
Elevate your design and manufacturing processes with Autodesk Fusion
Learn how to streamline manufacturing operations management — from pilot project to a company-wide strategy.
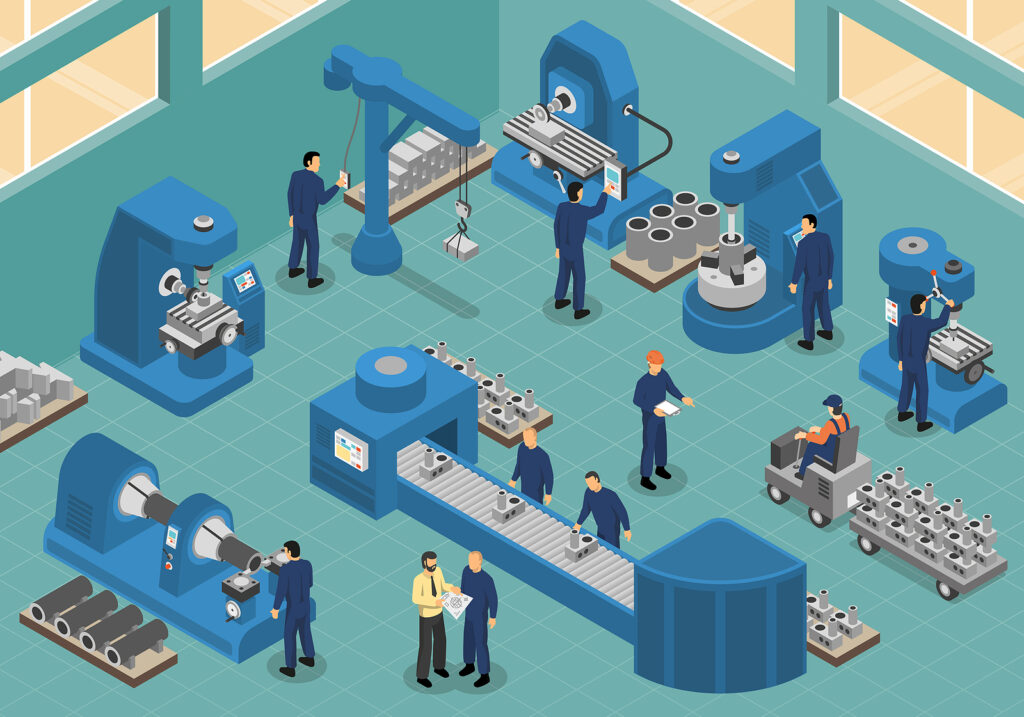
Thanks to technological advancement in the past century, today’s consumers have greater demands than a few decades ago. It’s the operations manager’s job to streamline manufacturing operation management to meet these increasingly demanding customer expectations.
Contrary to what most people believe, streamlining a manufacturing production line doesn’t necessarily mean using next-level automation and high-performance equipment. It can be as simple as applying lean manufacturing to the production line to eliminate waste. Fusion Operations, a manufacturing execution system that allows you to easily track if things are going out on time and that quality standards are met, is a great place to start your journey.
Why is it important to streamline manufacturing operations?
No two companies are identical, and the same applies to their manufacturing: each company has its own complicated multi-step production process. For a company to maximize profits, improve quality, and stay competitive, it must streamline manufacturing operations and reduce production time. Some of the main benefits that streamlined companies enjoy are better quality, minimal waste, faster production times, and reduced costs.
Let’s explore 10 definitive steps to streamlining manufacturing operations management:
1. Start with an underperforming product line
One of the best places to start when streamlining operations is to put underperforming product lines under the microscope. As these products are already facing a variety of problems — from fulfillment to quality to production scheduling to sales to product awareness — they are typically a great starting point.
When examining an underperforming product, it’s easy to focus on what you can directly control — storage space, the factory or plant, the production environment, etc. However, it’s important to step outside the box and examine not just the product but also its production lifecycle for possible flaws.
2. Define KPIs
Defining effective metrics and KPIs to streamline manufacturing operations management is rather easy when it’s clear what to and what not to track. Not all pieces of information will be useful in helping meet the company’s objectives and goals. Be sure to resist the tempting urge to track dozens of KPIs and metrics. Instead, focus on those that are most relevant and can be scaled across all teams. Creating a dashboard that helps teams visualize this data is a great way for all teams to stay on the same page.
3. Capture machine-level data

