
Elevate your design and manufacturing processes with Autodesk Fusion
This post is also available in: Italiano (Italian) 日本語 (Japanese)
The Fusion Manufacturing Extension
The Fusion Manufacturing Extension goes beyond and 5-axis machining. It also unlocks advanced sheet metal nesting, additive manufacturing tools and more. Explore some of the extension’s top capabilities here.
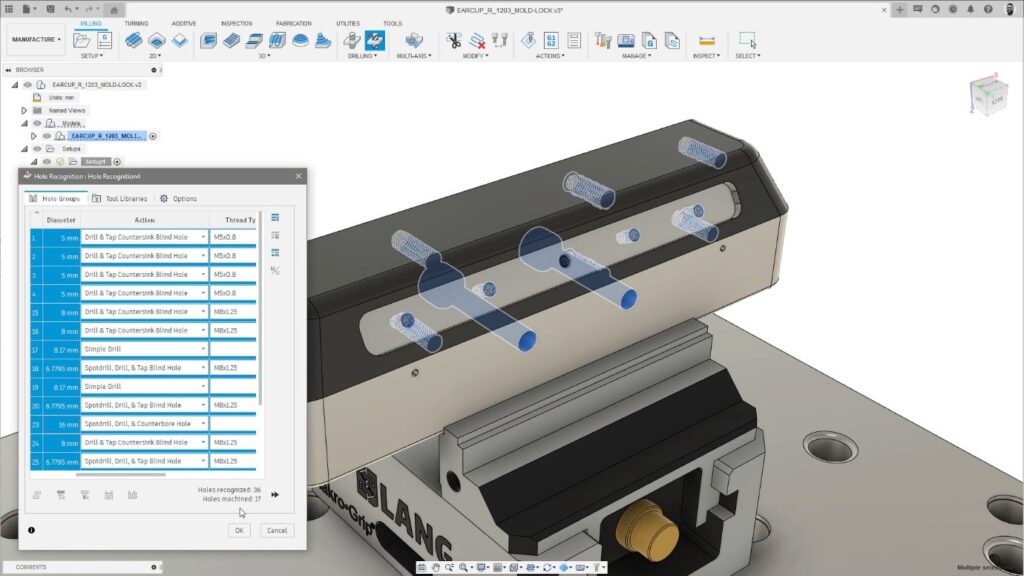
The Fusion Manufacturing Extension certainly does include a wealth of simultaneous 4- and 5-axis technology, but it’s not just a fancy 5-axis add-on for Fusion. As its name suggests, The Fusion Manufacturing Extension unlocks additional functionality for manufacturers using CNC machinery to produce components, along with those nesting sheet metal and 3D printing using metal materials.
Let’s unbox the Fusion Manufacturing Extension and see what CAM programming goodies are inside.
Automated whole-part machining
Programming simple 2D and 3D shapes generally isn’t too difficult. It’s easy to decide which strategies to use, they’re pretty quick to produce, and you don’t need too many of them to fully machine components. Creating the necessary NC machining code is quick and painless, meaning you can rapidly produce parts.
However, as the complexity and precision of parts increase, it can be much harder to decide which machining strategies you should use to ensure parts are machined fully and accurately. With so many ways to finish machining a part, the task for the CAM programmer can be overwhelming, resulting in longer programming times and an increased likelihood of costly mistakes.
The Fusion Manufacturing Extension addresses this with a range of “whole part strategies” that can accurately machine components with a small number of highly effective toolpaths. For example, the Steep and Shallow strategy intelligently recognizes separate regions of the component. It then uses different optimized toolpath types to machine them.
