
Elevate your design and manufacturing processes with Autodesk Fusion
Power Hour: Do You Need a Linear Regulated or Switching Power Supply for Your Next Electronics Project?
Everyday electronic devices, especially those with integrated circuits, require a reliable DC voltage source that can supply powers at all times without any hiccups. In this blog, we’ll be looking at two power supply design topologies to consider for your next project, linear regulated and switching power supplies. The power supply that you choose ultimately comes down to your requirements for efficiency, space, output regulation, transient response time, and cost.
Linear Regulated Power Supply
Linear regulators were the power supplies of choice until the 1970s for converting alternating current (AC) into a steady direct current (DC) for electronic devices. While this power supply type isn’t used as prevalently today, it’s still the best choice for applications that require minimal noise and ripple.

How They Work
The main component that allows a linear regulator to function is a steel or iron transformer. This transformer provides two functions:
- It acts as a barrier to separate high voltage AC input from low voltage DC input, which also filters out any noise getting into the output voltage.
- It reduces AC input from 115V/230V to approximately 30V which can then be converted to a steady DC voltage.
AC voltage is first lowered by the transformer and then rectified by several diodes. It’s then smoothed into a low DC voltage by a pair of large electrolytic capacitors. This low DC voltage is then regulated as a steady output voltage with the use of a transistor or integrated circuit.

The voltage regulator in a linear power supply acts as a variable resistor. This allows the output resistance value to change to match output power requirements. Because the voltage regulator is constantly resisting current to maintain a voltage, it also acts as a power dissipating device. This means that useful power is constantly being lost in the form of heat to keep the voltage level constant.
The transformer is already a large component to have on a printed circuit board (PCB). Because of the constant power and heat dissipation, a linear regulator power supply will require a heatsink. These two components alone add to a very heavy and bulky device when compared to the small form factor of a switching power supply.
Preferred Applications
Linear regulators are known for their poor efficiency and large size, but they do provide a noise-free output voltage. This makes them ideal for any device that requires high-frequency and low-noise, such as:
- Control circuits
- Low noise amplifiers
- Signal processors
- Automated & laboratory test equipment
- Data acquisition sensors & circuits
Advantages & Disadvantages
Linear regulated power supplies might be bulky and inefficient, but their low noise is ideal for noise-sensitive applications. Some advantages and disadvantages to consider for this topology include:
Advantages
- Simple application. Linear regulators can be implemented as an entire package and added to a circuit with only two additional filter capacitors. This makes them easy for engineers of any skill level to plan and design from scratch.
- Low cost. If your device requires a power output of less than 10W, then the component and manufacturing costs are much lower when compared to switching power supplies.
- Low noise/ripple. Linear regulators have a very low output voltage ripple and high bandwidth. This makes them ideal for any noise-sensitive applications including communication and radio devices.
Disadvantages
- Limited flexibility. Linear regulators can only be used to step down voltage. For an AC-DC power supply, a transformer with rectification and filtering will need to be placed before the linear power supply which will add to overall costs and effort.
- Limited outputs. Linear regulated power supplies only provide one output voltage. If you need more, then you’ll need to add a separate linear voltage regulator per required output.
- Poor efficiency. The average linear regulated device achieves an efficiency between 30%-60% due to heat dissipation. It also requires the addition of a heat sink which adds to the size and weight of the device.
In this day of energy efficient devices, the poor efficiency rating of a linear regulated power supply can be a deal killer. A normal linear regulated power supply will operate at about 60% efficiency for a 24V output. When you consider a 100W input, you’re looking at 40W of lost power.
Before considering using a linear regulated power supply, we highly recommend considering the power loss that you’ll get from input to output. You can quickly estimate the efficiency of a linear regulator with the following formula:

Switch Mode Power Supply (SMPS)
Switching power supplies were introduced in the 1970s and quickly became the most popular way to supply DC power to electronic devices. What makes them so great? When compared with linear regulators their high efficiency and performance stand out.

