
Elevate your design and manufacturing processes with Autodesk Fusion
USB connectors are everywhere these days. Learn the best practices for routing your PCB traces to your USB 2.0 connectors.

You’re most likely familiar with USB connectors since nearly all electronic devices use them for charging, powering up, or data transfer. Since streaming data has become commonplace, it’s necessary to implement techniques to speed up USB connectors’ data transfer speeds reliably. This blog will teach you the best practices for routing your PCB traces to your USB 2.0 connectors.

Before we begin providing details on routing, I’d like to give you an overview of USB pinouts. As mentioned earlier, USB devices are for data transfer. They are also for battery-charging electronic devices: mobile phones, players, laptops, tablets, and other gadgets.
Creating a high-quality USB connection requires knowledge of USB Standards, the ability to read diagrams, and guidance on the type of connections. Knowing the wires’ classification, colors, and purpose is necessary. Trouble-free long cable operation is ensured by correct wiring. USB 2.0 connector pins type A and B
This cable is commonly found connecting computers to printers and scanners. The colors of the wires found in this cable are:
- +5V ( red VBUS ), voltage 5 V, maximum current 0.5 A, intended for power supply;
- D- (white) Data-;
- D+ ( green ) Data+;
- GND ( black ), voltage 0 V, used for grounding.
mini-USB and micro-USB:
These cables have smaller connectors and connect to cell phones and other devices that do not have the space for larger USB connectors. The colors found on these connectors are:
- VBUS red (+), voltage 5 V, amperage 0.5 A.
- White (-), D-.
- Green (+), D+.
- ID – for type A abbreviated to GND, to keep OTG function and for type B not connected.
- The black GND voltage, 0V, is used for grounding.
Most cables have a Shield cable; it has no insulation and is used as a shield. It is not labeled and is not assigned a number. A universal bus has two types of connectors. They are marked with an M for (male) and F (female).
USB 3.0 pinout types A and B
Version 3.0 of the bus has a ten or 9-wire connection. Pin 9 is used for the Shield wire, which is missing. Pin assignment is such that it allows for older devices to be connected.
USB 3.0 pin assignment
The plug;
- The pins that correspond to the 2.0 specification pin-out have the same color scheme;
- pins for data transmission via the SUPER_SPEED protocol, marked SS_TX- and SS_TX+ respectively;
- GND;
- Pins for receiving data through the SUPER_SPEED protocol, identified as SS_RX- and SS_RX+.
What is USB 2.0?
USB 2.0 is also a high-speed USB. In April 2000, it was released and is supported by nearly all USB-compatible devices.
USB 2.0 devices have a maximum data transfer rate of 480Mbps, higher than USB 1.1.
The USB 2.0 standard supports the Mini-A, Mini-B, and Mini-AB connectors.
What are the advantages of USB 2.0?
- Speed
- You can get 480 Mbit/s of bandwidth with USB 2.0, which equates to a 40 MB/s effective image data rate. This is sufficient performance to run many cameras at standard resolution or greater on a single computer and inspect multiple components per second.
- Modern Device
- The technology offers you a hot plug / hot unplug: You can connect and detect devices during operation.
- Power Usage
- USB 2.0 can provide up to 500 mA of current.
- Max Cable length
- A USB 2.0 cable typically has a maximum length of five meters to ensure you ease and the best results.
- Price
- Your USB 2.0 is generally less expensive than all other USB versions.
- More bandwidth
- Data transmission is possible in both ways with USB 2.0. You can use the camera’s control, triggering, and parameterization options during operation.
What is PCB board routing?
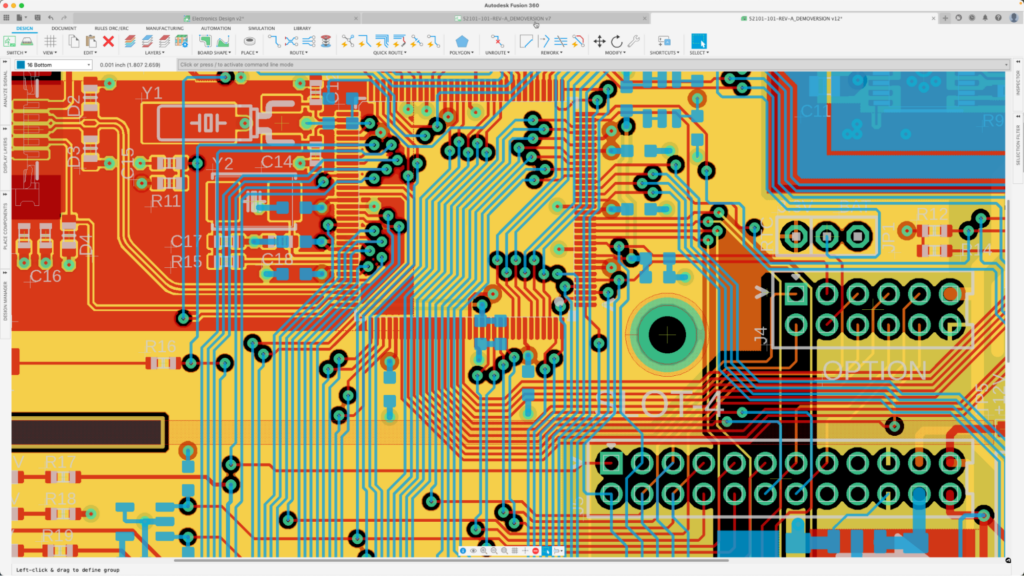
Many believe that routing PCB traces on a PCB design is easy. Routing a board for low-speed signals is considered a relatively straightforward process, but this couldn’t be further from the truth for high-speed USB signals.
In the past, when low-speed TTL DIP components were used on simple boards, that might have been accurate. Today’s designs are much more complex and need to meet specific routing criteria for the component to be operational. A PCB’s traces may require detailed design specifications to be met while routing o ensure signal integrity. Although traces might have routing specifications, you can set up and meet the design criteria for your traces with today’s more advanced PCB routing techniques and capabilities.
The routing methods you’ll use for your board depend entirely on your routing topology and signaling standard.
Don’t worry if you’re designing a PCB for the first time and are about to begin the routing stage; we’ll show you how to do it and tell you which routing specifications your PCB needs to meet.
USB 2.0 High-Speed PCB Routing Requirements
Starting PCB Routing
All PCBs must have copper traces, which connect components on the surface or interior layers. The routing technique used in your PCB will rely on several criteria.

