
Elevate your design and manufacturing processes with Autodesk Fusion
During the prototyping phase of product development, crucial decisions are made, requiring good judgment and questioning beforehand.
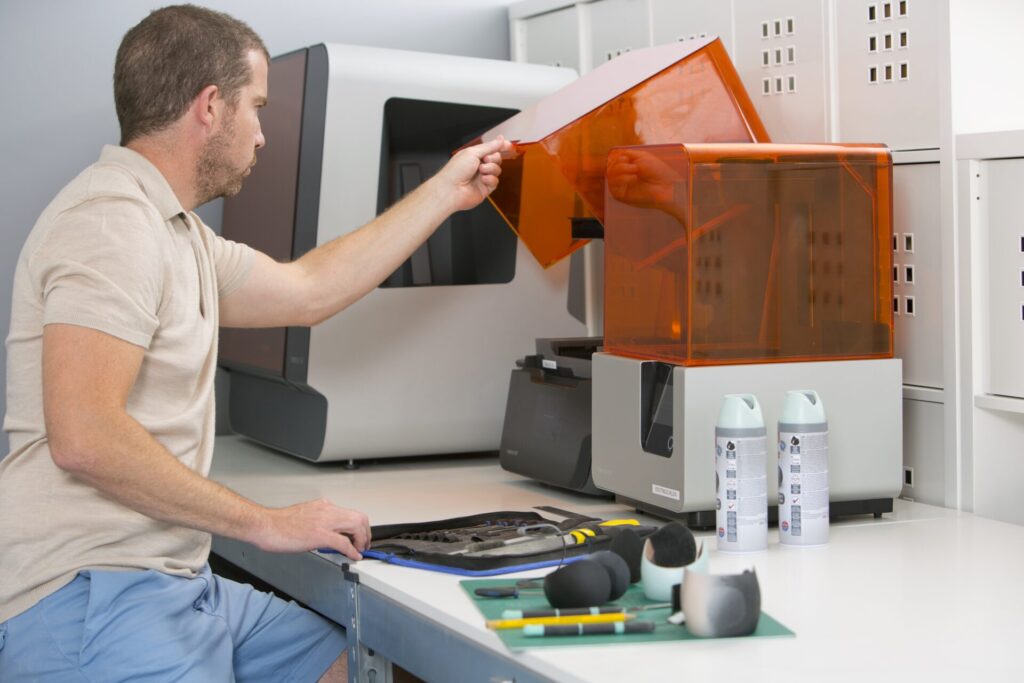
The purpose of prototyping is to reduce the unknowns in initial product development work. Not asking the right questions before starting the prototyping process can lead to expensive design changes later on during product development.
Building physical prototypes can be quite expensive. so, a good product development team will only prototype as much as necessary. A primary challenge for many teams, then, becomes knowing when it is advisable to prototype a product and understanding when a simulation is sufficient. Figuring this out requires a good understanding of the design lifecycle. It also hinges on asking yourself the right questions during the prototyping phase.
Read on to learn a few of the important questions to ask yourself during the prototyping phase.
Can this idea be simulated?
The first question one should ask before building any prototype is whether it’s something that could be simulated instead of prototyped. Simulations can help identify potential problems or limitations in the design before investing time and resources in physical prototyping. By detecting and addressing these issues early on, engineers can avoid costly mistakes and delays during the prototyping stage.
Autodesk Fusion has powerful simulation tools that can often reduce the need for physical prototyping, including FEA tools to simulate loading and the ability to simulate complex mechanisms.
Simulating iterations can quickly narrow down the concepts that you want to physically build. Therefore, it’s important to ask yourself if you can simulate results before developing a new prototype.
Do we understand what’s really important yet?

Once the design concepts have been narrowed down to one or two options, a skilled product development team will meticulously craft the prototypes with careful consideration. Before jumping into physical prototype development, it’s important to nail down the purpose you want the prototype to serve.
What are the biggest unknowns that we want to test? What are the critical functions that need to be proven? Do we want to test an integrated system or a series of smaller simpler prototypes? Plus, you always need to consider if a prototype will
During product development, there are always important functional questions to ask. However, zooming out and figuring out the answers to these questions will help you develop a strategic approach to prototyping and hopefully cost you the need to build multiple prototypes.
How will we deal with lead times?
There are numerous strategies to minimize prototype lead times and costs. Engineers should consider modifying off-the-shelf products or components to create prototypes, as this significantly reduces expenses and allows more time for testing. 80-20 aluminum extrusions are another common technique for quickly building up development framing and structures. Fusion can import many common CAD file formats which can ease layout and design when utilizing off-the-shelf components during prototyping.
If you can’t use an off-the-shelf component, 3D printing is often the quickest way to get a prototype in hand. Even if there is fabrication capability on-site, 3D printing is often still faster and, depending on size, can give the team parts in hand on the same day. Be careful when relying on printing, though, as it is easy to design parts that can be 3D printed but can’t be replicated using mass production processes.
Custom machining is usually the last but necessary resort for prototype fabrication. Autodesk Fusion CAM tools can be used to speed up the process and give the development team insight into the process. However, even in-house machining can often take days or weeks to turn parts around.
If ordering prototype parts from an outside vendor, the lead time can often be weeks. In this case, especially on large, costly, parts, it is good to implement design for manufacturing practices when prototyping. This can save machining time and hence costs on one of the most expensive steps in the product design process.
Autodesk Fusion for prototyping
Prototyping can be costly and time-consuming, but Autodesk Fusion offers tools to streamline the process and reduce expenses. Asking the right questions early on and minimizing uncertainties before transitioning from digital to physical prototypes is crucial. Effective prototyping yields long-term benefits throughout the product development cycle and should be prioritized.