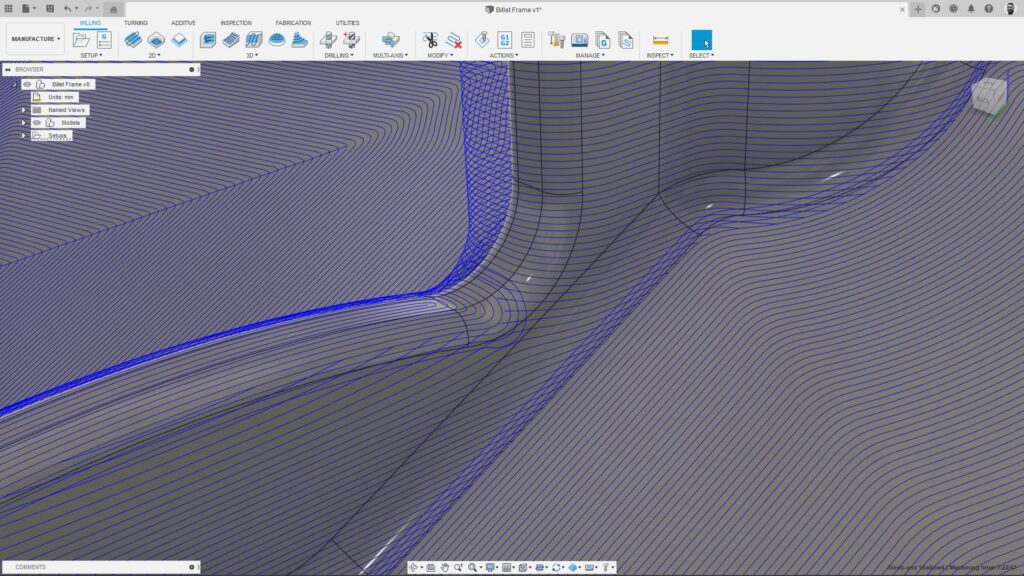
Steep and Shallow is way more than just a clever toolpath. It’s a 4-in-1 strategy with individual access to parallel, scallop, and contour toolpaths and the added ability to combine them to produce the Steep and Shallow toolpath itself. With independent controls over stepover and stepdown, toolpath ordering, region overlap, toolpath smoothing, and automatic wall clearance, Steep and Shallow simplifies the programming of complex geometry. Additional smoothing options control the toolpath point distribution, letting you tailor the toolpath point output to suit your controller.
What may be less obvious is that Steep and Shallow is an attractive option for users of 3-axis and multi-axis machines, with automatic collision avoidance for even greater toolpath safety and efficiency.
Automated hole recognition and drilling
Drilling holes is one of the most common CNC machining tasks. The Fusion Manufacturing Extension streamlines this tedious process by recognizing holes in 3D models (including models imported from other CAD systems) before using pre-defined (configurable) templates to create efficient 3-axis and 3+2 drilling cycles. This includes spot drilling, tapping, threading, reaming, and more. Templates allow company-wide best practices to be defined, recorded, and shared across teams for greater consistency, improved productivity, and a significant reduction in non-value-added tasks that can waste time and lead to human error.
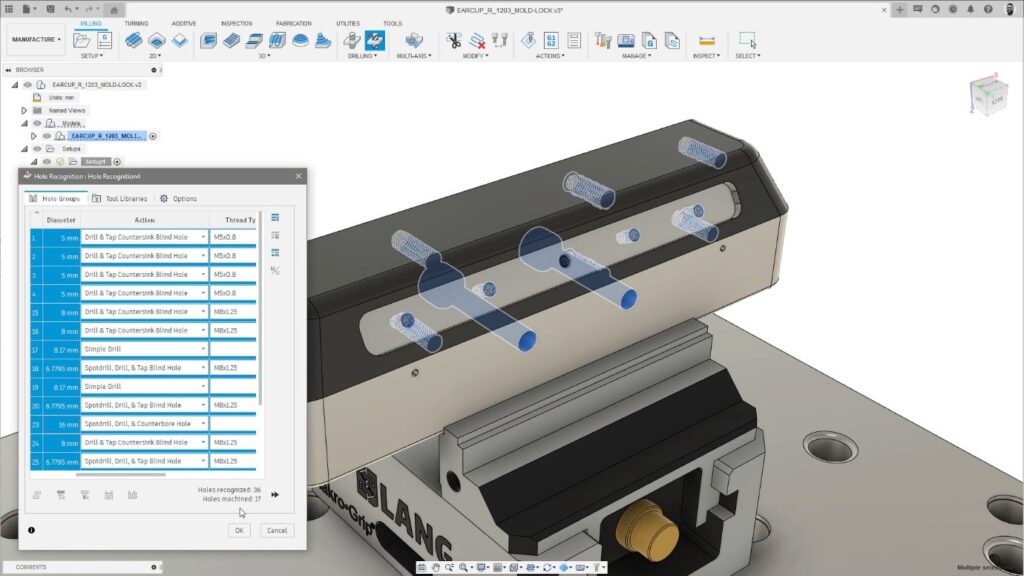
Geometry probing, surface inspection, and part alignment
The core version of Fusion includes workpiece coordinate system (WCS) setup probing that you can use with spindle-mounted probes to automate simple part setup on CNC machines. The Manufacturing Extension goes further, adding Geometry Probing, Surface Inspection, and Part Alignment capabilities to monitor the quality and performance of the entire CNC machining process.
These additional tools allow you to measure parts after specific machining operations to validate that the state of the part is as expected. Catch any non-conformance early in the process and use the measurement data to make informed decisions to salvage parts. If parts are already non-conforming, it is better to resign them to the scrap bin and avoid wasting further machining time or money making a bad part worse.
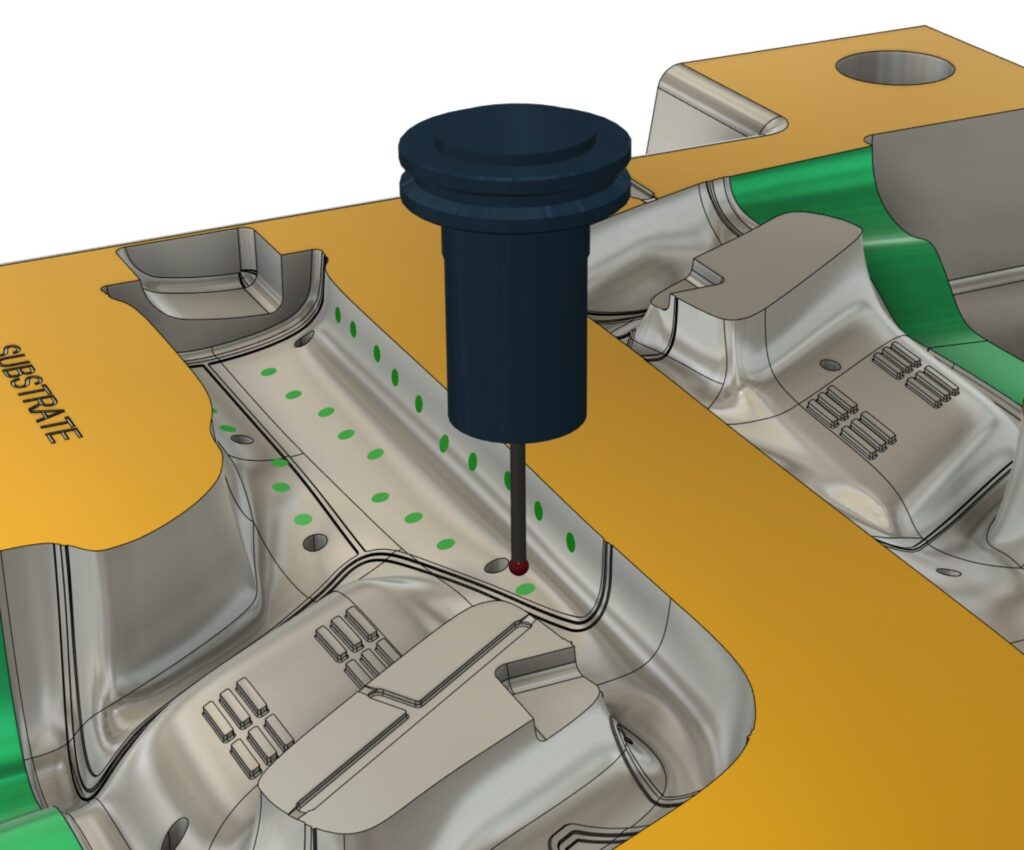
Using probing to automate part setup is especially useful in cases where the parts you’re machining are large, heavy, or non-prismatic in shape and require considerable time and effort to set up manually. Surface inspection allows you to measure key points to determine where the actual part is on the machine. You can then use this data to adjust the WCS to allow the NC code to align with the part. In many cases, automated part setup only takes a few seconds or minutes — but it can save up to 80% of time spent on manual setup.
“We recently used the part alignment capabilities within the Manufacturing Extension to machine some parts out of aluminum that we cut to size from 1″x5″ bar. When we came to start machining on our Haas VF2 machine, we noticed the bar stock had been cut out of square. We were on the verge of having to scrap and reorder well over $200 in material and have our machine sitting idle the rest of the day.
By using the part alignment tools in Fusion, we were able to use a spindle mounted probe to measure each piece of stock and automatically adjust the machining orientation so that every part fit in a less than ideal stock envelope. All the parts came out perfectly. The total savings paid for at least half the annual cost of the Manufacturing Extension, it’s clear the extension pays for itself in a few weeks.”
— Patrick Fee, Shop Supervisor, Conturo Prototyping
Toolpath modifications
In an ideal world, the toolpaths created by a CAM system would be perfect the first time, every time, and do exactly what the CAM programmer needs. In reality, programmers often need to change toolpaths – possibly removing localized regions to avoid duplicate cutting, restricting the Z-depth, or deciding to use a different tool holder.
This is where the powerful Toolpath Modification options provided in the Manufacturing Extension can help. They allow CAM programmers to make small but significant changes to toolpaths without recalculating them completely. Toolpath modifications include:
- Trimming a toolpath to a sketch/polygon/plane – allows you to remove local regions of a toolpath.
- Deleting one or more toolpath passes/segments – a variation on the above limiting option that allows you to remove entire portions of a toolpath.
- Moving tool entry positions – allows you to change the position where the cutting tool enters the material on closed toolpath passes
- Replacing the tool – For example, updating the toolpath to use an alternative tool. Note: the tip must remain unchanged, but the feeds & speeds, holder assembly, and length below the holder can be changed.
Check out this article to learn more about toolpath modifications.
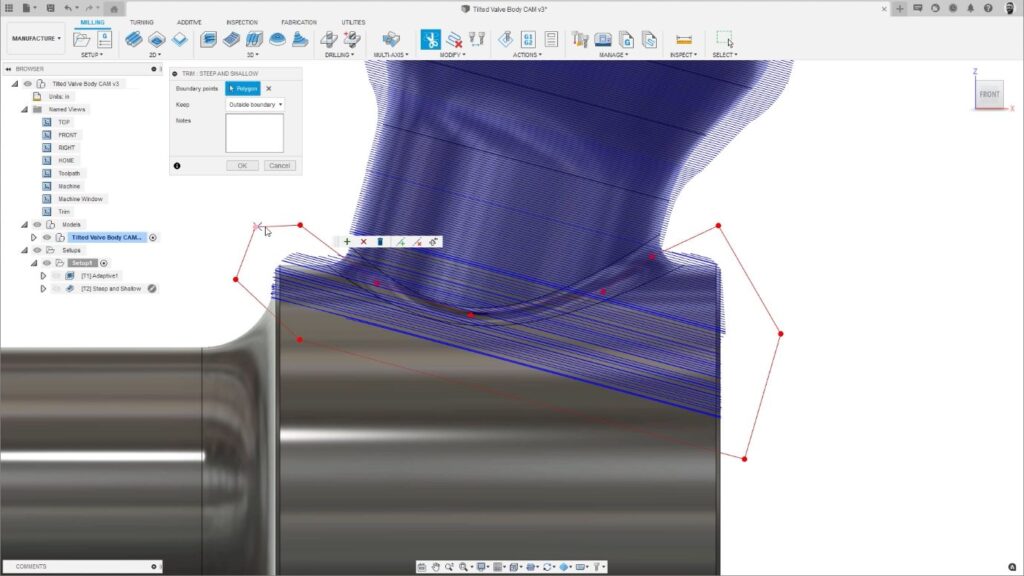
4- and 5-axis simultaneous
Up until this point, everything mentioned so far benefits 3-axis users, clearly highlighting the advantages of having the Manufacturing Extension even if you don’t have a 4- or 5-axis CNC machine tool. However, it wouldn’t make sense to write an article on the Manufacturing Extension and not mention the powerful capabilities for 4-axis and 5-axis simultaneous machining.
