
Elevate your design and manufacturing processes with Autodesk Fusion
Water jet cutting is an effective cold-cutting process that saves time and money. Learn the basics of water jet cutting and how it rises above other manufacturing processes.
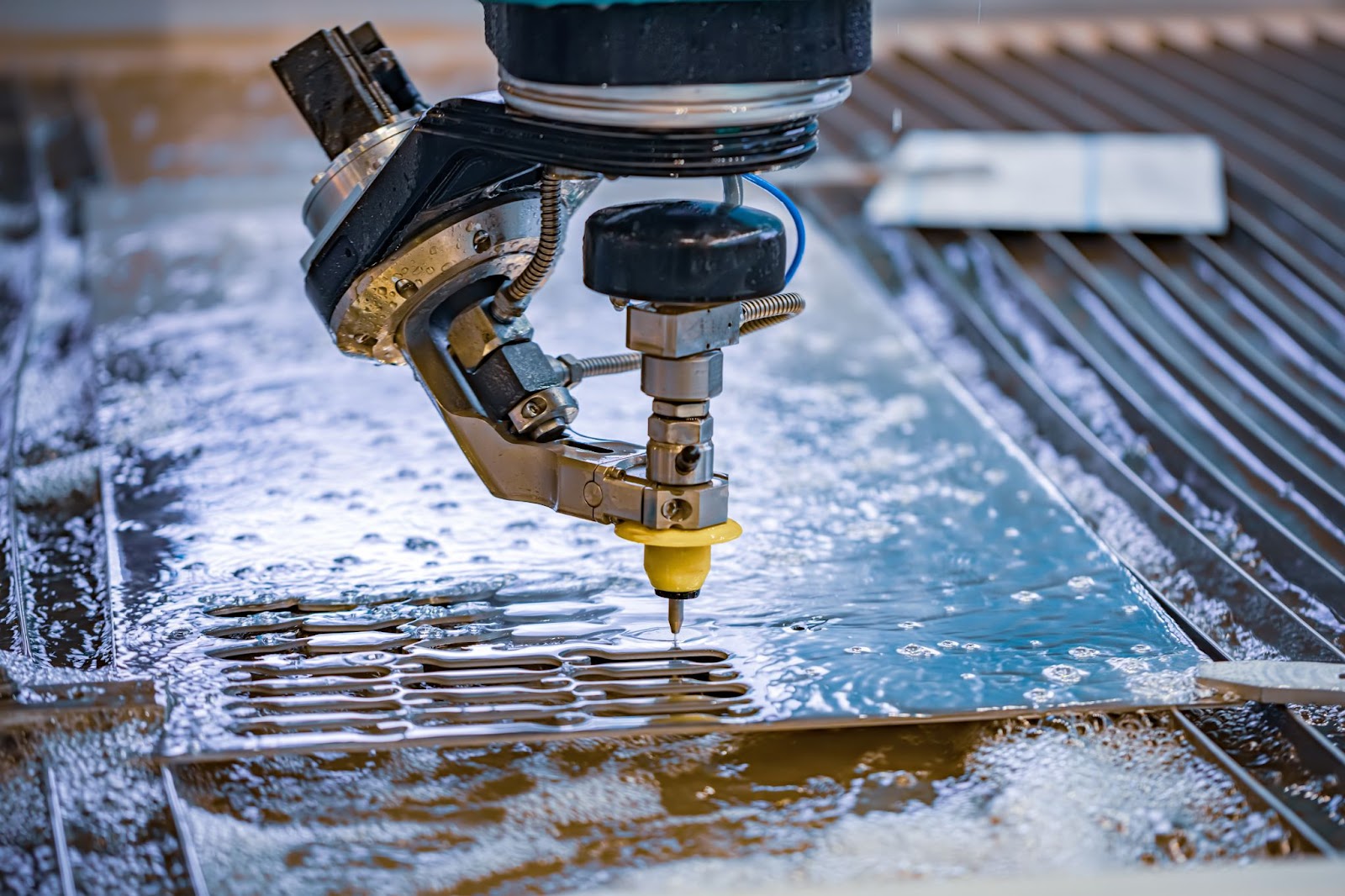
Among the many manufacturing innovations of the 20th century, water jet cutting remains one of the most significant advancements. In 1965, Dr. Norman Franz invented the first water jet cutting machine for the lumber industry. Six years later, the first commercial water jet cutting machine was installed at Alton Board Box Company to cut cardboard boxes. Almost a decade later, water jet cutting machines became commercially available. Since then, water jet cutting has diversified between many different industries.
Water jet cutting is a computer numerical control (CNC) process of using the energy from high-speed water jets. Pressurized water, funneled through a narrow outlet, creates a mighty stream of water that can cut through paper, stone, and metal. Water jet cutting is extremely versatile and produces accurate and less abrasive edges than other manufacturing processes.
How does it work?
For water to erode through an object, it would take millions of years. But, pressurize a stream of water at around 390 MPa (roughly 4,000 atmospheres), and it takes far less time. Pressurization is only half of the equation, though, as one would also need to feed the pressurized water through a small-bore nozzle. The nozzle is typically at or less than 0.1 mm.
