
Elevate your design and manufacturing processes with Autodesk Fusion
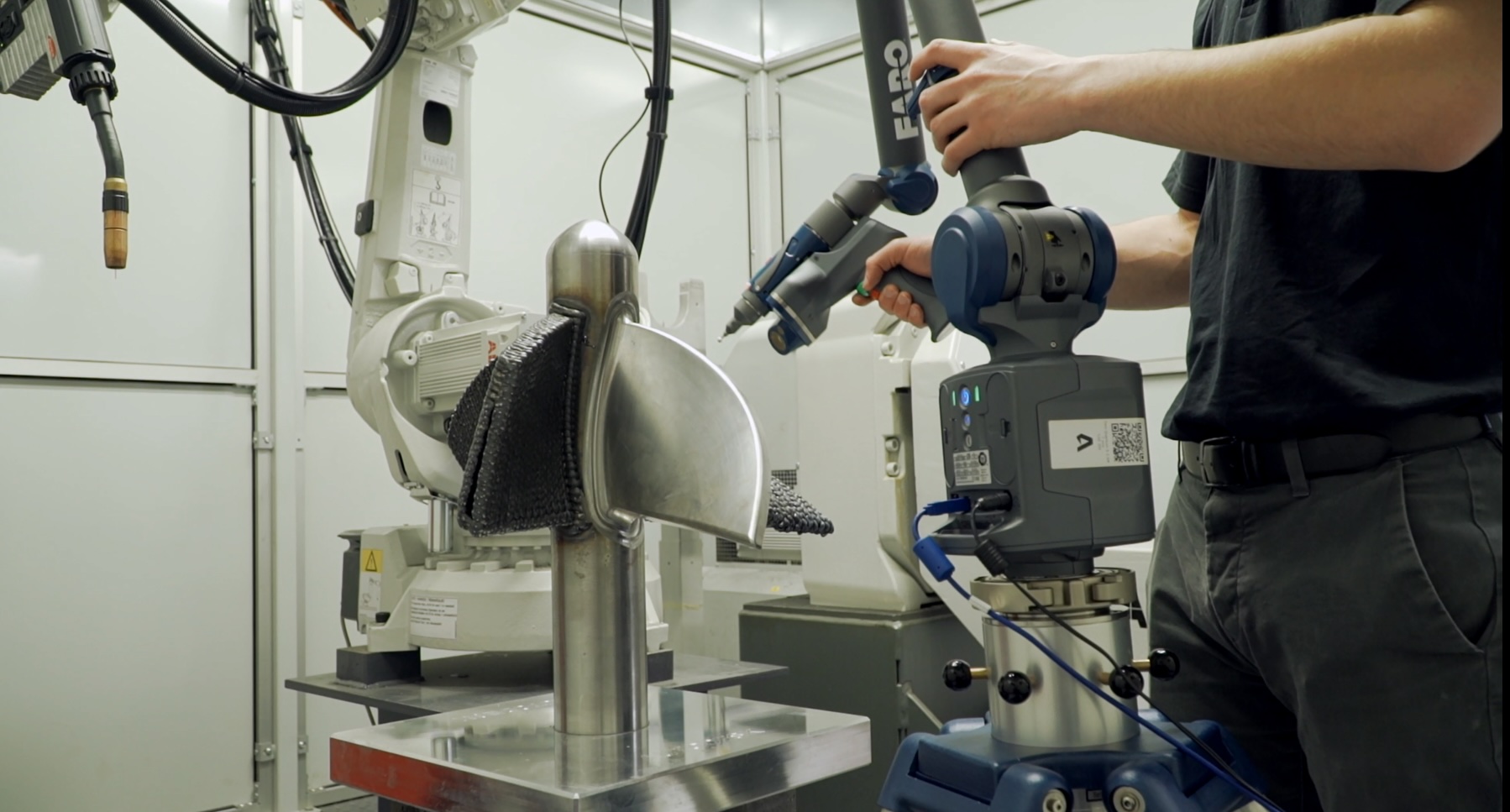
An Engineer’s guide to understanding and implementing additive manufacturing in the production process…
Introduction

Image Source: Marines
Additive manufacturing (AM) is a term used to described the set of manufacturing processes that progressively add layers of material to manufacture your products, and it could change the way you go about engineering your products. Instead of being held back by manufacturing constraints, you can design the component you need, focused only on the function it requires to perform and meet clients’ needs. You have full control over the interior structure of the part, so you can include voids, lattices, and other hard-to-manufacture structural components that can help cut down on material use and increase functionality. Subassemblies that used to require multiple parts can be combined into a single component. You can customize everything you make to suit your individual customers’ preferences. With all the recent innovations in the additive manufacturing industries, now is the time to consider additive as a viable alternative to traditional manufacturing approaches and how to best take advantage of the design freedom it offers.
The Evolution and Growth of Additive Manufacturing Processes and Materials
What began as a rapid prototyping tool has now transformed into a multi-faceted manufacturing system capable of producing a wide variety of parts to functional specifications. Let’s take a look at some of the various forms of AM and how they are useful in their respective fields
VAT Photopolymerization – Stereolithography (SLA)

A vat of photopolymer liquid is cured by focused UV light which builds parts layer by layer without the need for structural support. Stereolithography encompasses the process of manufacturing photopolymerization.
Binder Jetting

Image Source: Wikimedia
A powder substrate is hardened when the printing head deposits a strategically placed drop of binding fluid in a layering process.
Material Jetting

Image Source: Navy.mil
Primarily used where surface finishes and form testing are needed, material jetting involves a heated inkjet printhead that lays down successively solidifying layers of waxy material to form prototyped designs.
Material Extrusion / Fused Deposition Modeling (FDM)

Image Source: Flickr
Most commonly seen in recreational 3D printing technology and rapid prototyping, this approach utilizes a heated nozzle which extrudes a plasticized material to form products from a spliced CAD model.
Powder Bed Fusion

Image Source: Wikimedia
Laser or electron beams are used in the powder bed fusion (PBF) process to rapidly fuse successively-layered powder material such as various metals together. PBF is the most common technique used in metal 3D printing of circuits, structures, and parts.
Sheet Lamination

Image Source: Wikimedia
Sheet lamination encompasses the bonding of ribbons of metal or paper through ultrasonic welding or adhesive respectively, with the finished shaping being completed through further material removal processes. Products constructed through sheet lamination are not compatible for structural use.
Directed Energy Deposition

