
Elevate your design and manufacturing processes with Autodesk Fusion
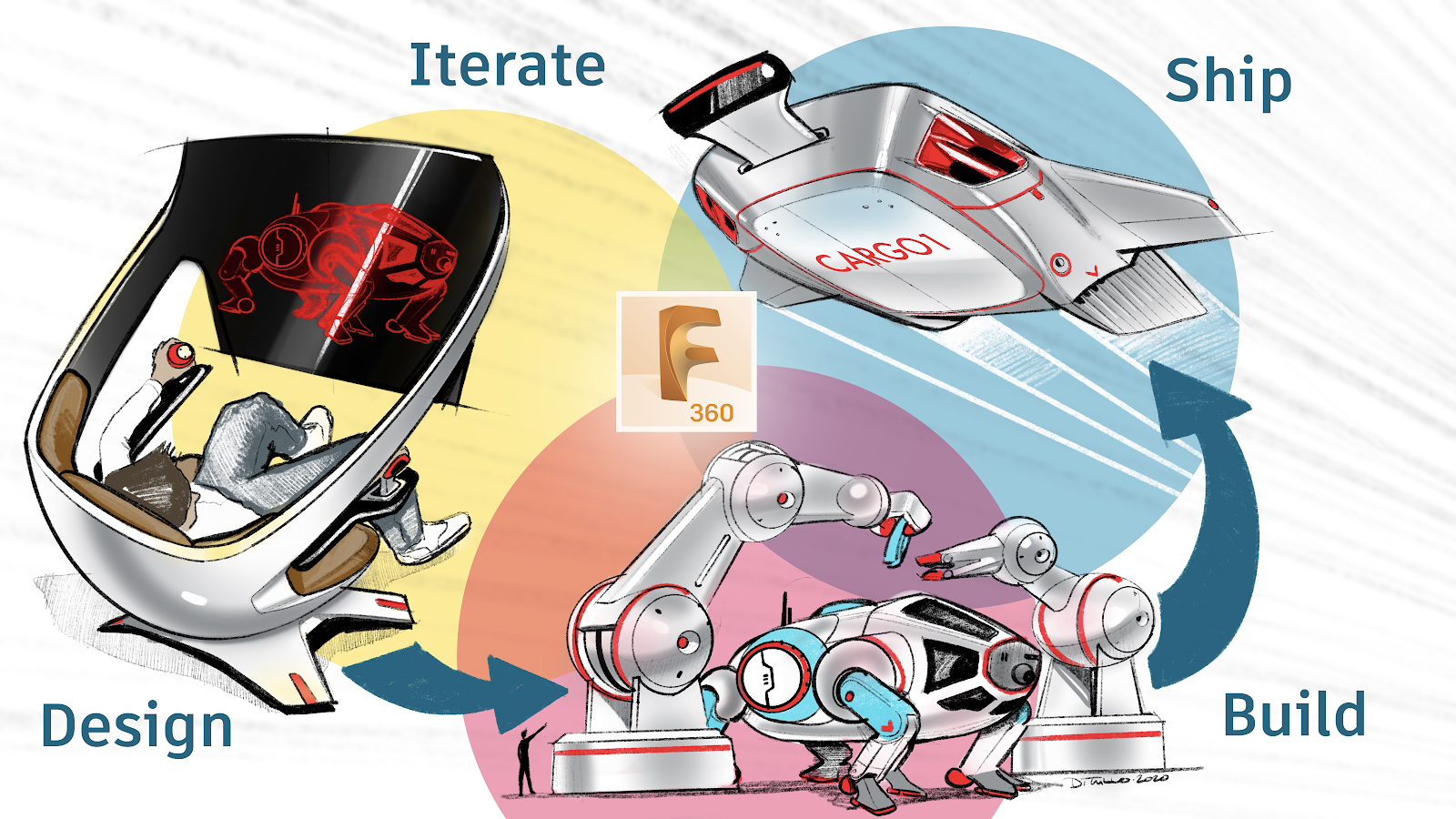
Illustration by Michael Ditullo, industrial designer, science fiction fan, and Fusion 360 user
Science fiction predicted that in the year 2020, we’d be colonizing Mars and Venus, that our brains would be permanently connected to the Internet, and that teleportation would be the advent of transportation. While many of these things still seem far from reality and technologically impossible, you can definitely see the ideas behind some of these predictions begin to take root today. How connected we are to the world through the tools we use is stronger and more relevant than ever.