These features complement the 3+2 machining capabilities in Fusion core and include dedicated toolpaths, such as Swarf, multi-axis contour, multi-axis flow, and 4-axis Rotary, as well as multi-axis options in the Steep & Shallow strategy. Choose from a range of tool axis options to precisely control the motion of the CNC machine for greater precision and surface finish.
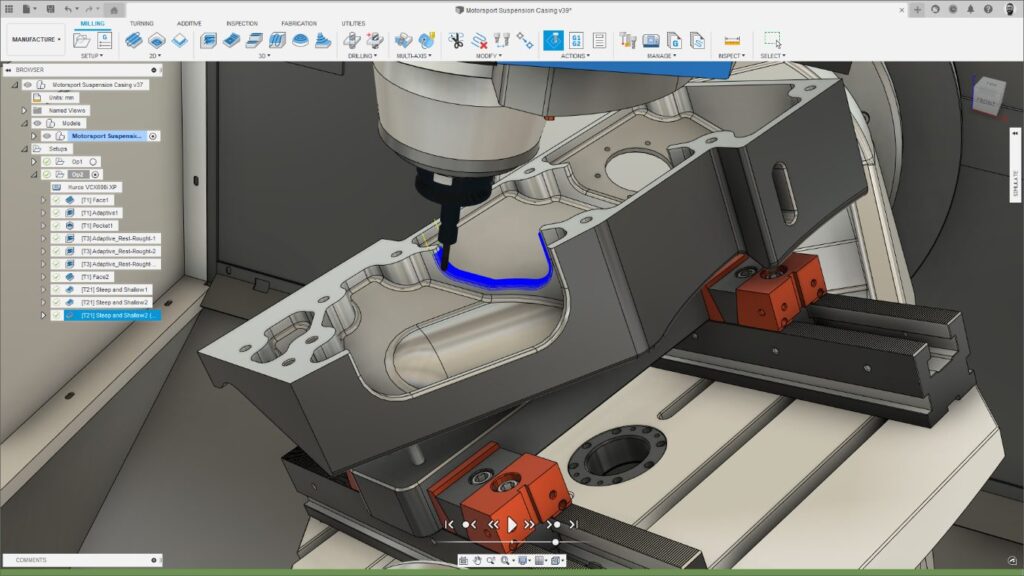
Options include “lead/lean” (derived from the underlying surface geometry) and options to drive the tool axis motion either to or from user-defined points or curves. Advanced options help generate smooth machine motion to minimize defects on the machined part, with tool axis limits to create NC code that will stay within the physical limits of the CNC machine.
For the most complex parts, automatic collision avoidance can tilt the tool holder assembly away from the part. You can access a range of tilting options to achieve the precise motion needed. Powerful toolpath simulation and machine animation help boost confidence by quickly identifying problems early so you can rectify them before they become expensive mistakes on the actual machine.
“The 5-axis capabilities in Fusion are so powerful yet simple to use. Programs that used to take hours now take minutes.”
—Phil Butterworth, Programmer, MJK Performance
Check out this article to learn more about the 5-axis capabilities of the Manufacturing Extension.
So, there you have it. The Fusion Manufacturing Extension unboxed. Whether you’re using a 3-axis or 5-axis CNC machine, it’s packed full of tech to help you produce and spend less time creating top-quality NC machining code.
Comprehensive nesting tools
Associative nesting tools enable you to convert 3D assemblies into precise 2D nested solutions ready for CAM programming, and automatically update nests if your original 3D design changes. Additionally, multi-sheet nesting capabilities intelligently group parts together based on thickness and other material-specific parameters, giving instant insights for costing, quoting, and ordering.
Integrated 3D printing functionality
Prepare 3D models for metal-based additive manufacturing with automatic part orientation, fully associative support structures, and 3D printing file exports. Use thermal simulation tools to validate the 3D printing process to avoid costly print failures and deliver better quality parts the first time, every time.