The combination of ultra-high pressure and an ultra-fine nozzle creates water speeds three times the speed of sound. Naturally, water shooting at an object at the same approximate speed as an SR-71 Blackbird will cause some damage. So what could an engineer cut with a water jet?
Water jet cutter applications
The list of water jet applications is endless and widespread. Water jets can cut through stone, tiles, glass, metal, food, composites, and plastics. Water jets are used to stencil-cut and mass produce metal parts in aerospace and automotive industries. Both industries require a high degree of accuracy, fitment, and durability, all of which can be achieved using water jet cutting techniques.
The benefits of water jet cutting
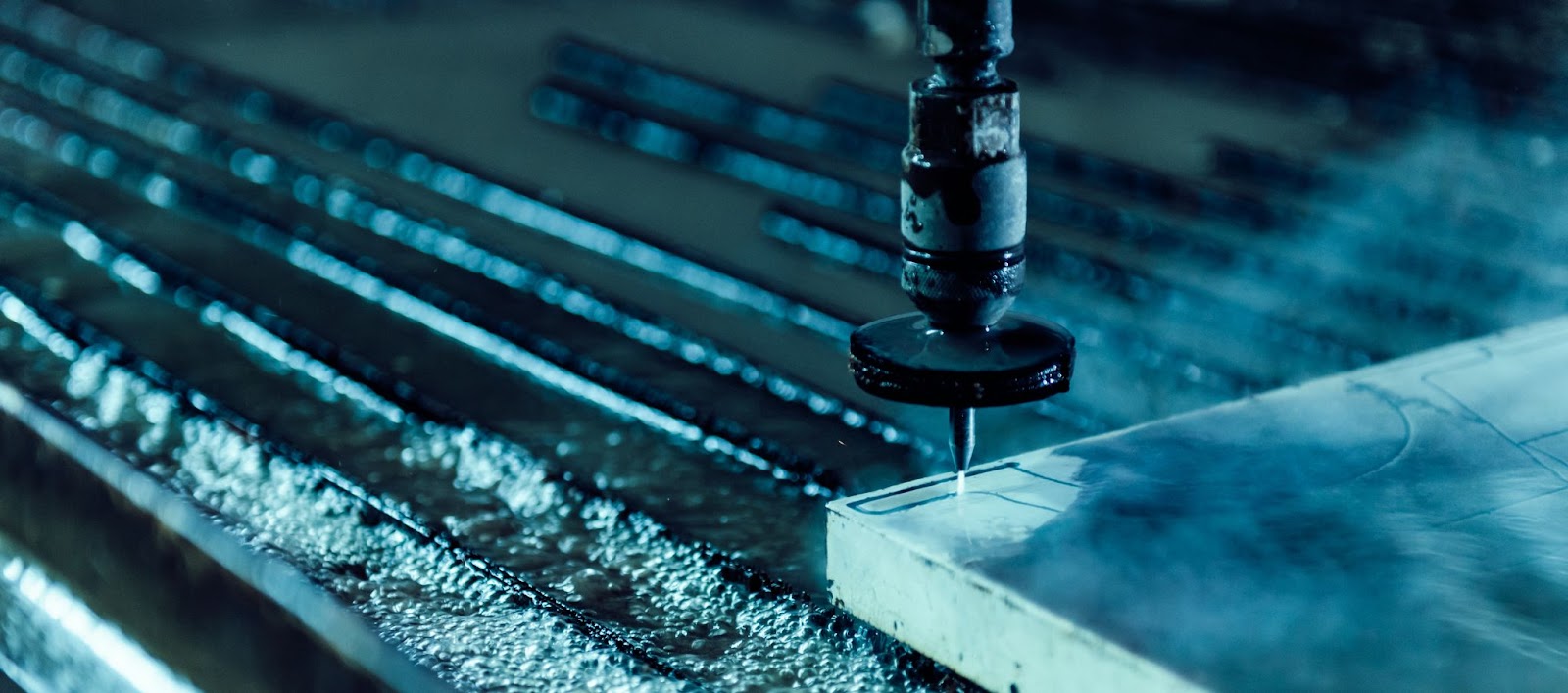
Water jet cutting stands out from other CNC machines because of it’s precision and ability to produce smooth cut edges. Softer edges require less edge treatment after the initial cut because of their extreme precision.
Other benefits include:
- Increased efficiency and reduced production costs – Using a water jet increases efficiency and saves money because it is a cold cutting process. Other processes require hot cutting techniques, which can potentially create heat zones. Heat zones cause parts to warp or weaken. Also, the energy needed from the heating process requires more power.
- Accurate cut-outs – The water jet cutting process produces precise cuts within 0.1 to 0.2 mm.
- No material thickness limits – Water can be mixed with an abrasive solution to increase the cutting capabilities. Water jets can cut through materials over 25 mm thick.
- No required tool changes – Other CNC machines require different cutting edges for various applications and materials. On the other hand, water jets do not require any additional nozzles, eliminating the time spent swapping tool attachments in between cuts.
The benefits are seemingly endless, which makes water jet cutting one of the most efficient processes on the market.
Like any other CNC machine, Fusion’s comprehensive software package provides an integrated computer-aided design (CAD) and computer-aided manufacturing (CAM) platform for all your water jet cutting needs. Try Autodesk Fusion today to improve your manufacturing process!