
Elevate your design and manufacturing processes with Autodesk Fusion
This post is also available in: Français (French) Italiano (Italian) Deutsch (German)
Injection Molding Simulation technology inside of Fusion enables you to simulate your own injection molding studies right inside Fusion.
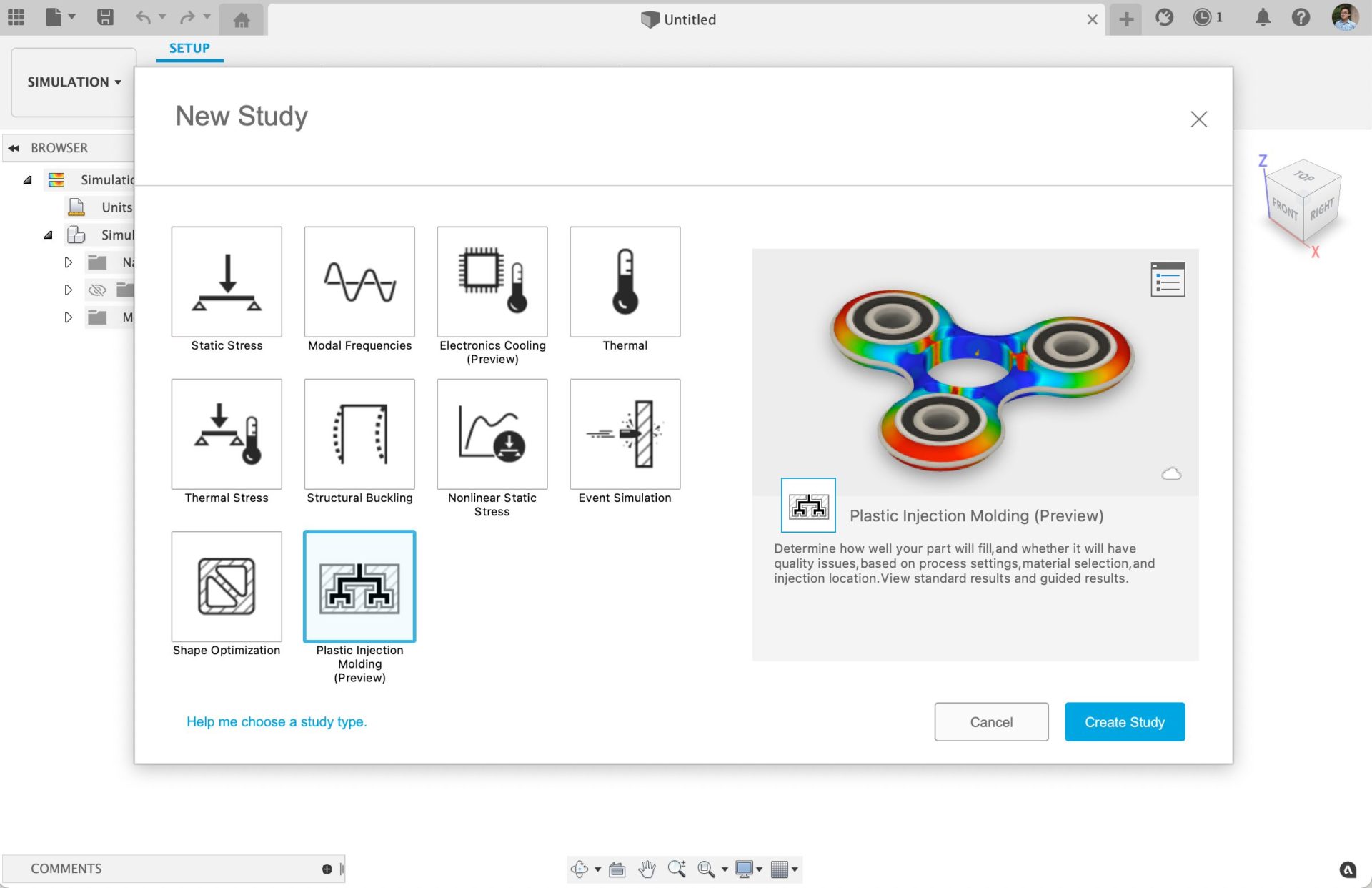
You can find plastic injection molded parts everywhere; just look at consumer products, medical devices, and automotive interiors. In many cases, plastic components define the exterior shape of a part and hold the technical components inside, protected, dry, and in place. The advantage of using injection molding for manufacturing is to produce complex, high-quality parts in a cost-effective and highly repeatable way. It is also capable of producing parts in high volumes and is incredibly efficient.
However, getting the plastic part you designed to come out of a molding machine can be pretty hard. The ability to fill the mold completely, for example, can be highly influenced by the part’s design. The final part’s overall quality is also dependent on several factors and can result in visible flaws on the part surface or dimensional variation preventing product assembly.
For over 40 years, Autodesk Moldflow has defined the space of injection molding simulation software and has been widely used in the plastics industry. It has helped flag molding problems before creating the mold by assisting analysts in making informed decisions and minimizing problems before they appear on the production floor. However, Moldflow products were created to address the needs of specialized and dedicated users, those who dig deep into the analysis results for data-driven decisions to provide design recommendations to team members. The “Moldflow Analyst” jobs typically revolve around the question, “How do I manufacture this plastic part” and typically utilize CAD design as part of their input. Using simulations, they make recommendations on design decisions that, without change, make the part challenging to manufacture. The workflow for the Moldflow analyst is a pretty traditional CAE workflow that may not have fully leveraged all the benefits of modern computing.
With the Injection Molding Simulation technology inside Autodesk Fusion, we have created a complementary workflow for engineers who, although they may only occasionally work with plastic parts, want to provide feedback on the feasibility of manufacturing them through injection molding. This person would typically collaborate closely with designers and answer the question, “Can this part be manufactured?” so they can make improvements as needed. This engineer may not know everything about plastic injection molding (since it’s not their job), but they understand the basic principles and may be involved in decisions like material selection.
Injection Molding Simulation in Fusion
In Fusion, the initial setup, which includes material selection, picking an injection location, and selecting the type of molding process, is automatically done upon entry into the Injection Molding Simulation workspace. This is to help a new user get past some of the initial hurdles to get started while avoiding the perception that everything needs to be perfect to get a reliable outcome. Like any simulation tool, the more thorough the information you provide for the analysis, the more confident you can be in the predicted capabilities. Injection Molding Simulation in Fusion lets you alternately customize the setup if more specific information is known. For instance, if someone has already made some decisions about the injection location point, you can make that adjustment before the analysis starts.
Additionally, suppose you have a few materials your company always uses. In that case, there’s a good chance of finding the exact material grades in the pre-loaded database, which houses over 11,000 materials. Sticking with those default inputs for the analysis, however, will provide good insights to get started with understanding the way your part will mold.
Guided Results and Warpage Analysis
Another area where the Fusion workflow differs from the typical Moldflow simulation is how the user can review the results. In addition to traditional results seen within Moldflow, where users draw their own conclusions, Injection Molding Simulation for Fusion has a “Guided Results” experience that provides the user with answers to the following questions:
1. Will the part fill?
2. Will I have sink marks and weld lines in aesthetically important areas?
3. Will I have problems with excessive warpage?
Injection Molding Simulation also provides targeted suggestions when problems are apparent to resolve them through specific suggestions such as modifying the design or changing the injection location.
Concerning warpage, we have created a new approach that lets users evaluate whether certain faces deform out of plane within a certain tolerance – flatness. This feature allows you to evaluate whether or not to expect problems when assembling two mating parts. The conventional way to look at this type of problem can be labor intensive and error-prone, while this new approach is much more straightforward with “red = out of tolerance” and “green = in-tolerance.”
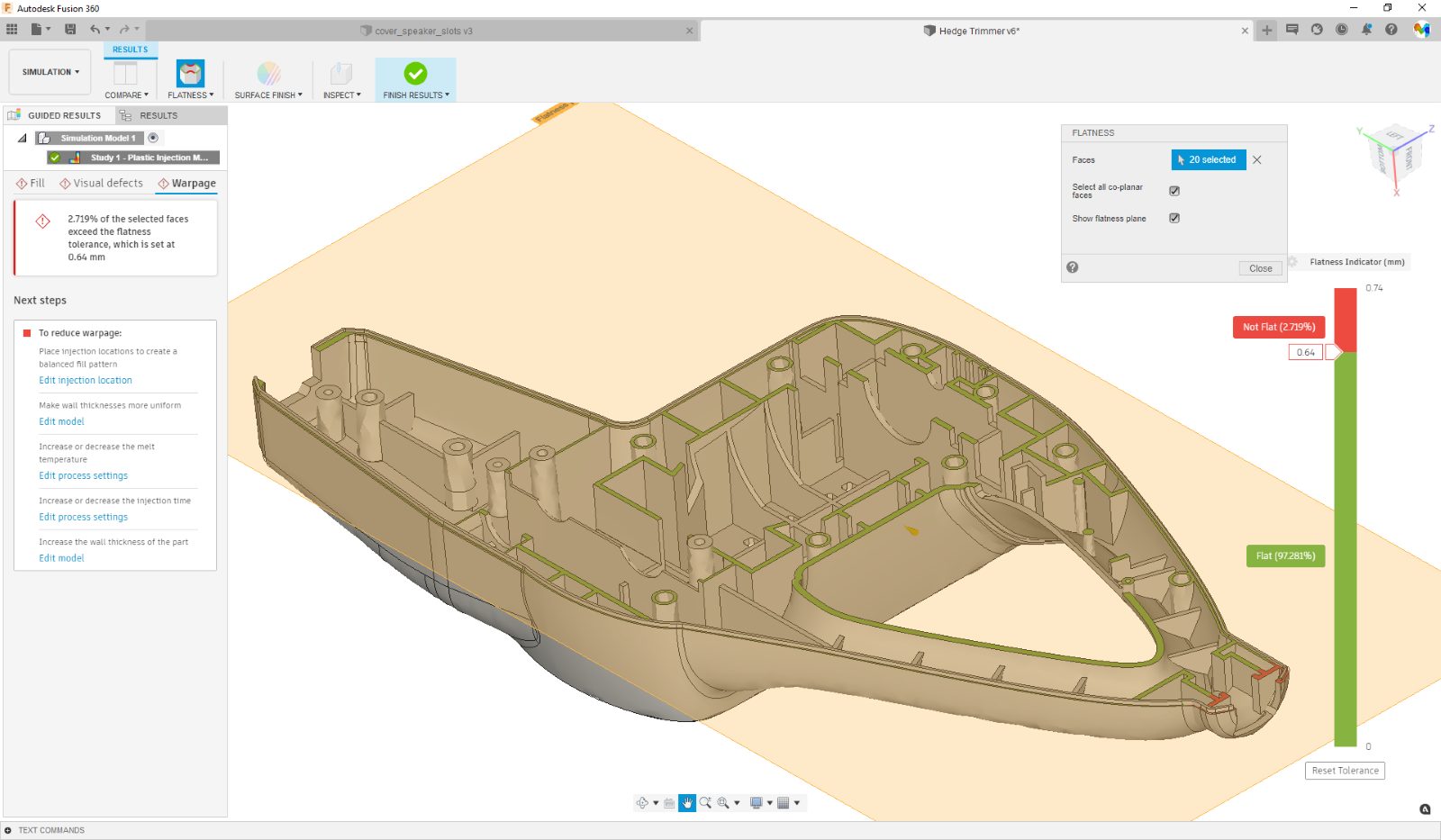
The post processing environment also includes a summary of the findings of the simulation, featuring helpful animations that explain the different stages of the molding process. This summary can also be used to collaborate with others.
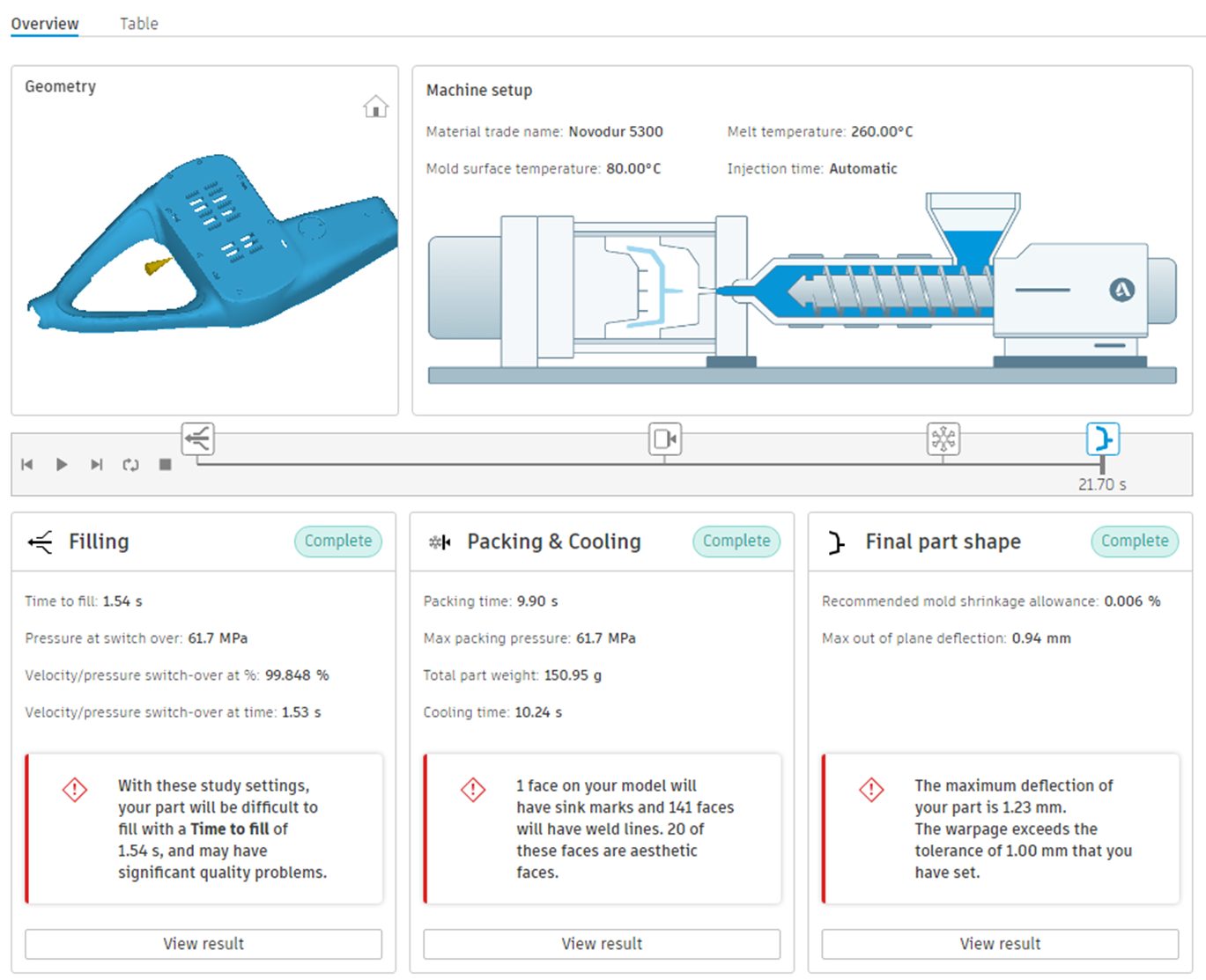
Injection Molding Simulation in Fusion features the typical things you would expect in a simulation workflow; the ability to animate results, probe values of data, compare different design or manufacturing options, and the ability to magnify deformations. However, Fusion users can also benefit from additional powerful features like version control and concurrency to easily collaborate with team members who may have continued to evolve the design.
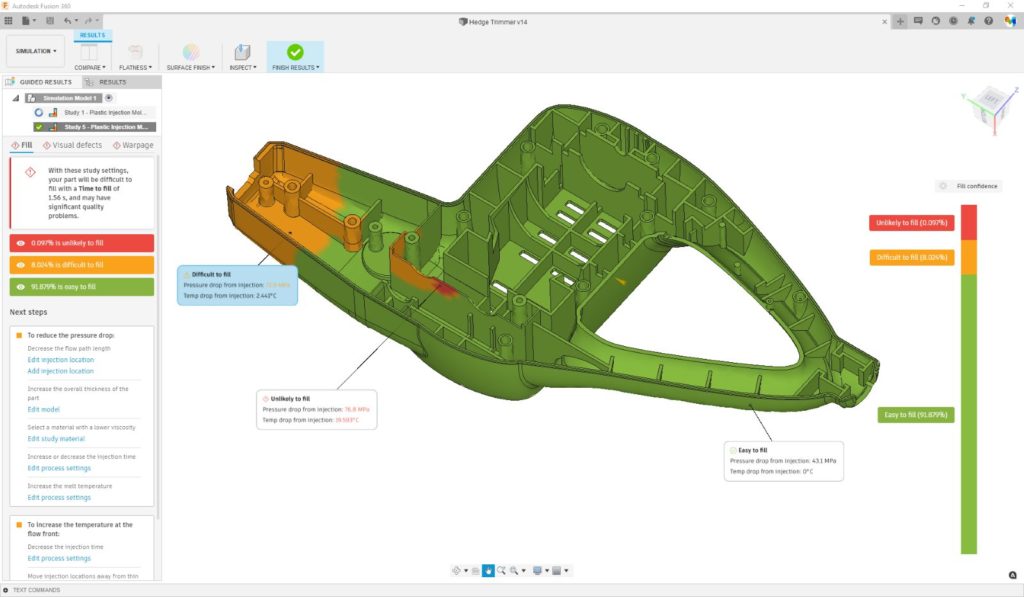
For now, Injection Molding Simulation technology in Fusion is limited to a ‘part only’ analysis and is not intended to address issues related to the mold design (thus no runners, cooling channels, or mold can be added). It’s also limited to the standard thermoplastic injection molding process used for the vast bulk of plastic parts.
As you can tell, the Injection Molding Simulation technology in Fusion is not an immediate replacement for Moldflow products in use today, nor is this the endpoint. Instead, it provides a starting point and a fresh look at providing insights in a more intuitive way. We can build upon this starting point and eventually expand to different users with varying requirements.