How They Work
A switch mode power supply regulates an output voltage with pulse width modulation (PWM). This process creates high-frequency noise but it provides a high-efficiency rating in a small form factor. When plugged into an AC mains, 115V or 230VAC is first rectified and smoothed by a set of diodes and capacitors, which provides high voltage DC. This high DC voltage is then lowered using a small ferrite transformer and set of transistors. The step-down process still retains a high switching frequency between 200kHz to 500kHz.
The low DC voltage is finally converted into a steady DC output with another set of diodes, capacitors, and inductors. Any regulation required to keep the output voltage consistent is handled by adjusting the pulse width of the high-frequency waveform. This regulation process works through a feedback circuit that constantly monitors the output voltage and controls the on-off ratio of a PWM signal as needed.
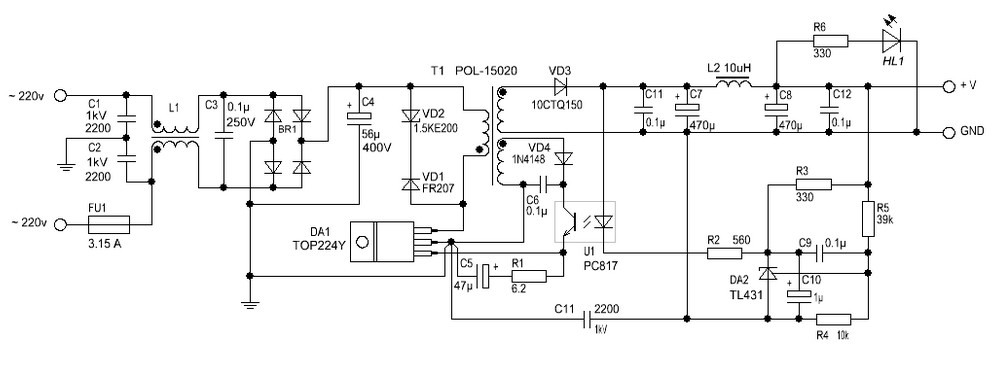
Preferred Applications
You’ll most often find switching power supplies used in applications where battery life and temperatures are important, such as:
- Electrolysis, waste treatment, or fuel cell applications
- DC motors, slot cars, aviation, and marine applications
- R&D, manufacturing, and testing equipment
- Battery charging for Lithium-Ion batteries used in aviation and vehicles
- Electroplating, anodizing, and electroforming processes
Advantages & Disadvantages
Switching power supplies might have a higher efficiency than linear regulators, but their noise makes them a poor choice for radio and communication applications. Some advantages and disadvantages to consider for this topology include:
Advantages
- Small form factor. The step-down transformer in an SMPS operates at a high frequency which in turn reduces its volume and weight. This allows a switching power supply to enjoy a much smaller form factor than linear regulators.
- High efficiency. Voltage regulation in a switching power supply is made without dissipating excessive amounts of heat. SMPS efficiency can be as high as 85%-90%.
- Flexible applications. Additional windings can be added to a switching power supply to provide more than one output voltage. A transformer-isolated SMPS can also provide output voltages that are independent of input voltages.
Disadvantages
- Complicated design. Compared to linear regulators, planning and designing a switching power supply is typically reserved for power specialists. This is not the best power supply to choose if you plan to design your own without careful study or experience.
- High-frequency noise. The switching operation of the MOSFET within a switching power supply provides high-frequency noise in the output voltage. This often requires the use of RF shielding and EMI filters in noise-sensitive devices.
- Higher cost. For lower power outputs of 10W or less, it’s cheaper to use a linear regulated power supply.
Switch power supplies are here to stay and are the power supply of choice for applications that aren’t noise sensitive. This includes devices such as mobile phone chargers, DC motors, and more.
Linear Regulator vs. SMPS Compared
We’re now going to look at a final comparison between linear regulated and switching power supplies when compared side-by-side. Some of the most important requirements you need to consider, including size/weight, input voltage range, efficiency rating, and noise level among other factors. Here’s how it breaks down:
How to Design Your OwnIt’s beyond the scope of this blog to explain how to design a linear regulated or switch mode power supply. However, there are several guides available that we would like to share. Keep in mind that SMPS design requires a high level of complexity and is not recommended for an electronics design beginner.Linear regulated power supply design guides
- John Errington’s tutorial on power supply design
- University of Nevada, Las Vegas linear power supply design
- Instructables regulated linear DC power supply design
Switch mode power supply design guides
- 7 critical steps in switching power supply design
- ON Semi switch-mode power supply reference manual
- Electronics Tutorials switch mode power supply
Power OnMost electronic devices these days need to convert AC mains into a steady DC voltage output. There are two topologies to consider for this goal, linear regulated and switch mode power supplies. Linear regulated is ideal for applications that require low noise, whereas switching power supplies are better suited for handheld devices where battery life and efficiency is important. When deciding what topology to choose, always consider your required efficiency rating, form factor, output regulation, and noise requirements. Ready to design your first linear regulated or switch mode power supply? Try Autodesk EAGLE for free today!
Linear Regulated Power Supplies | Switch Mode Power Supplies | |
Size | 50W linear power supply typically 3 x 5 x 5.5” | 50W switching power supply typically 3 x 5 x 1” |
Weight | 50W linear power supply – 4lbs | 50W switching power supply – 0.62lbs |
Input voltage range | 105 – 125 VAC and/or
210 – 250 VAC | 90 – 132 VAC or 180 – 264 VAC without PFC
90 – 264 VAC with PFC |
Efficiency | Typically 40%-60% | Typically 70%-85% |
EMI | Low | High |
Leakage | Low | High |
Circuit Design | Moderate complexity, can be designed with guides | High complexity, requires specialty knowledge |
Load Regulation | 0.005% to 0.2% | 0.05% to 0.5% |
Line Regulation | 0.005% to 0.05% | 0.05% to 0.2% |
Part Count | Low, only requires regulator and I/O filtering | High, requires switcher, snubber, transformer, capacitors, feedback network, etc. |