Image Source: Wikimedia
DED is commonly used to repair or add to existing components using a multi-axis nozzle to extrude laser-melted material onto the printing surface.
How is Additive Manufacturing Different?
When you set out to design products, you typically have to design around the manufacturing process, which results in additional costs, time, or even material. Imagine being able to fully combine what was previously a set of subassemblies into one manufacturable part. You have likely had to overdesign certain parts to withstand common manufacturing processes, which a dilemma that additive manufacturing can help you get around. When you design with AM in mind, you can forget about designing for anything other than functionality. Looking deeper into this, you can save time in the design process while also saving your client money in manufacturing costs relative to design complexity.
As engineers, we’re always thinking of new ways to improve components and designs. We have all had amazing ideas, only for them to crumble with the realization it would be nearly impossible to manufacture. With AM, you can enter the realm you previously thought impossible – releasing your full problem-solving potential. If you want to make internal voids or complex lattice structures, there’s a form of AM that can make it happen. The freedom and potential you can have in your future designs are immense if you cast off all design limitations. The path for pure unadulterated design can be paved with AM, although it can have some material and production limitations.
Design for Manufacturability (DFM)
What is DFM?
Design for manufacturability is a proactive process used to maximize the design of components for the intended manufacturing process.
Constraints of Traditional Manufacturing Processes
Looking over the typical manufacturing processes of machining, casting, injection molding, and forming, we see the shortcomings in each technique. When you design with injection molding, you are bound by many limitations, from quality assurance to assembly issues. In addition to being limited to solid components, you are also limited by shapes and designs of parts to allow for mold separation. However, what if you don’t need a solid structured part or need one with a complex shape? With previous forms of manufacturing, you would be kind of stuck; but not with additive.
Let’s look again to machining, one of the many great forms of manufacturing, yet full of limitations. When your part is being machined, there is room for operator error and you are limited in degrees of freedom from the machining head. While you can generally design around these constraints, why do it when you don’t need to? Each manufacturing process you want to use requires that you have some knowledge of how it works when you design a component. All the time you spend learning how a manufacturing machine works could be spent improving your original design. Manufacturing capabilities have been significantly restrained for thousands of years, and no longer should engineers have to work around these issues.
Downside of DFM
You should be starting to get an idea in regards to the downside of DFM, but let’s discuss it further. It’s something we do on a daily basis, yet it’s time-consuming and can be costly. In situations where additive is applicable, it can compensate for many of the downsides of traditional techniques.
You may also want to focus on improving the design and functionality of a part, but given time constraints and the need of DFM, you may not get a chance. Eliminating the need for DFM in a project allows for you to focus your energy into actually improving your designs, rather than hassling with manufacturing. While focusing on manufacturability may decrease cost, you can significantly increase value for the client by focusing on improving design and functionality. Compromising on design just to make a product manufacturable hurts both the engineer and the integrity of the end product.
Design for Functionality (DFF)
Perhaps the key aspect of additive manufacturing and what makes it the perfect fit for your possible needs is its ability to produce fully functional products without manufacturing setbacks. AM overcomes the drawbacks of DFM and pushes you fully into designing for functionality. There are obviously material limitations, which we’ll get to later, but where it’s applicable, it can help out in your design process significantly. Since you have more time to focus on design and functionality with additive, there is a whole new array of opportunities that have never existed before. Whether that be through the exploration of new ergonomics or significantly improving function, you now have options.
Your specific design software has its limits, but additive can push beyond them. For example, modeling latticed structures can be time-consuming at best. With many additive techniques, you can actually manufacture more complex parts than are capable of being designed within software. Through many additive software, you can automatically pinpoint areas where material is unnecessary, and either remove it altogether or easily replace it with a complex lattice structure. AM isn’t just about increasing the time you can spend on design, it’s about being able to manufacture beyond what you can currently easily design. It creates true design freedom.
Instead of creating complex subassemblies through multiple designs, you can focus on the function of your component. AM requires absolutely no tooling, so the end product can be exactly what is needed to satisfy your customer. Instead of needing to compromise on certain specified design criteria due to manufacturing capabilities, additive manufacturing allows engineers to solve problems without constraints. DFF is what design was meant to look like.
Lightweight and Strong

AM has brought a wide array of new materials into use, such as polymers, plastics, lightweight metal, and composites. These materials aren’t always perfectly suited for your needs, but when they become an option in your project, they can increase your design flexibility. One of the biggest setbacks in traditional part design is when we have to create a part that can actually survive the manufacturing process. Let’s take a look at some of the techniques you can combine with AM that will increase strength yet decrease weight.
Undercuts and Internal Structures
Traditional manufacturing has held back the engineering world’s ability to design with undercuts and internal structures. If you want to design any sort of recessed surface or internal support, you would have to create subassemblies and break down your part into workable pieces. The only other alternative to this time-consuming breakdown of your part is using expensive multi-axis machines. AM allows aspects like undercuts and internal structures to be designed into one singular part, which means no assembly or extra work – just pure manufacturing.
Latticing
A lot of material goes wasted in manufacturing, not because of scrap, but rather because of unnecessary material being in a part where it isn’t required. Many manufacturing styles don’t provide the ability to remove material in certain areas, increasing component weight and material cost. Through latticing, you can create parts that are as strong as you need them, yet only use a fraction of the material at a fraction of the weight. When civil engineers design a bridge, they could get the job done by building a solid block, but that would be overkill. Instead, they design the equivalent of lattices (trusses) to support the structure with as minimal material as necessary. This is similar to how latticing allows you to optimize a part and remove unnecessary material, focusing in on what is actually needed to function. Anyone can design a solid part that won’t break, but it takes an engineer to design a part that just barely won’t break.
Part Consolidation
As we discussed a little in the undercuts section, you can virtually eliminate the need for subassemblies with additive technologies. You have the capability to consolidate all of your parts into one design and one production batch. Other than decreasing design time, you can increase your material strength and decrease component fatigue all through AM consolidation. Consolidation is one of the key areas you can focus on to reduce manufacturing costs, part complexity and even reduce failure points. When you combine all needed functionality into one easy-to-manufacture solid component, nearly all of your design criteria are optimized.
Customization
You can only customize a part up to the extent that your manufacturing process allows. There’s a gate, if you will, that gets unlocked by additive manufacturing, which allows you to fully customize your parts.
Medical Applications
Customization has the ability to offer necessary design for unique shapes of individual patients in medical applications. Start thinking about hip replacements, prosthetic limbs, implants, and you can start to see the possibilities. Beyond just manufacturability, AM allows engineers to design a medical device that perfectly interfaces with a patient. Whether that be fitting a wound or shaping around a bone, additive designs can be drawn from scans and be created with no invasive surgery. Many times, doctors will have to do an exploratory surgery just to analyze if a certain implant component will work. With additive, you have the capability to design custom fit parts with randomized lattices to help with healing and adhesion. Some of the cost hurdles that may be presented with additive manufacturing are overcome with the ability to increase functionality, specifically in medical applications.
Customer Preference
If you’re an engineer, your head might start hurting a little when you hear the phrase “customer preference.” Customers can be some of the most demanding people you will work with, but after all, that’s where your paycheck comes from. Currently, when a customer comes to you with certain preferences, you feel additional pressure from what is capable of being machined or forged. Additive manufacturing solves this, allowing you can start focusing solely on making the customer happy and designing a good part. You can optimize your components however you want, and create exactly what the customer desires – a part you are proud of.
Mass and Energy Exchange