Here’s what you can do now
Our vision remains true from day one: we want Fusion 360 to be the most intuitive and intelligent all-in-one solution for your product development needs, carrying your ideas from concept through manufacturing so that you’re ready for the future, today. We want to help you achieve the new possible, and together, we absolutely can. Since our October of 2019 Roadmap Update, we’ve worked towards this vision by introducing some major pieces of technology towards the end of 2019 and beginning of 2020:
[icon name=”check” class=”” unprefixed_class=””] Electronics Design enabled you to associatively design 2D electronics schematics, 2D/3D PCB, and library all within Fusion 360.
[icon name=”check” class=”” unprefixed_class=””]Advanced Simulation tools like Event Simulation and Electronics Cooling Preview give you the power to test and validate your designs for optimal impact resistance and heat dissipation.
[icon name=”check” class=”” unprefixed_class=””] Edit-in-place preview gave you the ability to finally edit referenced geometry in-place and in-context to the entire assembly design, without the need to open it up as a separate document.
[icon name=”check” class=”” unprefixed_class=””] Generative Design outcome cost estimation (powered by aPriori) makes it possible for you to compare outcomes and make design tradeoffs informed by costs.
[icon name=”check” class=”” unprefixed_class=””] Drawings improvements powered by sketch tools as well as line-weight control, move the needle by providing you the tools you need to make comprehensive production drawings.
[icon name=”check” class=”” unprefixed_class=””] Advanced manufacturing tools like Toolpath Trimming, 4-Axis rotary, and 5-Axis Steep & Shallow strategies not only save you time, but also improve the finish quality of your parts.
[icon name=”check” class=”” unprefixed_class=””] Fused Filament Fabrication opens the door to mainstream additive manufacturing capabilities, as well as hybrid additive+subtractive strategies.
Here’s what we’re working on
[toc]
With the latest product update in the books, you can see that we’ve delivered on many of the projects mentioned in the 2019 roadmap update. This year, we’re continuing down the path we laid last year as we set out to enhance Fusion 360 in three major areas:
- Mature the core functionality that already exists
- Deliver advanced capabilities in product development
- Push the boundaries of what is technologically possible
Here is the section you’ve all been waiting for: the overview of key projects we’re working on/have planned.
[icon name=”asterisk” class=”” unprefixed_class=””] Keep in mind these are not promises, and scope of these projects can change drastically at a moment’s notice. Some projects may land sooner than others based on a variety of influencing factors.
Sketching
Sketches are foundational to your mechanical designs, and having the right tools to create sketch geometry, edit geometry, dimensions, constraints, text placement, and proper inference is critical to the overall robustness of the design. Our sketch experience has come a long way over the years, and we’re continuing to deliver on more robustness, more predictability, and overall performance. Here are a number of projects we’re working on you should know about.
[expand title=”See the projects in progress”]
Sketch Text improvements
The ability to put text on a sketch and later extrude those words is a necessity in any design software. We wholeheartedly agree with you when you tell us that our Sketch > Text experience needs to be revamped, and that’s exactly what we’re doing. We’re working on a new experience that’ll be more intuitive to place, resize, and control how your text looks in a sketch. Put Sketch along a path, or put it on a circle. This project will enable all of these things to happen.
Better DXF/SVG support
We’ve heard from you that Fusion 360 needs better DWG\DXF\SVG support, and we’re definitely on the same page. Support for DXF can be challenging because of the many varied sources of DXF data. As we continue to work with you through the forums, the support teams, and one-on-one conversations, we are focusing on 3 major fronts around improving DXF/SVG behavior:
- Automated Gap Repair – DXF files often have small gaps between geometry that prevent Fusion 360 from finding closed profiles; today these gaps require manual repair. We are evaluating improvements for automatic and automated repair of these irregularities.
- Import threshold – DXF files can be large and include enormous quantities of geometry. We know there are limits to what Fusion 360 can currently handle, and are working on a better way to prevent you from getting stuck by making it work or letting you know beforehand that the import isn’t gonna go well.
- General Performance – These are improvements to the underlying framework for managing geometry, so things don’t come in broken.
3D Sketch improvements
We delivered our revamped 3D sketch experience back in March, and we’re not stopping there. This project will enable 3D sketch support for commands like Mirror, Symmetry, as well as constraint types.
Flipping and dragging/tangent handle control
While we’re working on improving 3D sketch, we’re also looking at improving the performance and predictability of how geometry behaves when you drag tangent handles and Spline point handles.
A more flexible and predictable coordinate system
Fusion 360’s sketching experience has come a long way, and your feedback has been central to how it has evolved over time. We’ve heard that redefining sketch coordinate systems often lead to unpredictable outcomes, where geometry would flip unexpectedly. The goal of the project is to eliminate any unpredictability in redefining sketch coordinates and give you the confidence to create more robust sketches.
Chamfer tool for sketches
We’ve had the 2D Sketch > Fillet command for quite some time, and we hear you on wanting Chamfer. We’re happy to share that this is something we’re working on implementing soon, so you’ll have the ability to create Chamfers within your sketches.
[/expand]
Modeling
At the core of every design are the sketches and modeling tools used to create the design. Here are highlights of projects we are prioritizing and working on to improve the sketching and modeling experience.
[expand title=”See the projects in progress”]
Ruled Surface
Now this one has been a blocker for a lot of your workflows especially anyone creating any kind of plastic parts that need draft. We have been working hard to identify gaps in our surfacing toolsets and one of the biggest was Ruled surface. We will be giving you all the goodness of adding a ruled surface to your designs soon; utilizing either a model edge or sketch edge. Tie this in with our new 3D Sketching capabilities and the possibilities are vast.
Parting Line draft
Just like Ruled Surface, one of the tools that many of you have needed for a while is Parting Line Draft. This one tool will revolutionize workflows especially when working with plastic parts. Our current draft tool is adequate for some super simple geometry but we are still lacking in this area and need to step up our game. We will be investing more time into the Draft command and the first step is to enable you to use Parting Line Draft.
T-Spline Edit by curve
Having the ability to create a curve to edit a T-Spline makes it a lot easier to manipulate multiple nodes in a T-Spline and makes sure that the final shape is more like the design intent. We will be bringing this functionality to you soon, making T-Splines easier and more flexible to manipulate.
Emboss
This one feature has been such a source of pain for a lot of your workflows and has been one of the most requested features in the Forum, our former IdeaStation, Feedback Hub, and face-to-face conversations. We are making sure that we have the right solution for you and are taking the time to make sure some of the required backend work was implemented before building out Emboss.
Mirror Combine / Stitch
We always want to help you be more productive with Fusion 360’s toolsets, and one way to do this is to reduce the number of steps you have to take to get the results you want in your designs. It can be a real pain having to mirror a body or bodies and then having to do either a Combine or Stitch. We are adding the ability to do this all in one command instead of multiple commands.
Parameter naming during creation and edit
Just like the Mirror Combine / Stitch enhancement, this is a workflow enhancement that makes using parameters that much easier. Currently you have to define the naming of parameters within the parameters dialog, and constantly opening the dialog to create parameters can become unnecessarily tedious. We are simplifying this approach so you can define the names of parameters during creation and edit while you are creating sketches or features.
Augmented reality viewing with USDZ
Augmented Reality (AR) is all the rage these days, and has some real practical applications in the product development lifecycle. We wanted to give the community a way to start the journey around AR for design reviews. As a simple first step, we’re adding an USDZ as an exportable format to Fusion 360. USDZ is an AR file format developed by Apple and is quickly becoming the standard format for AR applications across the industry. This will allow you to create an AR experience on an Apple device. We are looking at other ways we can add AR experiences to Fusion 360 and are interested to hear how you envision yourselves using AR in your design process.
T-Spline Parametric match Edge
You read it right! We are working on giving you the ability to create a relationship between a BREP body / edge and a T Spline body / edge. Why is this important? Because this will allow you to create a BREP surface / body and make sure that if the BREP body moves or changes, then the T-Splines body created from the edge of that BREP body updates automatically.
Fixing 2 Distance + Distance Angle chamfer
This has been a hot topic for a while and in dire need of fixing. Today you cannot flip the dimensions for the above chamfer options, making it frustrating to get the right geometry. To be able to achieve the correct Chamfer, you had to either do a sweep or various work-arounds to get to the final correct chamfer shape. We are adding this fix to this year’s list of projects so we can finally get round to fixing it.
