
Elevate your design and manufacturing processes with Autodesk Fusion
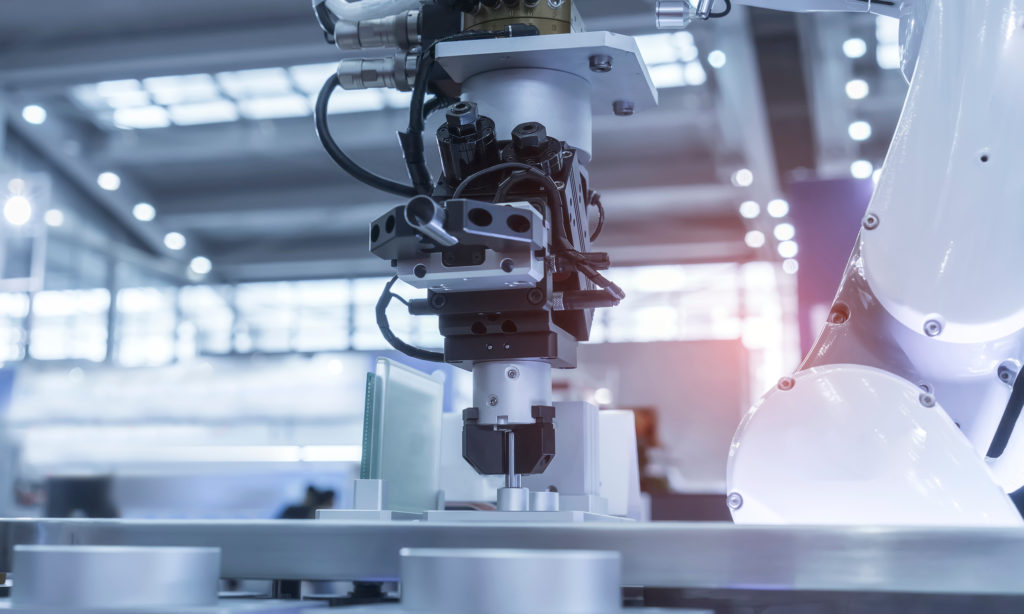
These days, most professionals are trying to accomplish tasks faster than ever before. An invigorated focus on efficiency and proactivity has been the impetus for this shift. While traditional industries aren’t eliminating the human element from the equation, many are looking to strategically offload certain tasks. Machine learning adoption is thus becoming a differentiator between companies. But how exactly does automated machine learning tie into industrial automation today? What use cases does it have in the real world?
How Machine Learning Works

Machine learning is a subset of artificial intelligence and is an algorithmic framework that learns automatically from experience. This experience stems from the data that machine learning models analyze at any given time. Companies with customer databases or online systems use machine learning to make sense of the information they have, making it easier to determine patterns or make predictions. Machine learning thus helps companies understand the mountains of data they have.
Since machine learning was designed to work with computers, it can be an ideal sidekick in the push for manufacturing’s digitalization. Teams are harnessing the technology to help automate a variety of processes. Overall, global industrial players are aiming to boost the productivity of their facilities. This happens when workers are freed up to tackle other projects.
Let’s take a closer look at how industrial automation benefits from machine learning.