Image Source: Wikimedia
Surface area is key in mass and energy exchange components, but with typical production techniques it can be hard to come by. Think about the limitations of creating internal or external surface area using processes like machining or casting. When creating heat exchangers and other components, you no longer have to ask “how much surface area do we need?” Instead, you can start asking “how much surface area do we want?”
Increase in Surface Area
Since most techniques of AM involve some sort of printing or curing head, materials can be created layer by layer. This also means that surface area can be adjusted on a nanoscale, and densities of structures can be finely tuned. Instead of increasing surface area through a change in overall dimension, you can increase surface area within the same dimensions using creative AM techniques. Imagine the increased thermal characteristics of an energy exchanger with a maximized surface area in a relatively small space.
Injection Molding
While it may not be obvious at first, the combination of AM with injection molds can allow you to design with greater functionality in mind, rather than conforming to the molds’ capabilities. Additive manufacturing allows for integrated cooling channels throughout injection molds, allowing for faster cooling time and increased production. One of the biggest setbacks to injection molding is the cooling time for batches. Through use of additive technologies, cooling channels can be organically and efficiently incorporated throughout each injection mold as desired. This faster cooling rate achieved through the channels also significantly reduces component warpage from uneven cooling. It can even prolong service life through less thermal stress.
Technologies Enabling Design for Additive
Additive manufacturing is held up by the various technologies and software that are constantly improving and shaping the industry. Advances in design software and increased production capabilities give you the ability to focus on design functionality, rather than spending more time on manufacturability.
Computer-Aided Design (CAD)

Image Source: CHIPS
CAD software forms the basis of most engineering professions, and it is perhaps the key aspect of your everyday job. Whatever design software you use, there is one out there that is optimized and perfected for every form of additive manufacturing. When designing a very complex part, you may struggle with how to optimize your CAD software to create such designs. At the core of additive manufacturing is CAD software. Many programs have become tailored or are directly compatible with additive techniques like laser sintering and 3D printing. This allows you to design your part in CAD like anytime else, then simply export your design to manufacturing. The result is both instant and perfect.
These design software have grown to accommodate additive techniques, which can allow you to actually design with organic and natural shapes. The ability to 3D print a complex shape means nothing if it takes too long to model it in CAD. There are some ways, below, where computer-aided design has improved to allow for organic design.
Topology Optimization
To describe it briefly, topology optimization is the process of maximizing your material layout within the given constraints of a design. Essentially, when you use topology optimization on your part, you focus material on high-stress locations and remove material where unneeded.

When a component is topologically optimized, it ends up looking far more organic than would be easily-designed in many CAD software. With the advancements in organic CAD abilities, you can actually use natural flowing structure for functionality rather than simply aesthetics. Many software can analyze your CAD designs and optimize them for handling actual stress and strain. The process as a whole ensures your parts are strong, but removes virtually every bit of unneeded material, saving both you and the client a lot of money in possible excess material costs.
Structures within the same external dimensions of a part end up becoming organic flowing supports instead of geometrical shapes like commonly seen in traditional designs. This technique is unique to additive manufacturing, and it allows you to design for actual stresses, rather than theoretical. It is a pain to design using organic structures, as we all know. The key is to understand that advances in CAD software, along with AM, allow you the possibility to design organically, rather than geometrically.
Latticing
Latticing allows for optimizing manufacturing material requirements and designing organic parts for many industries. As we discussed earlier, latticing becomes an easier task through additive manufacturing, but it can be hard to design for with traditional CAD software. You may understand that latticing could help you in your component design, but how do you overcome the challenging CAD design hurdles? Let’s look at some easy ways to design for latticing and analyze the resulting structure.
Software
Latticing is an incredibly useful and innovative additive technique, but how in the world do you design lattices in your CAD software? There are innovative software out there that can help you design with latticing by automatically generating complex, lightweight parts with lattice structures. The generative software can take your part and organically incorporate latticing within the structure and optimize supports for necessary strength.

By far, the biggest issue with most manufacturing techniques is the inability to remove material from places that are otherwise unneeded. Designing in lattice structure may be an obvious solution to you, but typical CAD software doesn’t make it easy. Not to mention the manufacturing hurdles you are probably going to have to overcome in the production process. You can quickly and easily incorporate latticing into your selected designs and provide for internal stress analysis and hollowing with these new latticing software.
Another key industry for latticing technology is medical orthopedic applications. Bones and tissue have been proven to bond far better with roughly latticed material rather than smooth manufactured parts. Most latticing design software allows you to design micron-accurate randomized latticed structures into your components to perfectly fit your client’s needs. Bone growth is improved with randomly latticed parts as well as the increased ability to provide a solid yet organic interface for the body to begin healing around. When a lattice is randomized organically, the adhesion to organic surfaces through healing increases drastically. Only additive manufacturing allows you to design medically optimized parts with latticing, and there are few better ways to customize engineering design for the medical industry.
Generative Design
As engineers, we constantly try to mimic and recreate nature’s designs. Generative design is exactly that, and through additive manufacturing, it can become a relatively easy reality. There are many generative design programs where engineers can input constraints and the software will develop organic and perfected structure. The generative design software iterates each design automatically until the generated structure is organically perfect for your design needs. It does the work that used to take days or weeks of analyzing in just a few minutes. By saving time and money, boosting creativity, and integrating beautiful geometry, generative design may be exactly what you need to impress your boss. You now have the ability to do weeks’ worth of intensive engineering in no time, which is something to consider when weighing design options.
Limitations of Additive Manufacturing
While additive manufacturing can overcome many problems in the design process, like any other technique, it has its drawbacks. As you likely realize, AM is still an emerging technology, which means that many common constraints like time, cost, and material have to be compromised with maximizing functionality.
Cost
Cost is a big limitation when it comes to additive. There are many printing and sintering machines that are going to cost upwards of several million dollars. If the machine doesn’t drive up the cost, several AM techniques can require longer production time, which in turn drives up costs. While cost is usually higher in production with additive, there are circumstances where it can match other techniques.
Manufacturing Time
Additive is by no means lightning fast. As engineers, we may like to think of 3D printing as rapid prototyping, but on a large scale, additive is usually much slower than other manufacturing processes. Many additive techniques can also require post-processing after printing, which further increases production time.
Material
Likely the biggest drawback for engineers’ use of additive manufacturing is the limitation it presents you in material. For example, printing with metal is being pioneered by the process of powder bed fusion, but the process is still in its infancy in regards to what it can offer you as an engineer. Even if additive allows for your desired material, the process of layering and production may produce flaws within the structure.
Summary
Additive manufacturing is rapidly growing into a revolutionary engineering technology that has the ability to completely shift our design methodologies. While AM isn’t perfect for every project, it may be good to consider for some of the more technically complex projects you are working on. Some forms of additive are naturally going to be more expensive, or even time consuming, but the customizable benefits and design focusing aspects can make it a viable option.
You may have to alter how you design with additive, but only in ways that drastically improve the end product. As you are well aware, engineering is all about compromise, and additive can allow you to increase your focus on functionality while possibly compromising on other aspects. Currently, the cutting edge of the manufacturing industry lies in additive technologies, and you have to decide if riding that additive manufacturing wave is the perfect fit for your design project.