Full Round Fillet
We’ve been hearing that we can’t achieve a proper full-round fillet on geometry; the only way to achieve this is with a very deft touch while dragging a size manipulator or by getting a dimension close to half the thickness of the geometry you’re trying to apply a Full Round Fillet to (and even that it’s not perfect). The good news is that we’re working on giving you the ability to do this without cumbersome work-arounds.
Parametric Mesh
The idea is to be able to not only repair and work with mesh files more effectively, but also to enable you to modify, light-weight and even convert mesh bodies to freeform and solid bodies in a parametric modeling environment. This is obviously no easy task but we are working hard on getting all the pieces in place so that we can get this technology into your hands as soon as possible.
[/expand]
Electronics Design
As consumer products become more technologically advanced, so do the electronics that make it all possible. We introduced Electronics Design back in January to demonstrate what it really means to have a complete product development platform all within a single user experience. Here are projects we’re working on to evolve the Electronics Design workflow.
[expand title=”See the projects in progress”]
Derive 3D PCB from Sketch
We introduced the concept of Derive in 2018 for more flexible modeling workflows, and now we’re working on making it possible for 3D PCBs. This project will enable you to derive a 3D PCB from a sketch. The boundary of the selected sketch profiles will be used to create the board outline. If the source sketch is updated, the board outline can be updated too because there is association between the outline and the source sketch. This is the major difference between Derive 3D PCB and the existing “Create 3D PCB” command.
Non XYZ Plane Support
Currently, creating construction planes in the 3D PCB environment for additional geometry is limited since you are only able to create sketch planes parallel to the XY planes. This project will enable you to create arbitrary sketch planes when creating 3D PCB using the Derive command.
Edit-in-Place for 3D PCB
When integrating a 3D PCB into a mechanical design as an external reference, you might want to adjust the position of some 3d packages based on the shape of the enclosure. This will be achieved by enabling Edit-in-Place.
Part list Support
Just like in drawings, part lists are equally important in Electronics design. We’re working on giving you the ability to generate part lists, add to them, edit them, and establish a link to the design library.
Spline and True, Solid Polygon Support
PCB boards come in all different shapes and sizes, and depending on the application, they require very custom shapes. Luckily we have the Spline tool in Fusion 360 that lets you create flexible splines, and we’ve tapped into this tool for Electronics Design. We’re working on expanding Spline tool’s capabilities with full Spline support so that you can create any board outline and retain shape fidelity.
Fusion 360 3D PCB Part Models
With Electronics Cooling currently in preview, we are working on giving you the ability to assign default material properties to your existing 3D model assets (created with our package generator) which are public under Eagle PCB/Fusion Electronics Managed folder. This will give you more accuracy in solving Electronics cooling simulation studies.
Component Library Expansion
The electronic components CAD library provides the building blocks of a PCB design, and we’re adding more components and more categories like Embedded – FPGAs, Micro-controllers, Relays, and Connectors.
More Quick Route Tools
Back in April, we introduced QuickRoute Guided tool, enabling you to route the airwires between multiple pads of devices in 2D PCB, by defining a guided drawing path. We’re working on adding additional functionality to the QuickRoute workflow with Aireware, Signal, and Multi with the ability to target multiple layers.
Tighter Library Integration
We are working on a number of fronts here to improve the integration between Library.io and Fusion Team, Fusion 360 and EAGLE. This will enable you to consume libraries, including 3D Packages made entirely in Fusion 360.
Better User Experience
In addition to maturing the feature set, we recognize that user experience is also a critical part of evolving this space. We’re working on enabling the ability to use the library across multiple machines, improving the usability of the add dialog and Library Manager, as well as the layer & colors experience in the PCB and Schematic editors.
[/expand]
Generative Design
When it comes to generative design, Fusion 360 has been at the forefront of the latest technologies and workflows, and we’re continuing to blaze the trail with enhancements to existing tools as well as making it more accessible for you to get fully editable outcome geometry to use in your product development process.
[expand title=”See the projects in progress”]
Generative Design Extension
You told us that the cost associated with learning and using generative design was a bit too unpredictable, and that it was a barrier to jump in and hit the ground running. Based on your feedback, we’ve been working hard to develop an extension offering that will allow you to subscribe to generative design on a monthly or annual basis. During that time, you will be able to have unlimited usage, removing any uncertainty about how much investment will be required for success.