A manufacturing execution system or MES is an application that tracks, monitors, and controls all the activities on the factory floor. They’re used to streamline manufacturing operations management and ensure that processes and activities are efficiently executed to maximize output. It’s essential to track and aggregate precise and accurate data on the entire product lifecycle in real-time, which is where an MES comes in.
MES are especially useful for capturing machine-level data, such as overall equipment effectiveness (OEE). OEE is a measure of the effectiveness of running a piece of equipment on a specified schedule. As a performance indicator, OEE gives companies an overview of how their manufacturing activities and processes are working.
Fusion Operations takes things a step further, offering real-time data and production reports that allow production teams to fully understand what needs to be improved or changed to better meet demand.
4. Implement PLCs and add-on sensors
During the initial stages of a pilot, manufacturing operation managers typically augment older machines with sensors and PLC controllers to visualize the entire production process. Sensors provide data that can be useful when analyzing a piece of equipment over a specified timeframe.
For example, you can monitor the vibration of a machine, which can tell a technician if the machine is on or not. PLCs, on the other hand, can aggregate large data points, which, when combined with sensor data, provide a clearer picture of the workings of a machine.
When combined, sensors and PLCs offer a hands-off approach to collecting and analyzing data. This method also offers plenty of flexibility and lets operation managers define parameters and performance indicators for every machine.
5. Define and test
The next step is to develop and test an integration system that connects all the data points to one centralized dashboard that transmits data in real time. Next, transform the dashboard into a web-based application that’s accessible to cross-functional teams. This step allows live performance monitoring and data access from any internet-enabled device, no matter the location.
This process also makes it possible to create a database that stores items based on a variety of parameters, such as machine configuration, part number, batch number, etc. You can also add future KPIs and metrics to the dashboard to keep things current.
6. Gain senior management support
Before implementing any organization-wide changes, it’s necessary to get executives on board to bypass any red tape in the way of progress. While there’s no denying the importance of engaging workers on every level of the company’s ladder, every successful change initiative (such as a strategy for streamlining manufacturing operations management) starts by having a committed executive backing the initiative. They can play a variety of roles in the project — from communicator to liaison to advocator.
7. Consistently gather data from every team

Before Manufacturing 4.0, a lot of managers were heavily dependent on intuition and experience to make decisions. Unfortunately, relying on intuition and experience over data never ends well. The modern manufacturing industry demands that decisions be made based on accurate data delivered on a timely basis, especially where streamlining manufacturing operations management is concerned.
When collecting data throughout a project, each team has a specific role to play. The focus of the sales and marketing team is to provide a clear picture of the entire pipeline, along with any data from special promotions or incentives. Finance, on the other hand, can provide an overview and insights into gross margins and how they were affected by the change in production strategy.
8. Begin a company-wide manufacturing intelligence strategy
One of the pillars of a great manufacturing operations management strategy is having access to accurate and precise real-time data. Once your MES starts outputting data constantly, it’s time to move past the basics and incorporate intelligent data-driven strategies into company-wide operations management.
A majority of global manufacturers in a variety of industries rely on real-time factory-floor data to make major decisions. For example, operation managers can use advanced analytics to process historical data and pinpoint major patterns. Additionally, companies can use predictive analytics to give recommendations for the future.
9. Plean ahead for greater integration

The next step is integrating your MES and ERP systems, which better translates whatever is happening on the factory floor into financial reports making it easy for c-level executives to drive results.
By integrating MES and accounting, operation managers will be able to:
- Get real-time insights into the financial status of the company, which can then be used to direct other strategies for optimizing performance.
- Simulate production orders, among other resource requirements.
- Streamline manufacturing operations management by eliminating unnecessary production delays and interruptions.
Integrating accounting and production systems, together with real-time data exchange, helps improve the overall operational efficiency of the company and allows it to adapt to satisfy customer expectations and meet their demands quickly.
10. Define a timeline for a company-wide manufacturing operations strategy launch
The last step of streamlining manufacturing operations management is applying the insights learned from the pilot data. Data-driven strategies are the key to staying competitive and differentiating the company from the competition. However, a company’s success hinges on its ability to aggregate data and use it to inform future decisions. Having completed the pilot, applying the strategy company-wide should be a much more straightforward process.
Streamline your manufacturing process with Fusion Operations
While most manufacturers are taking the necessary steps to apply data-driven strategies to their production lines, a majority of them have found it difficult to maximize their ROI.
However, by enhancing machine-to-machine communication and sharing organization-wide data, manufacturers will be in a unique position to improve efficiency, maximize profits, improve quality and foster innovation and ultimately streamline manufacturing operations management.
Ready to go paperless and streamline your manufacturing operations with ease? Try Fusion Operations today:
