
Elevate your design and manufacturing processes with Autodesk Fusion
In our last post we talked about how you can easily create custom Slotted drills in EAGLE. I have a new tutorial for you on Arbitrary Pad Shapes. Pads provide points of contact for components and play some pretty important roles on your board. They eliminate noise by helping to create a greater connection to the ground signal and help to cool down components by helping to release excess heat.
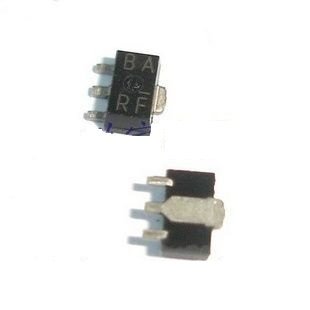
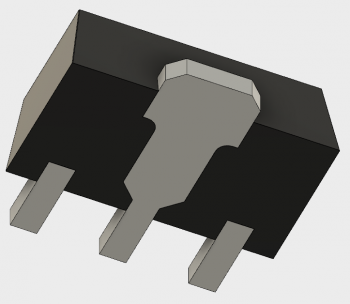
Figure 1 Voltage Regulator SOT-89 Package
This is the STMicroelectronics L78L10ACUTR series, we’ll use it for our example
- max current output of 100ma
- range of output voltages of: 3.3, 5, 6, 9, 10, 12, 15, 18 and 24 volts.
Like many regulators it excessively gives off power causing the devices to get really hot. Let’s get started with it!
Notice a few things here? The center pin, Ground, does not follow the usual convention of SMD landings. In this case the ground pin has an augmented shape to serve multiple purposes. Getting yourself a datasheet for the component in use is paramount, it’ll help get the component created correctly.
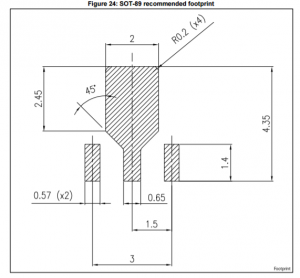
Figure 2 SOT-89 Pad Layout
Example1, we will be using the EAGLE Library Package editor to build this component. From the EAGLE control panel click on File/New/Library. This option will have you reaching the root of the library editor. Click on the Package icon to create your footprint Figure 3.
Figure 3 Creating a package
In the editor, change your default grid to a grid that is a factor of component pad spacing requirements. For this component we figure that the lead spacing would be easily satisfied with a .05mm grid. Use the SMD command, then set the size for the SMD pad .57 x 1.4 mm Figure 4 and place 2 pads with a separation of 1.5 mm for each from the origin of the page. Next change the pad size to .65 x 1.4 mm and place the center pad directly on the center of the origin. As a group we lowered the 3 pads approximately 1.85mm from the origin of the page and the connecting point of the center pad.

Figure 4 SMD Size
The center pad needs to be extended to comply the component specification as explain earlier. The PAD will be covered by a polygon to satisfy the remaining properties of the SMD pad. Doing some basic calculations based on the specification sheet, we are able to calculate the necessary coordinates for the polygon corners Figure 5.
Figure 5 Polygon Coordinate Calculation
Based on this calculation we clicked on the POLYGON command made sure that the top layer was selected. In the command line we entered the coordinates, Figure 6.

Figure 6 Polygon Coordinates
The polygon and the SMD command will be treated as the connecting pad on the board editor, the connecting point of this pad will be the connecting point of the pad. The drawn polygon becomes an extension of the PAD. On the board editor, the polygon drawn in the library will be treated exactly the same way as a regular pad, for then, all DRC setting will be taken into consideration. The final product will look something like this, Figure 8.
Figure 7 Completed Pad Layout
Only a few more steps to complete this component! Using PAD and SMD pads automatically calculate solder mask and cream mask. If you use polygons to draw custom pad shapes, the solder and cream mask will not be created. We decided to calculate the coordinates of our polygon because we will be drawing the same polygon a few more times for the TStop and TCream layers. Final component looks like the component on Figure 8.
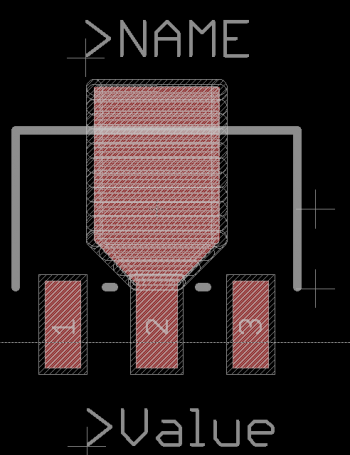
Figure 8 Completed component with Solder Mask and Cream Mask
Thanks for following the EAGLE blog!
Please contact us with inquiries, comments and suggestions.
Until Next Time!
EAGLE Support Team
support@cadsoftusa.com