Adolfo Munoz describes his first few months with Temecula Precision Fabrication as a perfect storm. It was just over two years ago when Munoz started with the company, which specializes in precision machining and manufacturing for the aerospace, medical, space, and cryogenics industries.
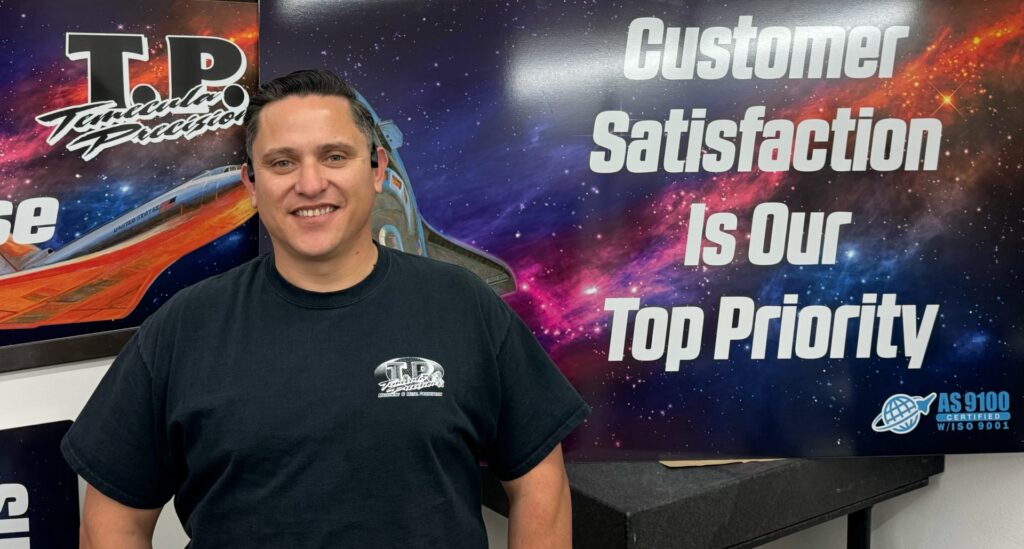
Munoz had joined the company as a CNC programmer, and just a few months later, the QA manager moved into a new position as operations manager and tapped Munoz as his replacement. “I was supposed to be programming machines, but things evolved really quickly,” Munoz says. “Before you knew it, I was no longer on the floor. I’m the QA rep. And my foot has been on the gas ever since.”
In his new role, the first thing Munoz noticed was that Temecula Precision, like many manufacturers that started small, took an “old school” approach to production management. While the company began as a “mom and pop shop,” today Temecula Precision boasts a state-of-the-art facility equipped with 3-, 4- and 5-axis CNC milling machines and live tool turning with a highly experienced staff of 20 operators.
But Temecula Precision still relied primarily on paper routers, travelers, and file folders. Material verification documents, for example, were kept in a storage shed in boxes labeled by year and month. All of the information was accurate, of course, but extremely inconvenient to access.
“We were aiming for much higher levels of efficiency,” Munoz says. “We couldn’t keep the ways of the past. It was simply too much work. We needed a way to harness all of our efforts and propel us into the future, as opposed to us saying ‘well, this is the way we’ve always done it.’”
With approval from his superiors, Munoz began reviewing options for ERP and MRP systems. But Munoz was also familiar with Autodesk Fusion, and he appreciated the way Autodesk platforms were designed to work together.
“I liked how all of the Autodesk tools worked with each other as seamlessly as possible,” he says. “And then I noticed some content about Fusion Operations on my social feeds, so I started following the Fusion Operations account. I saw enough to schedule an interview, and here we are going into our second year with the software. I couldn’t be happier.”