The following are some of the important design routing requirements you may find in low-speed and high-speed signaling standards:
- High-current boards may need wide traces or polygons due to the current carrying capacity of the traces.
- Traces may need to be spread apart to help reduce crosstalk and ensure reliability.
- Any required trace impedances will require a specific width and must be configured based on the PCB stack-up.
- The maximum allowed trace length will be based on total losses along a trace and susceptibility to crosstalk.
Your goal as a designer is to balance all these factors and choose the ones that are most important for specific connections. Although high-current DC designs require significant traces that don’t necessarily have particular impedance, you might have to route signals away from the high-current paths to minimize noise., High-speed designs depend on controlled impedance with differential pair routing rules.
Let’s look at some of the simpler boards’ routing requirements to start before moving on to more complex designs.
Simple PCB Trace Routing
If your design is not working at high speeds, it will not have width requirements to avoid crosstalk issues. You are generally free to choose a trace width that easily supports your component pins and leads if your traces only need minimal current.

These designs use trace widths between 5 and 15 mils since they are small enough to route directly into component pads. The diagram below shows a simple op-amp example with traces running between a low-speed IC, some resistors, and capacitors.
These simpler designs typically don’t have to worry about impedance, common routing topologies, or excessive currents.
Routing Rules for High-Speed PCBs
Today’s boards may require impedance-controlled trace design and routing principles to assure signal integrity, even if they only have primary MCU and low-power stages. To ensure dependability and signal integrity, designers must define the trace requirements for their connections.
- Determine how much current is needed in a specific trace because routing PCB power circuits can handle large currents.
- Determine whether specific impedances are required by reviewing your component datasheets or your signaling standard.
- If impedance control is necessary, determine the trace width required to reach your impedance target. This is done initially using calculators specifically designed for this purpose. These calculators give us essential trace spacing and differential pair spacing if needed.
Your signaling standards will determine your routing needs, including total maximum length, impedance standards, and the permitted length mismatch in differential pairs or parallel buses.
You can create design rules and classes for individual nets in your design once you’ve determined any routing requirements in your board. As you route traces, your routing tools will use these requirements to determine the trace width, which requires defining minimum or maximum trace widths in your design rules.
Impedance and Routing Topology
You must choose from several approaches to determine the impedance when you need to regulate it in your PCB layout. You can use formulas to determine the impedance in your design, or you can use an app specifically designed for this purpose. With the Fusion 360 Signal Integrity Extension, powered by Ansys, you can review the selected signal impedance of your lines and get insights on the target impedance.

In PCB design software with a built-in impedance calculator function, you can calculate impedance quickly. This kind of functionality is present in only some PCB design programs, and those with it have varying degrees of accuracy in their output. The best PCB design software will have an electromagnetic field solver that automatically analyzes the trace geometry, which is currently in the Fusion 360 Signal Integrity Extension.
These tools will show how trace width and pair spacing changes affect target impedance and use the copper height and dielectric values to influence impedance results.