Connection to Ansys Discovery
At the beginning of 2020, we announced and delivered a direct path from Fusion 360 to Ansys Mechanical 2020 R1 for validating generative design outcomes, fully setup and ready to run. We will be extending our partnership with Ansys to provide this same workflow for Ansys Discovery 2020 R2.
Additive Manufacturing Constraint Improvements
You also told us that our additive manufacturing constraints were not meeting your expectations as it relates to shape quality and editability. We hear you and we are remedying this by improving the way the solver enforces the overhang angles you define to reduce the amount of stair stepping that is present in many outcomes where the shape is not well oriented with respect to the default global print directions. These stair-step patterns were not ideal for manufacturing, nor are they easy to edit away. Additionally, we are investigating how to consider more optimal print orientations with the shape generation to provide you the best shape possible.
New Solver Platform
The foundation of Generative Design is our solver platform. We have been making significant strides in this area to enable a number of improvements:
- Improved time to solution
- Improved shape quality
- Improved handling of design spaces with thin geometry
- A foundation for more robust manufacturing constraints
- A foundation for additional physics and functionality
Symmetry
One of the first deliveries that will come as part of our New Solver Platform project will be the ability to enforce symmetry. Many of you have asked why symmetric design spaces with symmetric loads and constraints did not generate perfectly symmetric designs. While it might be valid for symmetric inputs to create non-symmetric outputs, we totally get how disconcerting and annoying it can be when it’s not meeting your expectations, so we have been working on making sure we can provide symmetric outcomes. We will also carry the definition of symmetry into the outcome and provide symmetric edit-ability, as well.
Fluid Flow
Yeah, we’re not just stopping at physical geometry with Generative Design. Another project enabled by our New Solver Platform project is adding a new physics type to allow for the generation of internal fluid flow channels/volumes. Following our existing generative paradigms, we will allow users to define flow inlets and outlets, designate obstructions as well as seed flow channels and then generate designs that minimize the pressure drop. You can also expect fully editable outcomes, just like we produce today for mechanical studies.
Assembly Context Loads and Constraints
One of the more challenging parts of working with generative design is knowing how to apply loads and constraints, especially when the part you are working on is in the context of a larger assembly. The loads and constraints that act on the component of interest may not always be obvious based on what you know about how the larger design works. We want to provide you with the ability to apply loads and constraints to the assembly where you know them and then let generative design figure out the rest.
Recommendation Engine
The ultimate goal of generative design is to provide you with a better design to solve your engineering challenges. If you are using the technology to its fullest exploration potential, you likely have more than just a few outcomes to consider. While we have a number of tools in the Explore environment to help you filter and find the most interesting outcome, we thought we could take this a step further and start to provide recommendations on which outcomes might most likely meet your requirements.
Design Outcome ‘Favorites’
As you are reviewing outcomes, you’ll find that some iterations are more interesting than others. You’ll want to remember those iterations and come back to it so you can dig deeper via the Explore environment for cost data as well as how they compare against each other. We’re going to provide a way to mark iterations as a ‘favorite’ so that they can be used in all of the Explore workflows, making it easier for you to nail down which iteration should become a full fledged outcome.
[/expand]
Drawings
We recently introduced the ability to create sketch geometry, control line weights, as well as access document and sheet settings in a more consistent experience. With the backend newly re-architected, here are some projects we want to get through so that we can make you more productive.
[expand title=”See the projects in progress”]
Switch Linear Dimension Units (mm/in)
Historically, drawing units have been defined during creation and inflexible thereafter. This long-requested option to toggle document settings between mm and inch units will be a huge time saver for those cases where a mistake is caught after drawing creation, or for those of you with clients with differing requirements.
Better Move Handling
This one is simple but will be game-changing! We’ve heard from many of you that interactions in the Drawings workspace simply ‘feel different’ from the rest of Fusion 360; you’re not wrong. The team’s done a great job rewiring our architecture so that we can better handle click-and-drag, for a much more intuitive and pleasant experience when moving views, text, and now sketches around a sheet.
Rename Views
We’re excited to bring you more flexibility by enabling view renaming for section and detail views. Gone will be the days of using clumsy workarounds or being forced to restart in order to change view names after reordering – a new Name field in the Drawing View dialog allows for quick changes from the default when placing a view, or when editing afterwards.
All-Level Parts Lists
We’re getting close to wrapping up support for all-level parts lists in drawings and Smart Templates, so that you can document both parent components and subcomponents in the same BOM. Per – level renumbering will provide for that extra level of control.
Section View Depth Control
We’re upgrading our Section View command to give you control over the cut distance – rather than cutting through the entire part, you’ll have the option to input a distance or drag a slider in order to define the desired extent of the cross-section and reduce the appearance of unwanted geometry.
Multi-Leader Leaders
Another small improvement that will go a long way towards rounding out your drawings toolset – multi-leader support will let you create multiple leaders on any leader object (balloon notes, bend notes, etc.). This is huge for hierarchical callouts, allowing you to declutter your drawing with a single note referencing part multiples.
Hole & Thread Notes
We know, we know – it’s about time we get this crucial piece of the drawing tool set into the product, and are hard at work laying the groundwork to make it possible. We’re excited to get Hole & Thread notes out the door this year
Weld Symbols
Similarly, this addition speaks for itself. While the newly-added sketch tools will provide an interim workaround for many of you, we know proper welding symbols are a must-have, and are partnering with the AutoCAD Mechanical team to get these sorted out and into your hands.
Broken Views
This a big, multi-month project that is a bit further out on the horizon – but we wanted to let you know that Broken Views are a priority, and on their way. You’ll be able to ‘break’ long parts and dimension the gap between them while keeping it to scale, saving room on your drawing canvas.
For more insights on where we’re taking Drawings, check out the dedicated Drawings roadmap page.
[/expand]
Manufacture
Over the past few updates, you many have noticed the Manufacturing workspace expand in terms of functionality with new capabilities like surface inspection, Steep & Shallow milling & rotary milling. A trained eye may have noticed these technologies came from our other CAM solutions. At the same time, we have focused on delivering on the details in areas like better error messages and improved turning tool-paths. As we look to the future, you can expect us to continue on this trend of both expanding the solution capabilities while reinforcing the fundamentals.
[expand title=”See the projects in progress”]
Tool Library
Many of you may have already turned on the preview of the updated tool library and have already provided feedback, thank you! At its core, the new tool library fundamentally changes the way you can think about how your libraries of tools with the extension of cutting presets, enable you to capture how to drive a tool in specific cutting conditions. While not as obvious, the architecture of this new library is being built in a way that will enable deep levels of API interactions between external systems and tools in Fusion 360. In addition, this new framework sets us up to provide an experience to interact with tools outside of the traditional Fusion 360 desktop experience.
In-Process Stock
Fusion 360 has also presented a backplot of toolpaths in canvas when an operation is selected. However, this backplot does not always clearly communicate the result of the operation. Not only will In-Process stock give an instant preview of the resulting stock from an operation, it also streamlines the process of simulating an operation in the middle of a setup.
Intelligent Invalidations
The power of an integrated CAD/CAM system is both giving CNC programmers access to best-in-class modeling tools in a consistent interface and providing associativity to toolpaths when model changes take place. However, we’ve all experienced the frustration of simple model changes invalidating entire manufacturing documents. That’s why we are determined to reduce the number of in-validations while continuing to provide the highest level of confidence that model changes will result in updated toolpaths where appropriate.
Template Library
One of the best kept secrets of Fusion 360’s manufacturing capabilities has always been the ability to capture manufacturing intelligence in templates. However, templates were limited to flat lists and not discoverable. Following the same User experience as other libraries across Fusion, we’re working on improving the template library to give you the options to store and reuse Manufacturing intelligence.
Tool Orientation adjustments
When doing positional 5 Axis machining (3+2) Fusion 360 provides amazingly intuitive options to selected faces to define orientations. However, when users need to make adjustments to these fixed orientations they resort to creating additional geometry. Leveraging the GUI elements of the move command, the team is working on allowing for associative adjustments to tool orientation.
Toolpath Modification
In addition to the recently released Toolpath Trimming feature, we are working on a feature that will enable you to simply select undesirable toolpath cutting moves and delete them. We plan to allow Toolpath Trimming to trim with a fully associative curve in addition to the current option of a sketched boundary.