Tracking data, increasing consistency
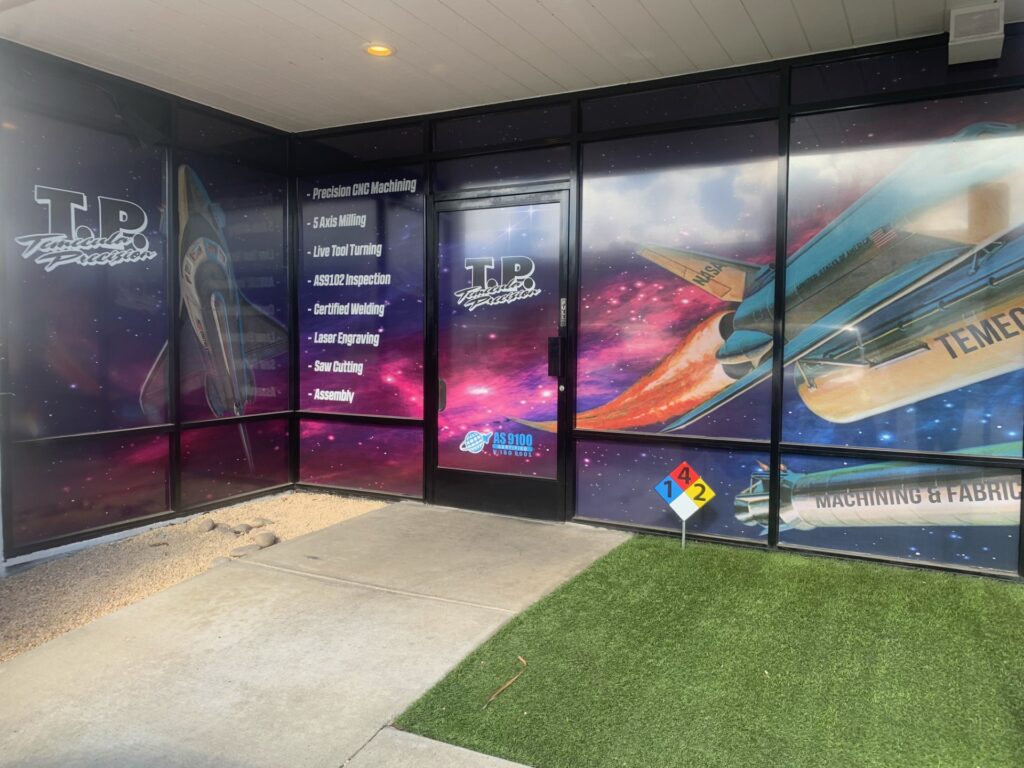
Today, Temecula Precision uses Autodesk Fusion Operations production management and production floor tracking functionality to improve overall efficiency and quality throughout the facility.
“We’re able to improve quality with Fusion Operations because we can track everything much more efficiently from the material inventory to finished products,” Munoz says. “We can track our operator efficiency as well. It’s allowed us to get very granular about our output, which has helped us become a lot more efficient in terms of how jobs flow through the shop.”
One capability Munoz highlights is how Fusion Operations allows his teams to provide very clear instructions to every operator as well as job-specific notes about any special quality checks or tools required. Fusion Operations also makes it easy to document a great deal of institutional knowledge that was previously only known by the most experienced operators — and inaccessible to new ones.
“Fusion Operations takes a lot of the guesswork out of our manufacturing processes,” Munoz says. “A new operator may be just as skilled as an experienced one, but they don’t necessarily know all of our standard procedures. Now we have the documentation and instructions that allow us to be more repeatable in our workflow, which has helped us improve our quality by ten-fold.”
Operator monitoring is another helpful feature that Munoz points to, although acceptance among Temecula Precision’s team was not easy. As a group, they were not accustomed to a digital platform tracking their work. In fact, they were not used to their work being tracked at all.
“Before, everything was done manually,” Munoz says. “We weren’t really tracking anything. And so the pushback on it was significant. But eventually, they realized that the data could work in their favor. If they wanted to prove they deserved a raise, they could point to Fusion Operations. They could say, I have 100% efficiency and on-time parts and my scrap rates are really low.”
Exceeding customer expectations
One of the most important impacts of Fusion Operations at Temecula Precision has been in material tracking. With 20 operators, the company invests heavily in stainless steel and aluminum as well as more exotic materials such as Monel alloys and molybdenum.
“On multiple occasions, Fusion Operations has prevented us from wasting money on material we don’t actually need,” Munoz says. “Before, knowing our exact material stores required someone to take measurements by hand with calipers and measuring tape. Now we can see what we have at a glance, which has helped us exponentially.”
Munoz also calls out Fusion Operations’ ability to help his team limit downtime and get jobs out onto the floor in real time. Processes and other details are saved in the system, which makes it easier to move jobs from one step to the next very rapidly.
All of this has not gone unnoticed by Temecula Precision’s customers. One very well-known aerospace company came in to do an audit prior to establishing a relationship and came away impressed.
“They looked at our routers and our material handling and the whole deal, and they said we were going the extra mile to manage our operations,” Munoz says. “They said they would be fine with steps A and B, but we’re doing A, B, C, and even D, depending on the job. That kind of positive feedback really keeps us motivated. It shows how Fusion Operations has really been helpful for us. It has been beneficial at every turn.”
Support from Autodesk has been instrumental to Temecula Precision’s success, according to Munoz. “The support Autodesk offers is phenomenal,” he says. “I can go to the support team with just about any issue. Typically I just need to be pointed in the right direction. Autodesk really makes it easy.”
For now, Munoz remains focused on getting the most out of all of the features within Fusion Operations. “I haven’t fully utilized all of the options that Fusion Operations offers,” he says. “Right now I’m working on production scheduling, collaborating with our production manager to input all the data machine by machine. We’ve made a lot of progress, but we’ve only scratched the surface of what’s possible.”