Trace routing topologies specify how traces carry to and from component inputs and outputs and how they branch off one another to reach different components.
In DDR routing, for instance, a single bus branch-off is used to reach numerous design components using a fly-by topology.
SPI uses a comparable bus design, but termination is implemented at the bus’s load points. When a design calls for a single component to communicate with multiple loads through a single IO interface, other components may use point-to-point topology to get to multiple components.
Ensure you are familiar with the routing topology required by your signaling standards and whether impedance control is necessary for those traces.
PCB Design Guidelines for USB 2.0

PCB layout for high data rate transmission is quite challenging, especially given the care with which the traces must be laid. There are a few guidelines that you should use to get the layout right for any high-speed PCB layout:
- Minimal use of vias
- Yes, they are useful, but incorrect routing will result in signal reflection and attenuation.
- Length Alignment
- The two ends of a differential pair must be the same length. This ensures that the receiver can adequately smooth out the common mode noise.
- Short track length
- To reduce attenuation, try to keep traces as short as possible. Attenuation occurs because signals lose energy as they travel along a trace due to dielectric absorption.
- Distance between tracks
- To minimize crosstalk, differential signals should be at least five times the trace width away from other traces.
Consider some of these vital PCB routing guidelines:
- Keep fixed impedance traces for a particular interface or signaling protocol on the same layer.
- Reduce using transitions on RF traces and high-speed signals.
- Use uniform ground regions and avoid routing through plane splits. Aim to keep traces short and direct; only make them as long as necessary.
- When constructing larger conductors for high current routine, don’t be afraid of using polygons; they may be used to create conductors of any shape.
The design and routing of PCB stack-ups closely algin to signal integrity.
Signal integrity is mainly determined by how your plane/GND/PWR layers are arranged The easiest method to ensure your design will maintain signal integrity and minimize EMI is to place a ground plane adjacent to signal layers.
These recommendations, plus the above routing rules, should help prevent or reduce many signal integrity issues and guarantee your board will work.
Interactive routing tools are the most cutting-edge solutions that can assist you in following fundamental PCB routing rules.
In other words, using these semi-automated tools, you can specify routes for a collection of signals. The routing tools will place the traces so that they automatically follow your design guidelines.
Establishing design rules for your nets and classes of nets ensures that they automatically adhere when routing.
Advanced PCB design programs can help you stay productive as you work to complete your PCB layout and route traces around your board. Many freeware and open-source design programmers force you to do everything manually.
High-Speed USB 2.0 Trace Spacing

You can route traces in your PCB layout by pointing and clicking on different parts of the board. Your intended DRC (Design Rule Check) assigns the trace width that will be used along the route of the selected signal, eventually extending across the layout to the needed location.
As you route traces in your layout, routing tools in your PCB editor application can automatically turn corners (often at a 45° angle). As you move traces between components on the PCB, they can insert vias.
Prepare a plan for several routes before you begin routing PCB traces to make sure you use vias sparingly or need to add extra layers to complete the board.
Your PCB routing technique will depend on your PCB layout; if the PCB layout has fewer crossing nets, routing traces with fewer layer transitions would be more challenging.
Sometimes it’s necessary to begin with the most straightforward routes first because they’ll show you which ones require the most time and work to complete routing in the PCB layout.
PCB layout rules and issues for high-speed circuits
To design and route a high-speed printed circuit board, you need to follow certain design rules for optimum performance. In the following, we will consider these trends and issues:
- Trace length setting
- High-speed interfaces often require that the trace length be adjusted to synchronize the signals before being transmitted over the data lines; otherwise, the board will not operate at a maximum frequency or, worse, will not be able to operate at all.
- When adjusting the trace length, ensure you get the correct size for a given group of signals—generally, the higher the interface frequency, the higher the length-matching requirements. Therefore, you must adjust the trace length for all parallel interfaces.
- Impedance
- When routing a high-speed PCB, pay particular attention to single-ended and differential impedances (Zo and Zdiff, respectively). Other common impedance types include odd mode, common mode, and even mode.
- Using the wrong impedance will cause the signal to be reflected inside the track. In fact, this reduces the operating frequency, generates unwanted electromagnetic interference, and leads to a loss in signal quality. To avoid all this, use the correct impedance.
- Track shape
- On high-speed traces, avoid using 90-degree bends if possible; use curved traces or stick to using two angles of 45 degrees to complete your turn. A sharper angle will result in reflections and impedance changes, as well as higher uncoupled lengths in differential pairs.
PCB Routing Requirements for USB 2.0: Conclusion
Complete the routing of a PCB design can be one of the most demanding PCB-related tasks. This becomes more difficult if the board size is small and the various components are hard to find. This guide provides essential guidelines, tips, and rules to help you easily design your high-speed PCB using USB 2.0 connectors.
Ready to expand your Fusion 360 PCB capabilities? Start with a free trial of the Fusion 360 Signal Integrity Extension today.