Rest finish milling strategy
A Rest finish milling strategy is being developed which is designed to efficiently machine residual stock remaining from the previous operations. This has similarities to the existing Pencil strategy but some of the key differences are: Optionally machine steep areas across the corner and shallow areas along the corner, The same 5 axis capabilities currently supported by the Steep and Shallow milling strategy.
5 Axis for all 3D strategies
The introduction of Steep and Shallow brought with it new 5 axis controls from PowerMill. However, these same levels of control are currently not available for other strategies. We are working towards making all appropriate milling strategies 5 axis capable. For example, strategies such as Parallel, Ramp, Scallop, Pencil, Spiral etc. will have a similar 5 axis capability to the recently introduced Steep and Shallow strategy.
Toolpath Smoothing
The Steep and Shallow milling strategy has a smoothing option called “Evenly Spaced Points”. We plan to enable this feature for all milling strategies. This style of smoothing enables modern machine controls to more closely achieve the programmed feedrate. Modern machines will generally move faster and more smoothly with this option set, reducing cycle time whilst achieving a superior surface finish on the machined part.
NC Programs as the primary workflow
Several months back we released a new way of creating output code called “NC Programs” allowing users to among other things visualize how multiple setups are woven together. Over the course of the year to come, you will see this workflow be promoted to the primary way of creating output NC code with additions like storing NC programs directly to Fusion team and notification for posting errors in product,; no more digging through posted text files to determine posting errors!
Arrange in Nesting
In addition to the Nesting functionality, we’re developing a new Arrange tool that enables efficient object arrangement within a specified rectangular or non-rectangular bounding area. The results will support associative arrangement updates with any design and/or bounding area changes. Additionally, arranged results will get saved to the timeline allowing changes to replay in sequence as the history marker is moved backwards or forwards. We have made significant progress on Arrange and are hoping to make it available in Preview very soon.
[/expand]
Additive
3D printing has come a long way and is not just a fad; it is here to stay as a manufacturing process and we’re giving you the tools you need to succeed. Here are a few projects we’re investing in on the additive manufacturing front.
[expand title=”See the projects in progress”]
Fused Filament Fabrication (FFF) Improvements
After the March 2020 update, Fusion 360 became a slicer for FFF printers overnight. As awesome as this release was for FFF, it had a couple of kinks. The team has, since then, been working hard at improving the usability and fixing any and all reported issues. You can expect to see a continued investment in this area. We are adding new printers, new post files and new functionality update after update. Some of the key projects that excites us are around G2/G3 support, new infill types, dual extrusion improvements and overall increased performance around toolpath generation.
Stereolithography (SLA) / Digital light projector (DLP) 3D Printing
FFF and metal powder bed fusion printers are great and all, but 3D printer processes are very diverse, and we want Fusion 360 to support all kinds of printing techniques. We are working on enabling SLA and DLP print preparation such as integrating printer workspaces, SLA/DLP specific support generation methods, packing parts within the platform, and slicing models for these types of printers. We can’t wait to see what you design and print using Fusion 360.
[/expand]
Collaboration & Data Management
Data management is the backbone of a well oiled product development lifecycle, and is what makes Fusion 360 unique. A common theme in most of the feedback we see around data management in Fusion 360 is about control and it is a big area of focus for us this year, especially with so many customers collaborating remotely as they work from home.
[expand title=”See the projects in progress”]
Folder Permissions
This is probably the number one most requested item in Data and we are excited to be working on the ability to invite and collaborate with team members on folders and not just at the top level project. Additionally we are introducing a few new roles beyond just Admin, Editor and Read Only, so that you can give all your collaborators the right level of access.
Extended Properties and New Properties Panel
We are be extending the number of properties that are available out-of-the-box, and they can be displayed in a new modeless (resizable) Properties panel. You can select components in the browser tree or on screen, and the values will change to reflect the selection. This will enable quicker viewing and editing of properties within Fusion 360.
Item Numbering
A common need in any company is applying a unique identifier to parts, assemblies and drawings. This process can fall into the spectrum from very manual, with users creating spreadsheets to manage part numbers, to automated with ERP integrations. Fusion 360 will add the ability to create unique item identifiers based on a predefined scheme.
Release & Revisioning
Continuing the theme of control, a long-standing request has been for the ability to have some gated workflows like Release to drive the revision and state of a design or drawing to clearly communicate intent with the rest of the team.
Change Orders and Workflow
One of the important aspects of control is accountability. With the introduction of change orders, you will be able to submit changes via an approval process with multiple approvers. Once the workflow is complete, the change is completed, there will be a full record of the transaction.
Consistent Data Experience
Over the years we have seen feedback on the data panel in Fusion 360 around the density of data presented in it and how it has a more limited toolset compared to the web Data management interface of Fusion Team. We are unifying these experiences so that all the capabilities of the data platform are available to you within Fusion 360, no matter which interface you use. Notice the data management “Home” tab integrated within Fusion 360.
Better Awareness of who’s working on what
As distributed teams work on larger Fusion 360 projects, it’s become clear that we need more explicit indicators of collaborators working in the same design at the same time. This much improved workflow will make it explicitly clear who is working on what in your Fusion 360 project.
Implicit Reservation
But wait, there’s more! Fusion 360 designs will be implicitly reserved to the person editing the item on the first edit command and this user will maintain exclusive access to the item until they save. In case of a part or drawing, this means that other users can open the Fusion 360 item but they will be read only till you are done. In the case of an assembly, it’s even better because the new Edit in Place command will actually allow multiple users to edit different subcomponents of an assembly even if some parts of the assembly are reserved to someone else.
[/expand]
Usability
As we mature as a product, we also have to make sure that Fusion 360 remains intuitive, easy to use, and has the room to scale. When we say ‘scale’, we mean it in an experiential as well as a physical way:
- Experiential in the sense that new technologies being added must feel inherently Fusion 360, easy to learn and rewarding to master.
- Physical in the sense that Fusion 360 as a software must be adaptable with more and more monitors running simultaneously in different working environments, and with higher and higher screen resolutions.
[expand title=”See the projects in progress”]
More language support
You’ve asked for additional language support, and we listened. Coming soon to Fusion 360 is French and Italian, joining the current list of languages available in Fusion 360 (English, Japanese, Chinese, and German). As some of you may not know, supporting a language doesn’t just mean translating the software appropriately, it also includes making sure that we have the right resources to support the community around it. We are working on other language support as well, and will keep you informed of the upcoming languages to support.
Flexibility for consuming Extensions
Based on your feedback, we added the Manufacturing Extension to Fusion 360 last year. By working with you and hearing you out, we are going to increase the flexibility on how these extensions can be consumed. This project will give you the flexibility to get future Extension functionality based on a daily, monthly, or annual basis, as well as select between cloud credits or credit card as your preferred method of payment.
Consistent notifications
The speed at which we’re developing Fusion 360 resulted in the unintentional introduction of a number of different notification behaviors throughout the years. You’ve seen everything ranging from banners, to fly-outs, to sticky and temporary toasts. We’re now working on cleaning this up, grouping similar category messages together, and showing them in a more consistent manner. As we’re working through this project, we’d also love to hear your feedback.
See Feedback Hub
Enhanced in-product learning
Many of you might have noticed the Learning Panel, which can be opened/closed from the Help drop-down. It currently suggests tips based on the actions you are doing inside Fusion 360. It has also become a great set up guide on the Generative Design workspace. We are about to offer additional options for help within this panel. For example, have extra information about current commands in use, and also trigger it when you click a shortcut from a tooltip. The whole point is to keep you in context inside the product as much as possible, instead of having to navigate into our web-based help documentation.
Better in-product support
A small cohort of commercial users has already been exposed to an in-product chat that lets them contact an expert that can answer any question regarding the usage of Fusion 360, or schedule time with an expert in any specific field if they can’t help in real time. We will be scaling access to chat for more commercial users in the upcoming months. User feedback from these chats is overwhelmingly positive, so we are very excited to extend it to a larger audience as soon as possible.
[/expand]
[icon name=”thumbs-up” class=”” unprefixed_class=””] We hope you are as excited about what’s coming as much as we are! As always, let’s chat in the comment section below; we would love to hear your thoughts!
_
NOTE:
- Roadmaps are plans, not promises. We’re as excited as you to see new functionality make it into the products, but the development, releases, and timing of any features or functionality remains at our sole discretion.
- The projects mentioned in this roadmap are highlights, and do not account for on-going efforts like bug fixes, platform and service maintenance.
- These roadmap updates should not be used to make purchasing decisions.