwischen Maschinenbauingenieuren und Elektroingenieuren. Aktuellen Untersuchungen zufolge nutzen die fortschrittlichsten Unternehmen Cloud-basierte Lösungen, um Definitionen zwischen Elektro- und Maschinenbauingenieuren auszutauschen. Dies hilft zum Beispiel sicherzustellen, dass elektrische Komponenten in die Gehäuse des Produkts passen, und erleichtert Analysen zur Flüssigkeitskühlung, um Überhitzung zu vermeiden und andere Risiken zu mindern.
Cloud-basierte Lösungen erleichtern auch den freien Informationsfluss zwischen den Teams für Mechanik und Elektrotechnik, wenn Konstruktionsänderungen vorgenommen werden. Manuelle dateibasierte Export- und Import-Austauschsysteme sind ungeeignet, da die Ingenieure nicht sehen können, was gegenüber der vorherigen Iteration geändert wurde. Um Verwirrung zu vermeiden, können sie mit dem Austausch von Ideen bis spät im Entwicklungszyklus warten, aber diese Taktik führt oft zu kostspieligen Projektverzögerungen.
Der Austausch von Designänderungen mit einer Cloud-basierten Lösung ist viel reibungsloser und ermöglicht es Maschinenbau- und Elektronikingenieuren, Designs früher und häufiger auszutauschen, was den Lebenszyklus der Produktentwicklung verbessert und kostspielige Änderungen in der Spätphase und Verzögerungen verhindert (siehe Abb. 6).
Jeder Hersteller von smarten, vernetzten Geräten wird einen etwas anderen Prozess für Produktdesign und -entwicklung haben. Dennoch können alle Hersteller von drei einfachen Empfehlungen profitieren, wie unsere Forschung zeigt:
1. Verstehen Sie, ob und wie sich die erhöhte Design-Komplexität auf den Lebenszyklus der Produktentwicklung auswirkt.
2. Bewerten Sie die Auswirkungen auf Zeit und Kosten, wenn Sie mit dem aktuellen Prozess weitermachen.
3. Erwägen Sie die Ergänzung von Elektro-CAD-Anwendungen durch Cloud-Lösungen, um die gemeinsame Nutzung von Konstruktionen und die Zusammenarbeit zu erleichtern.
Sind Sie bereit zu sehen, wie Cloud-basierte Tools Ihren Arbeitsablauf positiv beeinflussen können? Sehen Sie sich Fusion 360 an, die einheitlichste Cloud-basierte multidisziplinäre Entwicklungsplattform für PCB, MCAD, CAM, Datenmanagement, Simulation und Zusammenarbeit.
Quellen:
1. Lifecycle Insights’ 2020 Engineering Executive Strategic Agenda Study
2. Lifecycle Insights’ 2020 Product Development IT Ecosystem Benchmark Report