While the use of BIM has grown massively in recent years, too frequently it appears to start from the ground up, with the geology and subsurface being ignored. This is a significant omission as the whole premise of BIM is to reduce costs by reducing risk at the early design stage and throughout the lifetime of the project.
Unseen subsurface ground conditions are among the biggest areas of risk and uncertainty in any construction project. In fact, it has been reported that over a third of construction projects that overrun cite unforeseen ground conditions as a major contributor to the overrun. BIM principles can be applied to geotechnics to help reduce uncertainty and produce a better site investigation which is fit for the project and ultimately will help to reduce risk and cost.
This article looks at how the core BIM principles of data sharing, collaboration, and process can be used and applied to the geotechnical process, illustrated with the London Silvertown Road Tunnel case study. It will highlight the use of tools, like AutoCAD Civil 3D and Navisworks together with HoleBASE SI, for combining information from previous projects together with a wide range of other data sources, maps, drawings, and models. This leads to a better understanding of the site and improved processes to model and visualize geology and subsurface data with the wider team, which will ultimately help to reduce risk and save money.
“The use of a fully integrated, multidisciplinary Civil 3D model, including subsurface geology, has been a real eye-opener for the team. By visualizing ground conditions in a design context, we can reduce project risk and project costs during construction.” –Simon Miles, Principal Geotechnical Engineer, Atkins
Traditional Process
Many geotechnical professionals work within a process that has been developed over time. Even though they think and visualize in 3D, information is passed through traditional means via reports containing 2D site plans and log sheets. The next person in the design process has to decipher the information and again try to understand it and visualize it in 3D.
If we take a look at the development of CAD through to the current BIM working practices, we will see how the technology has evolved from the initial replacement of the drawing board through to more automated drawing and eventually through into full 3D BIM. We can compare this to the evolution of software within the geotechnical industry. Originally borehole logs were drawn by hand, then graphic software was developed to aid the drawing of the logs, and in time, software added data management to allow borehole logs to be printed at a touch of a button. This is where it ends for many… the production of a Log. The Log is an important document as it contains the important information, but ultimately it is either a piece of paper or a PDF file and the data within it cannot easily be reused or analyzed.
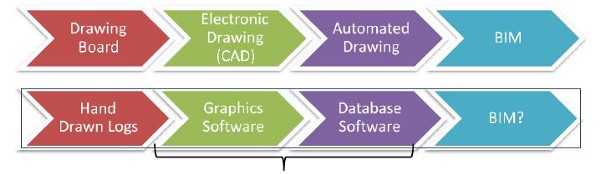
For the geotechnical information to be used again in the design process, information has to be relearnt and often re-entered from the reports and logs, this is a slow, time-consuming process prone to error.
BIM principles (Process, Collaboration and Whole Life) together with the enabler, 3D Digital Data, can be applied to geotechnical engineering. The process is illustrated by highlighting the benefits experienced by the proposed Silvertown Tunnel project team.
Definition of BIM
The manufacturing world claims the origin for BIM. Years before an item went into production, numerous prototypes would be designed and tested. Electrical and mechanical designers would come together to see how they could work more collectively to improve the prototype over a number of iterations before the first version would go into production. The manufacturer would keep the item’s data and model to feed into any improvements required through the whole life of the component.
This process cannot be fully replicated in construction as a tunnel, road, building or other infrastructure cannot be built, refined, demolished and rebuilt. However, in the virtual world, using the right processes and methodologies, a virtual prototype can be built using components from different civil engineering disciplines. This virtual version of the project can then be used to refine the design and construction process and kept to assist with the lifetime maintenance of the structure.
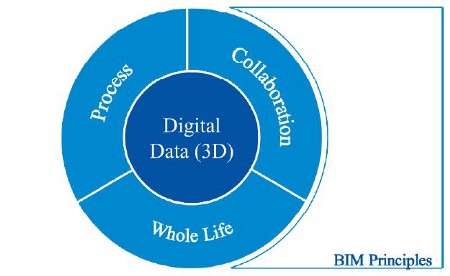
BIM can be broken down into three main principles and a digital data enabler when applying it to geotechnical engineering:
Process
BIM requires agreed repeatable procedures, methods and workflows, to allow data and information to be quickly captured, processed and shared.
Collaboration
Many of the benefits of BIM are obtained by visualizing and analyzing data in context with information from other disciplines, thus ensuring engineers see the big picture and can make decisions that are more informed.
Whole Life
Refers to retaining and building on data and knowledge collected over the life of the project so that it can be reused and refined. In a non-BIM environment information is often lost and has to be relearnt at each stage of the project. By managing data and knowledge, it can be used throughout the life of the structure and possibly in future projects.
Digital Data (3D)
Digital data is the core and enabler that allows the benefits of BIM to be achieved. For BIM to succeed, common agreed formats need to be used. For geotechnical data, the UK and various parts of the world are blessed with having mature agreed standards, AGS (Association of Geotechnical and Geo-environmental Specialists). In the United States, the DIGGS (Data Interchange for Geotechnical and Geoenvironmental Specialists) format is starting to emerge as the preferred format. Both formats enable the transfer of geotechnical and geo-environmental data within and between organizations. When utilizing data interchange standards, compiling geotechnical data requires importing the data from the data interchange file into the chosen geotechnical data management system.
One of the main benefits of BIM is the cost savings generated by using the virtual prototype model to highlight and remove potential problems before the construction stage, in essence helping to visualize problems which before may have been unseen. Better understanding and subsequent refining of the project from the collaboration of design data helps to minimize problems later in construction.
Problems identified and resolved at an earlier stage cost considerably less than rectifying them later in the construction process. This is highlighted in the MacLeamy Curve which illustrates the ability to reduce a project’s costs if informed decisions can be made earlier in the design stage.
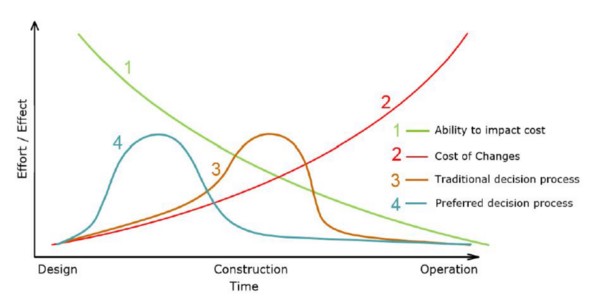
One of the standard usages for BIM is highlighting where objects from different disciplines might intercept and cause problems during construction (often called Clash Detection), for instance in a building the ventilation ducting may clash with a structural beam. This problem is heightened by ongoing changes in the design with different disciplines working, unknowingly, with out-of-date data.
The same process can be applied to geotechnical engineering, for example, a road cutting being realigned into different, or difficult, ground conditions that has a significant impact on the construction process.
The Silvertown Tunnel Project
Transport for London (TfL), the statutory authority responsible for most aspects of Greater London’s transport system, is planning a new road tunnel under the River Thames in East London. The proposed Silvertown Tunnel between Silvertown and North Greenwich will ease the strain on the nearby Blackwall Tunnel and other existing crossings. Engineering and design consultancy Atkins developed the project’s reference design.
There are many challenging problems in the area; the south portal of the tunnel route is the site of a demolished gas works. The soil in that area is contaminated and there are still remnants of the underground foundations of the plant. On the south and north banks, the proposed tunnel location comes close to the pylon foundations of the Emirates Air Line cable car. Additionally, the north bank tunnel portal is in the area of the now-filled western entrance to the Royal Victoria Dock and some demolished warehouses. Like the gas works on the south bank, there are still underground remnants of these features.
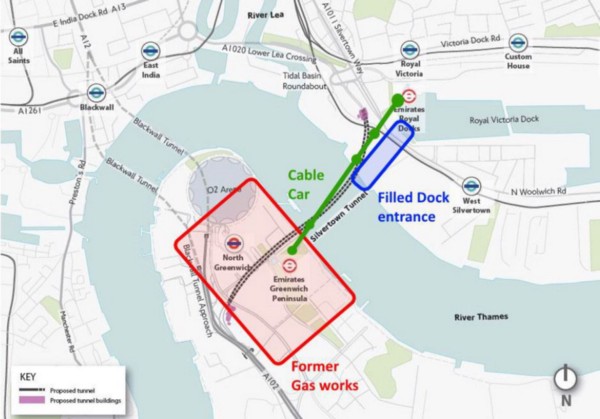
The route of the tunnel will need to thread through heavily industrialized areas of London; areas which contain many different ground conditions, roads, foundations and other subsurface structures.
Atkins realized that to reduce the overall project costs and risk they needed a better way to visualize and understand the ground conditions in context with existing built conditions and wider site challenges. One example was to have a better way of estimating the quantities of contaminated ground that will be impacted by construction. The costs of treating contaminated materials makes accurate volume calculations vital for assessing cost implications.
The BIM Approach
Atkins, the geotechnical engineers, knew they had a lot of existing information available for the site, from historic maps to more recent digital data from recent projects. They realized that by using this information it would be a sizeable aid in understanding the site conditions and allow them to design a refined site investigation building upon the existing knowledge.
Atkins decided to take a two-pronged approach to the project, collating the existing geotechnical knowledge in a geotechnical data management system, and at the same time developing a 3D ground model of the site and ground conditions. The two were then integrated to generate a 3D geotechnical model with the intention of constantly refining the geotechnical data and model throughout the whole process from preliminary investigation, full site investigation, design and onwards.
Geotechnical Data
For many years Atkins have embraced geotechnical data management, using standard methods and processes for managing their various geotechnical jobs. The use of standardization enabled them to collate geotechnical data from various projects in the area, coupled with AGS format digital data supplied by the client.
Historic Maps
Various historic maps and plans were available including old plans for the demolished gas works, warehouses, and piers and foundations of the old dock entrance.
3D Models
The project team also had access to, or created, a number of 3D models, including the proposed tunnel alignment together with other proposed structures relating to the tunnel.
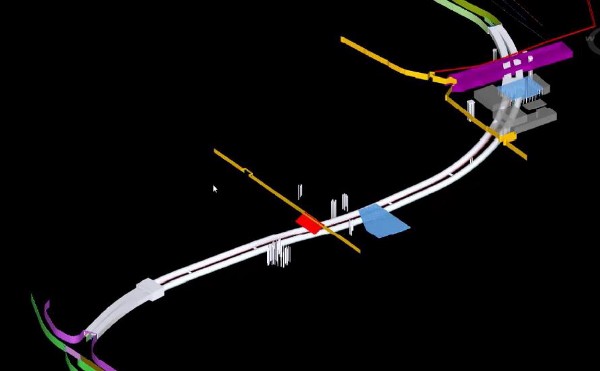
Due to the client’s approach to whole life BIM on previous projects, the team were also able to obtain the as-built data for the cable car foundations.
Geotechnical Data Management
Atkins collated and imported geotechnical data from the previous projects into the new project within their already established geotechnical data management system, HoleBASE SI developed by Keynetix. The process was relatively straightforward as the data was available in the common AGS format allowing them to take advantage of a standard method for sharing that digital data offers. Atkins had to ensure that a common datum was used across all imported projects together with standard geology classifications.
The DIGGS format will fulfill this function in the U.S. in the near future; however, in the meantime, each project team must agree on processes and workflows.
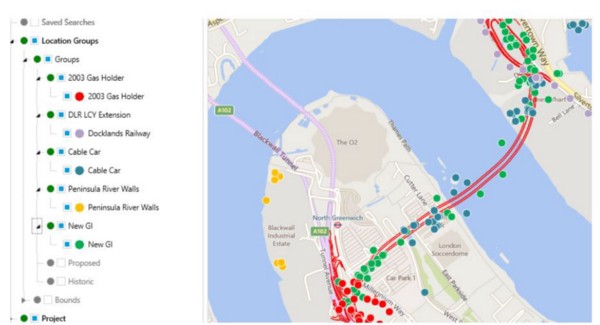
Historic maps from Ordnance Survey and geological maps from the British Geological Survey were also combined into the geotechnical data management system, building up a mosaic of known information around the site. By having easy access to past data in conjunction with seeing it in context with the environmental and geotechnical data allowed them to design a refined site investigation, building upon the existing knowledge.
In parallel, Atkins used AutoCAD Civil 3D to create an existing conditions model of the project area (both above and below the surface) based on a variety of data sources such as TfL’s as-built data for the cable car foundations, and historical data for the demolished gas works foundations, warehouses, and piers and foundations of the old dock entrance. The proposed tunnel alignment was added and other proposed structures relating to the tunnel.
One of the advantages of using a common drawing format like DWG, much of the data was already in the format, for the data that was not it was relatively easy to convert to it. Before combining all of the datasets into one ground model, Atkins also had to ensure that they all used the same coordinate system and datum.
As the information was created it was also combined together within Navisworks to allow the collaborating teams to see how the model combined.
Combined Geotechnical Model
As Atkins had used HoleBASE SI it allowed for the geotechnical data in the system and to be easily integrated with AutoCAD Civil 3D. It also enabled the geotechnical data from the management system to be visualized within the 3D ground model and gave them the ability to quickly combine, organize, and manage geotechnical data in the context of the existing and proposed above and below ground structures, again helping to improve and refine their knowledge of the site.