Better Maintenance Planning
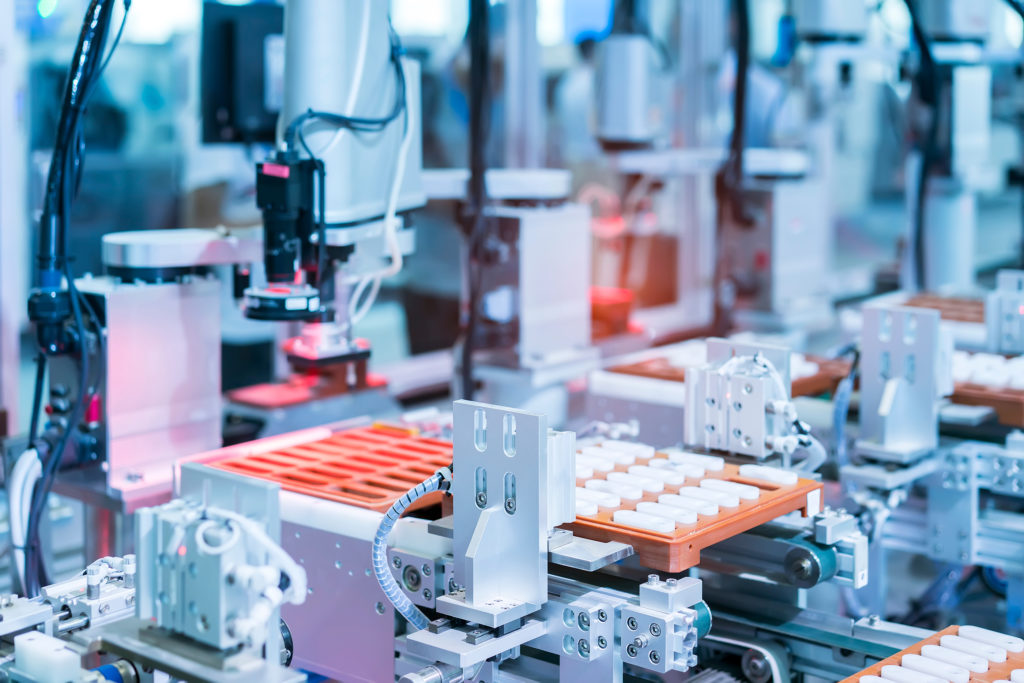
Automated machine learning is commonly integrated with computerized machinery in the industrial space. These systems are great conduits through which algorithms can work their automated magic. Traditionally, machinery lacked integration with sophisticated electronics. Maintenance workers accordingly had to perform reactive maintenance to keep equipment running. Without access to detailed operations metrics, workers were left in the dark — not knowing a problem was brewing until it became apparent.
Modern, digital industrial equipment has transparency built-in. It’s much easier to monitor multiple machines and keep tabs on performance. Changes in efficiency, output, pressure, and even thermal activity can signal impending issues. We can assign machine learning algorithms to monitor these systems. Models can tell us when a machine is experiencing issues or in danger of encountering problems at certain intervals. Continued learning thus helps machine learning technologies determine predictive maintenance schedules. Technicians previously shouldered this burden. Even established manufacturers are now riding the IoT wave. These machine learning models can be applied across the factory to assess the health of customized machinery groupings.
Increased Production Volumes and Collaboration
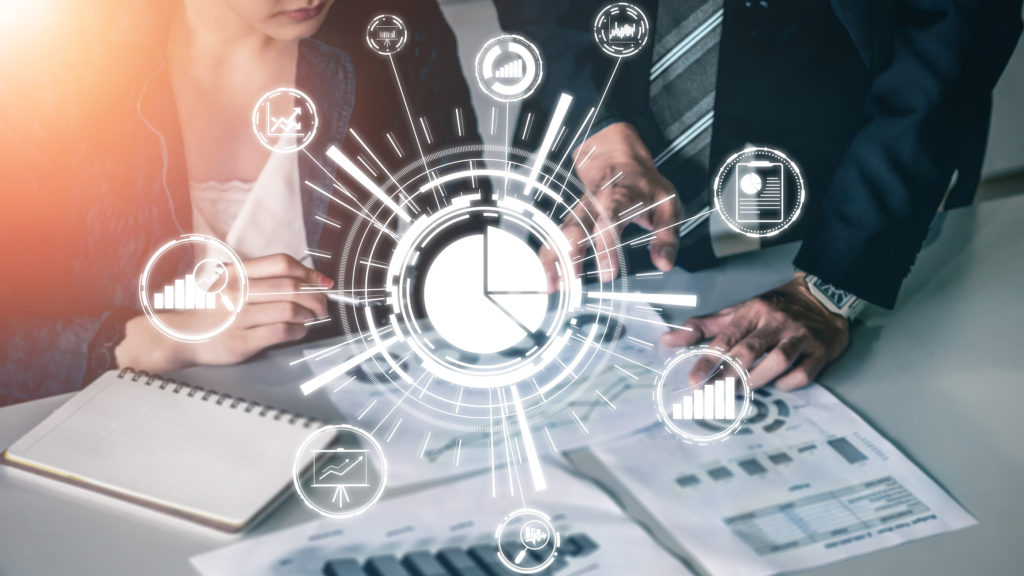
The industry relies upon securing raw materials, mechanized capital, and other resources essential to production. The steps in the process form what we know as the supply chain. Machine learning models can help companies identify the lowest-hanging fruit — or the areas ripest for improvement. Shoring up the supply chain ensures higher production, by eliminating pesky delays or extraneous costs. Machine learning can show us where our expenses are stemming from, how scheduling can improve, and how each provider’s role in the chain changes on a daily basis.
Production depends heavily on yield rates. Yields are a function of quality control processes, and how well they detect defective units. This quality-driven dataset is visible to machine learning algorithms, which can suggest pathways for improvement. Where are our problems occurring, and are certain products or batches especially problematic? How can we maximize our inventory? Machine learning can help answer these questions.
The machine learning process is results-driven in that it provides team-agnostic insights that are easy to digest. It’s otherwise quite easy for teams to become siloed in larger facilities—where physical distance and operational breadth force teams to divide and conquer. This isn’t always optimal, especially when problems impact multiple teams. Machine learning gives teams the power to review centralized analytics. This single source of information makes it easier for stakeholders to reach a unified consensus.
Machine Learning and Industrial Automation
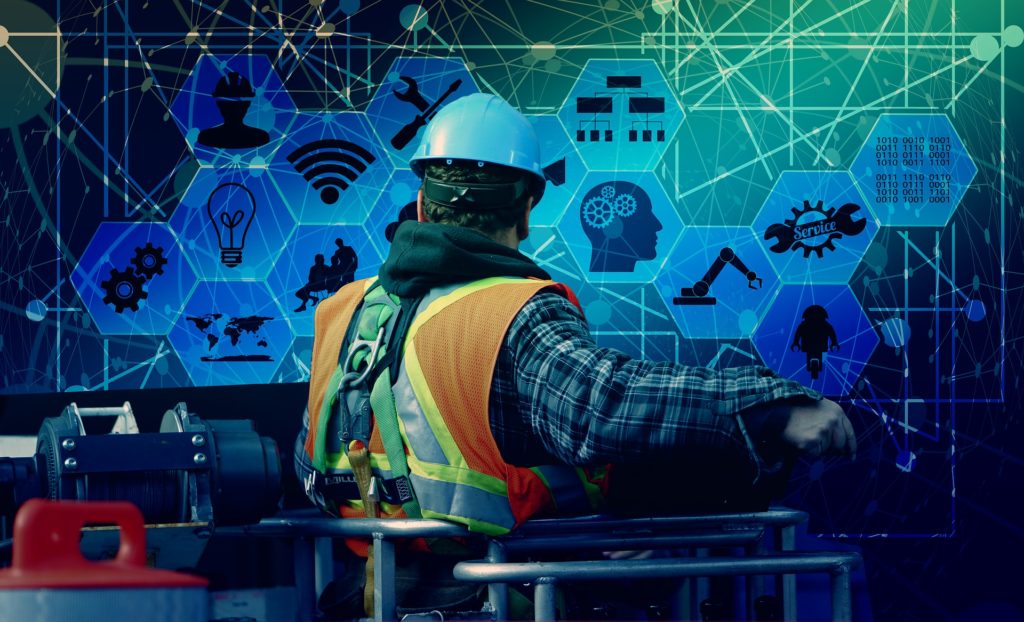
Industrial automation and machine learning have the same goal: to optimize workflows and remove productivity barriers by automatically handling tedious time-consuming tasks. Machine learning algorithms are adaptive and poised for adjustment in lockstep with the dynamic industrial landscape. A propensity for learning from data means these algorithms won’t lose effectiveness — they’ll simply become better over time.
Industry giants and startups alike will enjoy the cost savings and productivity that machine learning can provide. The space is already fiercely competitive, and manufacturers that openly embrace digitalization have the best chance of standing apart from their peers.
The Autodesk Research Team is currently conducting research around how automated machine learning might help with the optimization of 3D model development in Fusion 360, including the potential to recover or refine parametric history.
Download Fusion 360 to see how our automated processes like parametric modeling and generative design can improve your workflow and manufacturing process.
