
Elevate your design and manufacturing processes with Autodesk Fusion
This post is also available in: Italiano (Italian) Deutsch (German)
In this article, you’ll learn what metal additive manufacturing is, what technologies are available and what metal additive manufacturing capabilities are available in Autodesk Fusion 360.
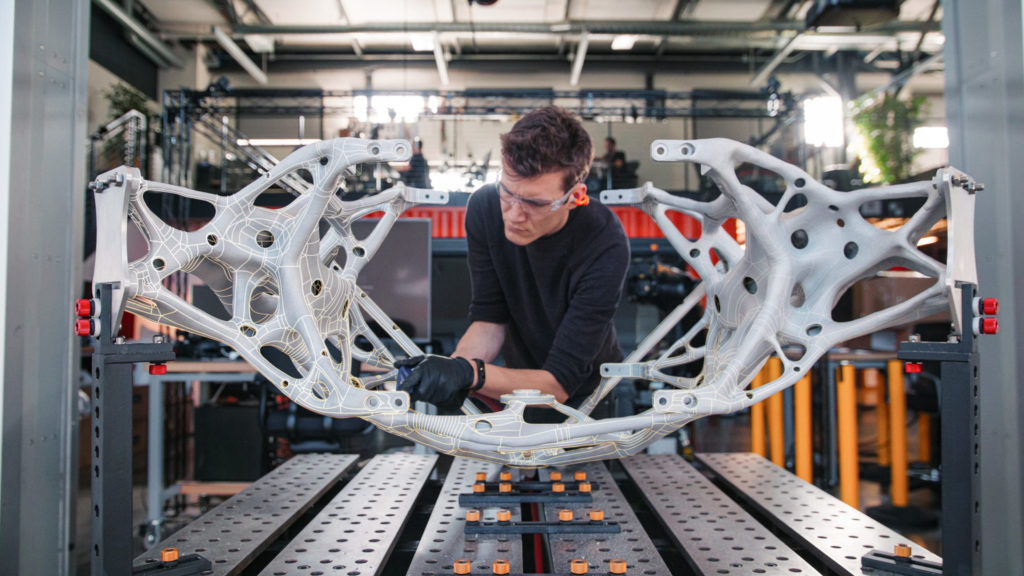
Additive manufacturing is a norm in today’s design and engineering workflows. Designers and engineers have become accustomed to FFF machines because of their accessibility, affordable price points, and because plastic is easy to come by. As the industry evolves, however, we’re starting to see metal applications become more accessible — there are even desktop metal additive manufacturing machines now.
Aligned with this industry shift, Fusion 360 has introduced metal printing capabilities to its additive manufacturing space through extensions. So, now feels like the perfect time for us to talk about metal additive manufacturing — what it is, the various metal additive manufacturing technologies available, and how this process might be helpful to you. Read on to get the full rundown on this exciting technology.
Metal active manufacturing: function and use
So let’s start with the easiest question to answer: why should you care about metal additive manufacturing? Well, the most significant reasons are:
- Higher part durability (metal vs. plastics) for use in prototyping and testing, or even as final parts in production.
- If your final part is manufactured in metal, why not prototype it in metal too?
- Compared to traditional machining, metal additive manufacturing is relatively affordable. It can also be done on your desktop, which takes up less space than a CNC machine and allows anyone to prototype instead of only skilled CNC operators.
If you’re new to Metal additive manufacturing, you may not be aware that there are a multitude of technologies that create metal 3D printed parts, each with its pros and cons.
Powder bed systems
SLM and DMLS
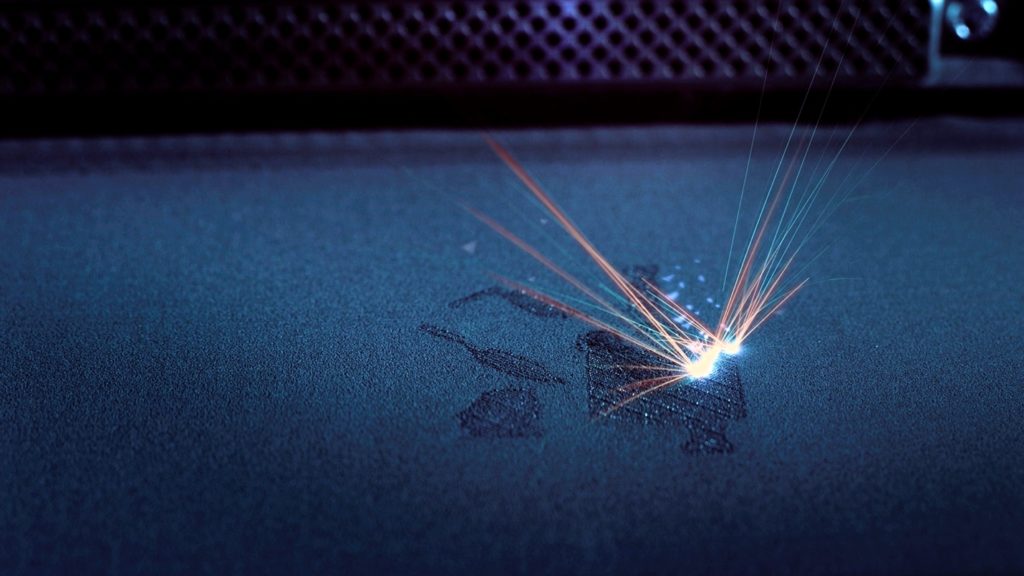
If you’re a seasoned additive manufacturing user, you’re undoubtedly familiar with Selective Laser Sintering (SLS). SLS uses a form of plastic powder in combination with a laser that melts and fuses the powder along the trace of the laser path. As it layers more powder up, it fuses the layer and forms.
SLS is the oldest and most common form of 3D printing that uses powdered plastics. This tech is well developed, consistent, and reliable. For metal additive manufacturing, this technology is either Direct Metal Laser Sintering (DMLS) or Selective Laser Melting (SLM). Both technologies are built very similarly to SLS.
SLM and DMLS use a similar process, binding metal together with a laser, using support materials for overhang angles, etc. This technology is very reliable, well developed, and produces high-quality parts. However, powdered metals are highly volatile, and if not handled properly, can explode, which is unsurprisingly very dangerous.
However, new companies are bringing the benefits of DMLS style manufacturing to the masses, like Xact Metal, at a dramatically reduced cost compared to most other machines available on the market. These machines have considerably smaller footprints than older generations, making them more feasible for most companies.
Electron Beam Melting
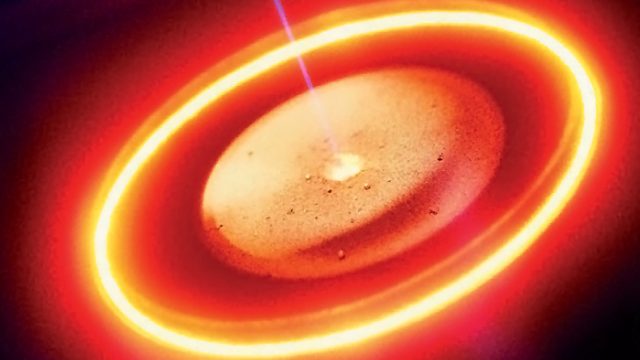
With a fancy name like electron beam melting, it should come as no surprise that this tech is an evolution of laser-based systems as above. The core differentiator between laser systems and EBM is that EBM uses an electron beam. The electron beam fires at the powder bed, which fuses where the beam touches, creating the print layers.
This tech is high-speed and can minimize the amount of potential deformation created in the part by keeping the powder bed heated at a stable rate so that the temperature change is not so extreme as the powder melts together. The trade-off here is accuracy and build volume. Electron beams are not as fine as a laser, so parts are “rougher” than their DMLS counterparts, and currently, DMLS/SLM machines are available with much larger build volumes than their EBM counterparts.
Feed-based systems
Full disclosure, these are my personal favorite machines, not because they’re better necessarily. They look the coolest. Feed-based systems usually work with a spool or hopper of raw material. Spool systems work by melting and laying up in a fashion that will be very familiar to you if you’ve used FFF 3D printers before, but they are, in actuality, more closely related to arc welding.
DED
Hopper-based DED systems work by dispersing metal powder that is melted by the heat source. These machines lay metal down by firing metal particulates from a hopper into the path of a laser beam or electron beam that melts the material together on impact. The jet of raw material is usually shielded with an inert gas to protect it from the oxygen in the air (you know, to stop things from exploding), creating parts very rapidly. DED works by laying molten metal directly down on the built plate, and then the previous layer, building up the part.
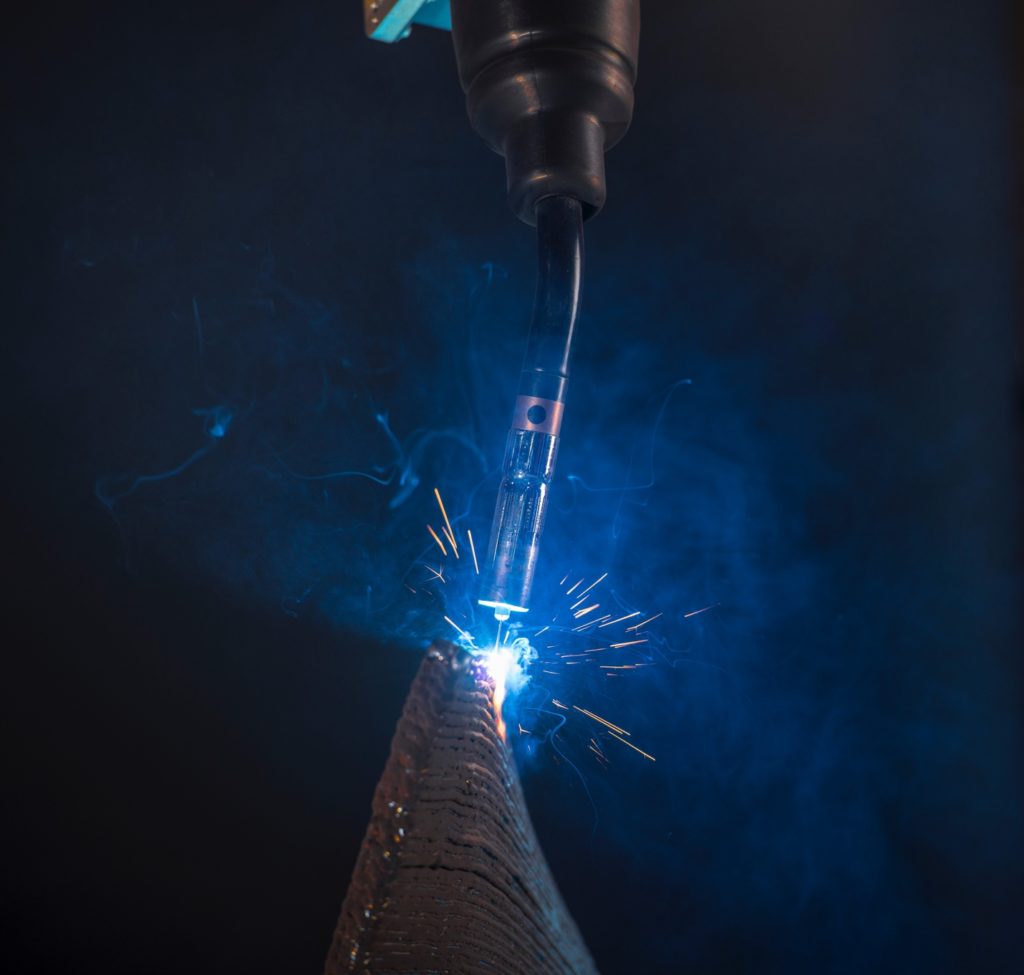
DED systems are easy to deploy and print very rapidly and produce powerful parts as the process has minimal disruption to how the metals crystallize as they cool down. However, parts made using DED typically have very rough finishes. As a result, the majority of DED parts are post-processed in a CNC machine to give them a high finish, but this process isn’t necessary, strictly speaking unless the finished form’s accuracy is necessary (in most cases, it is).
WAAM
Wire Arc Additive Manufacturing (WAAM) is a subset of the DED process but is worth calling out independently. WAAM applies the same principles of DED but specifically uses the technology that makes an arc welder operate. The material layers up by feeding a wire of material to a plate to create the arc. Like other DED technologies, WAAM produces parts very fast with stable material properties, but they’re very rough.
So that’s just a few examples of metal additive manufacturing technologies. More systems are being explored, from firing metal particles at Mach speeds onto build plates to nano-level particles carried through a liquid, fusing to each other as the liquid evaporates to make parts. This process is similar to the incredible tech from XJET or what Spee3D does.
Metal Additive Manufacturing with Fusion 360
As you can see, metal additive manufacturing is an exciting technology with great applications today and exciting potentials for the future. Interested in printing metal parts with Fusion 360? Check out the Fusion 360 Additive Build extension.