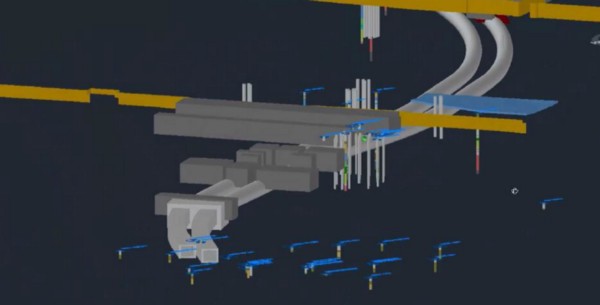
The software used allowed subsurface models representing the geology strata to be created inside AutoCAD Civil 3D directly from the geotechnical data stored in HoleBASE SI. The initial model, automatically created, needed manipulating and cleaning up. This process was carried out by the team using all available contextual information together with functionality within the chosen software.
The big advantage was that it helped the team to visually understand and evaluate the design alignment, pinpoint potential construction obstructions, and determine what new site investigations were needed. By analyzing the historical and available data within the model environment they reduced the number of exploratory holes required for the site investigation, which translated into reduced project time and cost for the client.
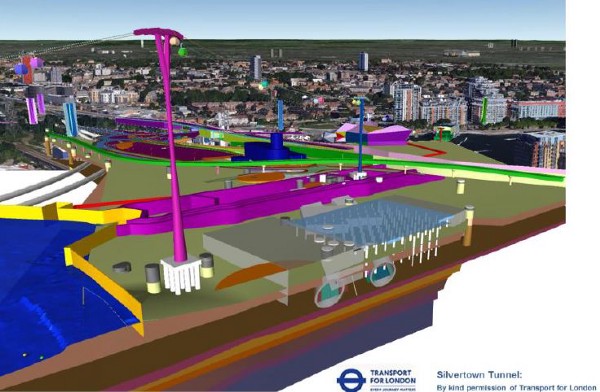
As the project progressed into the site investigation stage, the new site investigation data was added to the project in the geotechnical data management system, and used to further refine the 3D geotechnical model to enable better understanding of the ground conditions.
The dynamic link between the HoleBASE SI geotechnical database and the AutoCAD Civil 3D model, which allowed them to have a rapid workflow and enabled updated geotechnical data to be quickly viewed in context with the wider model. The savings in the time required for recreating or manually synchronizing the geotechnical data and 3D model gave them more time to further refine and improve the project design. Moreover, it also helped to automatically generate earthworks and contamination quantities for project costing and risk assessment.
Advantages of Collaborative BIM
Once a federated model had been created within Navisworks it was clear how the geotechnical BIM approach would benefit the wider construction team. It became clear to the structural team that once the approach ramps slab was incorporated with the geotechnical model the groundwater conditions would cause problems with their current design. The federated model including the geotechnical material has also been used to generate the necessary sections for the acoustic analytical software.
The project is still in the design stage, however when it reaches construction there will be a number of distinct advantages that the BIM approach has facilitated. The 3D geotechnical model can be passed on to the construction team allowing them to quickly build on existing data and reduce the time and cost of increasing their own knowledge.
The 3D geotechnical model will provide a distinct baseline for the construction team to compare their findings. If differences are seen during construction it will be possible to incorporate them into the model and any potential consequences can be better predicted and managed.
Conclusion
Atkins have found the use of a fully integrated, multidisciplinary model, including subsurface geology, to be of significant value for both the geotechnical engineers and the wider design teams. By visualizing ground conditions in a design context, they have potentially reduced project risk and costs during construction.
The client did mandate the use of BIM as an overall concept for the project, although it was the team’s decision to apply BIM principles to the geotechnical process in particular and generate the 3D geological model and in doing so they have found many benefits from it, including:
- The visual model allowed a better understanding of the site and enabled them to pinpoint potential construction obstacles.
- The model allowed them to improve their estimates on earthwork and contamination quantities.
- The use of existing client knowledge and BIM data led to a significant reduction in the number of new exploratory holes required.
- Streamlined workflows saved time and effort in updating and integrating data.
The project team is finding more uses for the geotechnical model across the wider project, which should ultimately lead to cost savings for the client and protection of geotechnical knowledge.
Gary Morin originally trained as a civil engineer and has over 30 years of experience working in the production and support of a range of geographic information and CAD software systems. He is now the technical director of Keynetix, which he co-founded in 2000 to specialize in geotechnical data management software.